Mild climate; expensive cellulose — What to do?
I am getting ready to go to Engineering for a new house in Raleigh, NC.
HDD – 3247 and going down….On border of zone 3 and 4. Technically in 4 but 20 miles from the 3/4 border.
Being in the South, everyone worries about cooling but we usually have 3x the cost in heat (based on last energy audit).
The house has a good amount of South windows. We are planning 2×6 construction and 24 O.C. I’d prefer to not do foam in the walls. Cellulose is looking like a $4,000 upcharge – for a 3700 sqft house. This is comparable to OCF. I am still waiting for the exterior rigid foam quote but it should be quite close – I’m guessing a little lower.
So here are my options –
– R19 batts
– R19 batts + 1 inch foam
– Foam or cellulose in 2×6
In a larger house with more windows that were less optimally oriented and R-13 walls, the heating bill is around $500 a year. Hard to get an exact number because of dual fuel. I anticipate the air sealing to be better this time around – we plan zip walls and are shooting for an ACH of 1-1.5 when the last house was more like 4. And all ducts will be in conditioned space – probably between floors. So I’m thinking with batts we will be more like $300 a year.
I’m perfectly happy with a 30-50 year payback but no more. I am also willing to pay more for sound control. But it seems hard to justify $4000 for cellulose or rigid exterior foam because I am thinking somewhere around $50 a year savings…..
We have $.05 per kwh at night and will likely use a heat pump and a minisplit or two. I am anticipating 2 ton heat pump with a minisplit for the master bedroom. So there is no where to save on equipment costs.
So is a pretty good house in central NC, R19 batts? And then otherwise – shade and window orientation and air sealing.
GBA Detail Library
A collection of one thousand construction details organized by climate and house part
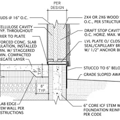
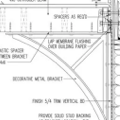
Replies
User-6902085,
Can you tell us your name?
John is wrong about the need for 2 inches of exterior foam for a wall in Climate Zone 4. There is no minimum thickness for wall foam in your climate zone. For more information on this issue, see Calculating the Minimum Thickness of Rigid Foam Sheathing.
If you can afford it, I think you should spring for the 1-inch exterior rigid foam, for a variety of reasons:
1. R-19 batts won't perform at R-19 because of thermal bridging through the studs;
2. R-19 batts are usually installed in a sloppy manner, with all kinds of voids;
3. Energy may not be cheap forever;
4. The rigid foam will probably reduce air leakage;
5. It's the right thing to do from an environmental perspective.
However, you may be right that the investment is hard to justify from a purely economic perspective.
Edit: Inaccurate information deleted by poster
2015 IEEC is R20 cavity or R13+R5(exterior foam) for CZ 3, 4, 4 marine and 5.
Low density R19 batts are really R18 (at center-cavity, not whole-wall) when compressed to 5.5" (nominal 2x6 depth). They're real junk, and not even code-minimum, but they make great mouse-nesting material! :-)
As John correctly asserts, IRC 2015 code minimum for zones 3-5 really DOES spell out R20, not R19 (that's really R18, which is 10% below code performance.) See:
https://up.codes/viewer/general/int_residential_code_2015/chapter/11/re-energy-efficiency#N1102.1.2
Now that R20 is code-min it shouldn't be too hard to find mid-density R20s, and the upcharge from R19s should be very small.
R20s now being manufactured in high volume, and actually perform at their rated R20 in a 2x6 wall (when installed properly.) They are also more air-retardent, and less susceptible to convective heat transfer within the batt at the temperature extremes than R19s, but still not as air retardent as cellulose (any density) or high density fiberglass.
For a bigger upcharge you can get high density R21HD "cathedral ceiling" fiberglass, or R23 rock wool batts, either of which are sufficiently air retardent that they really don't need tight air barriers on both sides to hit their rated performance- one side is enough. My personal preference is R23 rock wool, not for the higher R, but for the better fire resistance (fiberglass can melt in a fire), and less potential for friable fiber suspended in the indoor air.
But sprayed/blown cellulose or fiberglass will always be a more complete & perfect fit, even compared to the most obsessive of batt perfectionist installers. Cellulose also adds a measurable amount of thermal mass over the fiberglass & rock wool options too, equivalent to going with fatter wallboard, and being 85% recycled material, a greener product overall.
BTW: Using construction adhesive or polyurethane caulk to seal standard OSB / CDX sheathing in every stud bay can be at least as air tight as ZIP. Depending on labor costs that approach can cheaper overall. Be sure to lay a bead of caulk between any doubled up framing such as jack studs top plates, and between the bottom plate and subfloor etc too (even with ZIP.) With a powered caulking gun it goes a lot quicker than you might think.
OP here - name is David.
Code for us is still 2012. Even the upcode (HERO it is called) allows R19, the normal is R15.
I should have listed upgraded batts as an intermediate option. I was always planning to do at least R21. That is about $500 just based on big box material differences.
Does the thermal mass in a 5.5 inch wall mean much? We are humid without large diurnal variation. 30 degrees is on the high end. Winter typical is 50/30. Today is 95/75.
There is the possible argument that energy costs will go down of course. I already discount summer time electricity cost because of better solar. Since we don't have much installed wind (any?), winter is a bigger problem. My highest electricity bill is December - PV generates less, 2 EVs using more, heat pump, electric back up for solar hot water. Environmentally of course, you can add rigid foam and have it never recover its production if offshore wind or tidal is your source in 15 years.
We had a discussion last night and are leaning towards cellulose - partly for the sound control. There is also the power outage stable temp argument. Builder likes Zip because the house wrap is always wrong.
On hot water, today, what would you do? We use 30 gallons a day by my estimation. The mechanical room (in good proximity to fixtures) will be an insulated part of attic (probably). It will not be conditioned intentionally. I could do a heat pump hot water heater here, do solar or do some NG option. (If we don't do NG, then we will probably switch to propane for cooking only use)
Financially, Duke power gives incentives in addition to federal. It is unclear how much they are yet but it is possible solar is down to $2500 or so. There is a decent amount of marginal roof area - like west facing over the single story part of house with a large deciduous tree 80 feet away. Not ideal for PV but probably adequate for solar thermal. I am torn on using this RE for thermal vs PV though. The Duke incentive doesn't cover PV but does pay $.90 for saved annual KWH which can be pretty high with solar hot water. May pay for some extra insulation in the walls also.
Thanks for your help.
EIFS is an easy way to add 2" of foam to the exterior. It includes a liquid-applied barrier that is far superior to house wrap and contributes as air barrier too. Thermal break of course makes interior insulation more effective. Installed price is about equal to material price of Hardie-plank options (in East Tennessee).
@David McNeely - if you add EIFS, (true EIFS) you may have a problem getting insurance due to it's bad rap. Also, don't most EIFS systems now have a rainscreen BEHIND the exterior foam, thus making negating any insulation value of the foam?
The thermal mass effect of 5.5" of 2lbs+ density cellulose is measurable, but small in terms of annual energy use. But it both lowers & delays the peak interior wall temperature from direct solar gains through the wall. The difference in comfort level is hard to predict (there are other elements of the stackup, the exterior paint coler, and shading factors to consider), but it doesn't necessarily take princess & pea type sensitivity to feel the difference on a sun-drenched west facing wall, due to the partial translucency of low density fiberglass to deep infra-red. It's still pretty subtle.
The difference in air retardency between R19s and cellulose (any density) is almost an order of magnitude.
The difference in sound transmission about about 10 decibels (3-4 STC) lower for 5.5" of cellulose compared to 5.5" of low density fiberglass.
Heat pump water heaters do take a useful bite out of the latent cooling load. If it's in the attic the effect isn't as much as if it's in the fully conditioned space, but it's still in the right direction.
If the main shower is above a full-depth floor/basement or deeper crawlspace, a drainwater heat recovery heat exchanger may be "worth it", though I doubt Duke is willing to subsidize it. (In some cold water states utilities will sometimes subsidize it.) The bigger advantage for drainwater heat recovery is to be able to down-size the heat pump water heater and still have reasonable "apparent capacity" for showers. The upfront cost difference between a 50-60 gallon heat pump water heater and a 75-80 gallon version is more than the retail price of a 4" x 48" (about 50% heat recovery efficiency @ 2.5 gpm) or larger heat exchanger. The biggest one that fits is usually the better "deal" from a "payback" point of view. The installation labor cost is about the same, but the heat recovery efficiency improves with both length and diameter. The maintenance is effectively zero (unlike solar thermal systems.)
The main shower is unfortunately over a crawl with not enough room. 3-4 STC is great of course but what about compared to high density batts? I'm guessing the HD batts are 1/2 way in between.
Thankfully, I've limited the west facing walls. There is garage to the west and a peaked roof eats into the upstairs west. There is also a large shade tree. And when I say large, it is wider than the house. I will vegetate any other west faced walls if they aren't shaded adequately.
The word is that cellulose is coming back significantly higher than OCF. Ouch.
With HD batts the sound transmission can be even higher. With any batt solution key factors are the air tightness of the wall, and just how obsessively-perfect the installation is. Any gaps at the batt edges become both a thermal and sound bypass. With blown fiber a near-perfect fit is pretty much guaranteed.
Is blown fiberglass any cheaper than cellulose in your area? (It's usually more expensive in my neighborhood.)
The shortest drain water heat recovery units tend to be 30", though there are some 24 inchers, which works for some crawlspaces. A 4" x 30" will typically return 30-35% of the heat back @ 2.5gpm under standard Natural Resource Canada test protocol conditions. At lower flow rates it's a bit higher.
DIYer: when we had some walls open awhile back, we upgraded the old fiberglass (nasty stuff, talk about friable fibers) to r23 roxul. We were really shocked at the reduction in ambient sound transmission. But one caveat: I'm a really obsessive installer.
Whichever better stc insulation you go with, it will be worth the modest up charge.
One other note: HD pro desk now sells roxul comfort board in modest quantities. It is substantially more expensive than foam and a touch harder to mount flat but is fire resistant and does more (naked opinion here) to cut sound from outside. It does nothing to very little for air leakage though.
Good luck!