Michael: Need Help with Maine Codes

stephenr
| Posted in GBA Pro Help on
Michael,
There is a new code officer in Waldoboro and he is trying to do a good job. He is earnest and by the book (but open to learning), and is unfamiliar with high performance building. He is referring my plan for either a raft slab or a fpsf to the state fire marshall ( a bad sign), and needs MUBEC code references. He also states that the ICC code book for green building, IgCC, is not on his list for approved building codes.
Specifically, he doesn’t think that the code allows EPS foam under the thickened edge portion of a monolithic slab. He sees a raft slab, with foam underneath the load bearing thickened slab, in the same way. So, no insulation under footings, as he puts it.
Could you perhaps shed some light on this?
Thanks again,
Stephen
GBA Detail Library
A collection of one thousand construction details organized by climate and house part
Search and download construction details
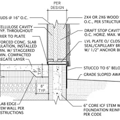
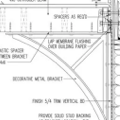
Replies
I don't live in Maine, nor do I work there, but FSPFs are in your amended 2015 IRC as far as I can tell: https://up.codes/viewer/maine/irc-2015/chapter/4/foundations#R403.3
What kind of building are you building? You mention insulation under footings, but in a heated building, you seem have prescriptive options in the code, though they don't include sub-footing or sub-slab insulation.
Thanks Patrick.
Its a heated, double stud wall, single pitch 3/12. In looking at the Fpsf codes, there only seems to be horizontal insulation allowed exterior of the frost walls. These are, no doubt, the codes that the CEO is going off of. Most folks are doing wings instead of this and sub slab insulation extending beneath the thickened edge of a slab seems to be a standard high performance building technique. I am trying to avoid frost walls because I want lay my gravel bed this fall, allowing it to go through the freeze and thaw cycles and get solid over the winter. This way, I can start building in the late spring without having to let the ground dry out first.
I am also trying to avoid having to do a traditional fpsf in order to eliminate the thermal bridging that would happen as cold moves up the footings and into the slab. But with the code official never having heard of high density EPS foam, it could be an uphill battle.
My process for putting foam under footings, including relatively high load spot footings has been:
1. Get more detailed engineering data from the EPS product rep. In the PNW I've worked with Insulfoam, and they were quite helpful in this regard.
2. Give the engineering data about the foam to my structural engineer so that they can specify the required density of foam. The engineers I work with are sometimes hesitant about this, but I found that once they had all the data about the foam (usually more info than was initially available in the cut sheets from the website), they were willing to do it, although they sometimes picked a denser foam than I expected in order to be conservative.
3. Include the stamped engineering drawings and calculations in the permit drawings. The code reviewers and inspectors I've encountered have all been willing to trust the engineers calculations regarding foam under footings.
YMMV of course. And if you're trying to do this prescriptive path without a structural engineer, you may have more of an uphill battle.
Alternatively, sometimes it's easier to design the building such that you can have a well insulated foundation without having to put foam under the footings. Always worth taking a second look if you can rethink the detail to avoid the issue entirely. Your flooring costs will go up, but you could always put the foam above the slab. And if you've got the budget for it, being "forced" to do a wood floor might be a nice upgrade. On the other hand, if that breaks the budget, obviously that's not a great solution, and it might be cheaper to hire an engineer to design the foam and foundation.
Waldoboro is unique, the only municipality in Maine that requires a licensed architect on every project. Even Portland allows unlicensed heathens like me to design 1 and 2 family homes.
On a few occasions I have had to get a licensed engineer involved on FPSFs and other situations that aren't 100% "normal." If the plan reviewer is technically competent, such as a former architect or engineer, sometimes they have accepted my detailed calculations, but it's getting more rare.
My main argument in your situation is that there is nothing in the code that prohibits foam under footings, or for that matter, using concrete for slabs. The code allows footings to be on soil with a bearing capacity of 1500 psf (https://codes.iccsafe.org/content/IRC2015/chapter-4-foundations#IRC2015_Pt03_Ch04_SecR401.4.1) which is 10.42 psi. Even the lowest-density EPS commonly used in construction can support 15 psi, almost 50% more than the soil.
However, for foam, engineers use a 0.30 adjustment factor to account for long-term creep, so prescriptively, under footings the foam should be at least 10.42 psi / 0.30 or 34.7 psi. When I do the calculations, unless there is a huge point load, 25 psi foam has always been enough to support the actual loads. But 40 psi foam is available that would exceed any situation the prescriptive code covers.
Manufacturers should be able to provide the engineering specs such as psi rating and ideally the creep factor. I'll attach the spec sheet from a product I use, and the ASTM table that all foam conforms to.
The state fire marshal is Paul Demers. We have had several conversations but I don't know that he'd remember my name. By all accounts he's a good and reasonable guy, if overworked in a difficult role.
I might have your email address but if you send it again I'll send you contact info for a licensed structural engineer who is on board with everything green and would likely sign off on your design, which should supersede the inspector's authority, or adjust the design to be acceptable.