Metal warehouse/shed retrofit

We’re converting an old Butler metal clad warehouse (or storage shed) into a house. Due to local zoning codes, we cannot tear down the existing envelope. This is an urban location and the adjacent building walls are a mere 3″ away.
The idea is to keep the existing corrugated steel panels (which are not leaking) and spray closed cell foam as both air & water barrier; to a thickness of 2″ clear of the corrugation. Then we would tilt up sections of wall between the horizontal purlins that are @ 7ft vertical spacing (~ 20ft clear height).
The walls would be made up of (going from outside to inside) 1/2″ plywood (for shear), 5/8″ sheetrock, 2×4 studs with open-cell foam, and finished interior sheetrock.
We were thinking of adding a waterproofing membrane on the outside as a belt & suspenders insurance, or would the closed-cell foam be sufficient? The existing envelope shows no signs of leakage.
Are we approaching this correctly, or have we missed something crucial? Any input will be greatly appreciated.
Terl
GBA Detail Library
A collection of one thousand construction details organized by climate and house part
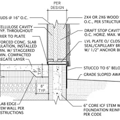
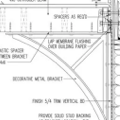
Replies
Probably be best to add some info. We're located in San Francisco where it's never really hot, or really cold. The only difference between summer and winter is the night time temp. Only have a few days where it gets past 80F, and then it cools down to 70F or less at night, so cooling is not an issue. Doesn't ever freeze; frost maybe once or twice. Humidity levels pretty high (fog).
We could go with 2x6 studs, but the 2x4's would better fit within the purlins while still leaving a 1" + airspace between the close-cell foam and sheathing.
Terl,
A few quick reactions:
1. Is there any reason that you need exterior gypsum wallboard? I'm guessing that this has something to do with fire regulations -- yet one might think that the metal siding panels would take care of those issues.
2. I think that installing spray foam against the metal siding is a bad idea -- because it makes siding replacement impossible. (Well, the 3 inches of clearance to the neighboring building is another problem, I'll admit.) Why not just build a new shell inside the old, leaving an air gap between the new walls and the existing metal siding?
Martin,
Yes, the gypsum is because of building code fire rated requirements, and trying to argue that a non-listed wall has equal rating to a listed wall is not a fight worth having with the building department, especially here in San Francisco.
The reason for trying to frame within the purlin space was to save width as the building is not very wide and we have to create inner courts to satisfy Planning's variance requirements in changing the building to residential use.
The idea behind the spray foam was to 1) seal the existing envelope, and 2) add as much insulating value as possible. I'm not that concerned about replacing the siding. On the walls that are accessible from the outside (rear portion of building) we could simply screw new siding over top.
However, upon further examination, my strategy may not work for one reason. Stacking framed walls between the purlins will turn them into thermal bridges ... unless having the spray foam at the outer layer level conditions them enough for the bridging to be insignificant.
I admit that we may have no other choice but to tilt new walls up against the purlins, and lose 14" of clear width since the purlins are 7" deep horizontally.