12v ERV/HRV ducted options

I plan to construct a plywood box to encase a small counter flow stainless steel HRV core (15″ x 7″ x 8″) with two computer fans moving air through the unit. 12V, PWM fan controller, ~22W total consumption for an off grid setup in a 300 ft2 cabin. I considered buying a metal box, (prohibitively expensive) a polycarbonate/plastic container or PVC sheet goods, etc., but I hope to use as little plastic as possible in the build and keeping PVC out of the intake ducting sure seems like a good idea. If a plywood box is indeed the most cost effective option for encasing the unit, I’ll need to find a way to waterproof the inside of the box, or at least the bottom of the box to drain condensate. Does anyone know a good product/source for long lasting waterproof low or no VOC paint suitable for application in DIY HVAC equipment? Or possibly another solution I’m not thinking of? Thanks in advance for any thoughts/feedback!
GBA Detail Library
A collection of one thousand construction details organized by climate and house part
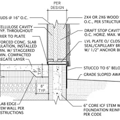
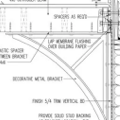
Replies
I've never seen wood hold up for things like this. I'd go for either a metal box, or plastic using (probably) polyethylene or polycarbonate. Polyethylene can be thermally welded, and there are places that can custom fabricate one-off boxes for you (I think US Plastics in Lima, OH can, as one example). Polycarbonate can be solvent welded. Both materials are pretty stable and shouldn't give you any issues with offgassing.
Bill
Thanks Bill, I’ll see if I can source something workable through US Plastics or find something online. If it doesn’t work, maybe I’ll just junk the idea and go with an hrv unit and replace the blower with DC marine or RV units. Cheers!
I would start from an existing unit. The extra cost is not that much plus you get an insulated assembly and duct connections.
An ERV is a better option as it needs no drain plus it doesn't need defrost controls until very cold.
Something like a Panasonic Whispercomfort ERV or one of the budget single room ERVs such as this:
https://www.greenbuildingadvisor.com/question/my-experience-with-a-small-ductless-erv-alternative
You can then take out the built in blowers and replace them with 12V parts. Keep in mind that most ERV cores are pretty restrictive, a standard muffin fan won't push much air through it. A small DC blower is a better option.
Thanks Akos! I don’t need to move much air (30-70 CFM) so I may try some underpowered fans on an oversized unit, but it looks like dc blowers can be had for $15-$30 which may fit the bill. If I strike out on plastic/metal body I may just bite the bullet and buy a 110 AC unit and replace the blowers as noted. I’m this case the incoming air will be 50ish degrees and fairly dry, so I don’t anticipate much condensation anyway. Appreciate the feedback!
Scottie, I more or less did what you're doing (not 12V) but I've learned a lot from the project. I'm still tweaking code on the automation as we're in zone 7A. Using ECM motors, I'm at about 20 watts to do 50 CFM.
You'll need bigger fans, guaranteed, to hit 30 CFM as the core alone will introduce resistance, and more if you have any filtration at all. You'll need some filtration to keep the core clean. The fans don't have to be inside the unit! You can use them externally which simplifies the box. I'm using 0-10V controlled ECM fans, which are controlled by a surprising bit of code from a Hubitat automation controller, sensors on each air flow, and have the unit working very well in up to -35 C so far.
You'll need drainage, and there is much more to it than you would think as pressures inside the HRV will prevent drainage, or pool water in low air pressure areas. Use an ERV core (not cheap, but you can order them for the Renewaire L series (which I would suggest) as it will have excellent efficiency (in the 88% or more at 30 CFM) https://ervdirect.com/shop/replacement-parts/ev-series/ev-premium-l/renewaire-ev200-ev300replacement-core/
No drain issues with an ERV, and you're good to -10 C with no defrost strategy. If you must have an HRV core, then you'll need a defrost strategy that involves a recirc damper, or two fans so you can run exhaust only.
What is your 99% design temp? Climate zone? Heat source?
I posted a fair bit about my system here at the start of the project: https://www.garagejournal.com/forum/threads/super-efficient-hrv-retrofit-with-smoke-filter-for-300.505161/ however what it has become now is quite a bit beyond that thread. The system uses full CO2 feedback control with 6 variable balanced CFM profiles, an asymetric make up air system pressure mode (driven by kitchen exhaust), variable defrost mode speed with temperature monitoring, defrost times variable with outside temp, exhaust hood defrost mode, real time efficiency feedback, inline variable wattage controlled (CFM and temp delta real time adjusted) PTC heaters, blah, blah. I can tell you more if you're interested...and it will save you a lot of time and money.
Hi Dennis, I'm impressed you're able to make a setup like this work in CZ7A! Super helpful to know you've been able to create 50 CFM w/20W of power using ECM motors. I am planning on using 2x Noctua NF-P12 1700 PWM 4-pin pressure optimized computer fans and a PWM fan controller to modulate airflow. The fans are rated at 70 CFM at 0.9A x2 and I'm hoping to create 30 CFM through the unit using ~22W max with the added resistance of an oversized HRV/ERV core and oversized MERV13 filter. I'm totally open to a better/more efficient inline fan solution if you know how to source something more appropriate? I'm probably limited to 4" or 6" ducting, which I'm hoping will work given my limited CFM needs.
Interesting that one of your final thoughts in the project thread is to just fork over $2k for an EC motor ERV! That said, the cabin in question will be in CZ5, outside Leavenworth, WA, 99% design temp is roughly 10F (-12C). The plan is to run 100-150 linear feet of 4" or 6" ducting outside the structure through a hillside to temper incoming air. I'm familiar with all of the advice against doing this at GBA, but am undeterred. :) This should keep the unit from dropping below freezing and reduce the delta T pretty dramatically. The strategy should also lessen the importance of the HRV/ERV's efficiency and more easily allow for passive ventilation strategies in a cold climate when battery storage is running low.
I anticipate the incoming air will be in the 50F range, and the RH in the structure to remain under 50% in most cases. This should limit the condensation in the unit. Famous last words, I'm sure. I hadn't considered the possibility of internal pressures preventing drainage and causing pooling in low pressure areas. Perhaps working in an hourly pause in operation or a uniformly slanted lower portion of the exhaust channel will help here. The property will be used intermittently as well, which should help unless/until the usage changes in the future.
I'm looking forward to doing a more detailed review of your project. Thanks so much for the VERY helpful feedback!
4" ducting is fine for 30 CFM on short runs, but not for a long run underground. You'd be looking at 6" or 8" to be safe on a 100-150 ft run. Moisture from an HRV core will be more than you think unless it is drained with at least 1/2" tubing...it will flood and make a mess. You also need to have the drains in the correct place or pressure differences around the core will also cause issues Ask me how I know this after spending nearly a month troubleshooting drain and freeze up issues :-)
Starting from scratch, I'd 1000% just start with that core from the Renewaire EV Premium L. It's not small though. It's a square profile with 10 1/2″ faces and 21 3/4" depth. You can find that ERV in the HVI database: https://www.hvi.org/hvi-certified-products-directory/section-iii-hrv-erv-directory-listing/
Given your design temp, that ERV core would not require any defrost strategy at all. With an HRV core, you need to program defrost cycles as soon as temps drop below freezing. No way around this, unless you can guarantee fresh air intake above freezing at all times.
A large exchange core and lower flow results in much higher efficiency. That core I linked to is found in the Renewaire EV Premium L which is tested at 88% efficiency at 59 CFM. At 30 CFM it's efficiency will likely be higher than 88%. This means that at 30CFM, and 10F outside, assuming 88% efficiency, the delivery temp "should" be about 63 F...worst case. With a large core, and low CFM pressure drop will be low, so you may just get 30 CFM with that fan. You can play with the efficiency numbers here: https://www.engineeringtoolbox.com/heat-recovery-efficiency-d_201.html
Is the risk, and labour in an earth tube system worth it? That said, you sound like a guy willing to play around a bit and are not afraid of failure...so it would an interesting experiment :-) I find that once I run the numbers (CFM, delta temps, heat energy etc) a lot of these ideas don't look as attractive. One of my pool solar automation sensors is intentionally positioned for winter at ground level in our back yard, under undisturbed snow. At -20F that sensor has stayed within 1 degree of 32F. Something to think about as the snow insulation layer and geothermal heating might suggest a shallow tube bed with 2-4" insulation over top might actually work well, providing it has good snow cover. You really need to manage moisture in that buried air tube which will make it a challenge to get right.
Computer fans are really not great with static pressure so I'd grab one, throw it into 6 ft long 4" duct and take some flow measurements with an inexpensive vane anemometer as you add resistance. I ended up replacing the 4" ECM fan with a 6" version on the fresh air side of my setup (which has higher resistance than stale side) so a 352 CFM (rated at pretty much zero pressure drop I'm sure) fan is topping out at a delivered 90 CFM. This is through an HRV core rated for over 200 CFM, and a 14x14x4 MERV 13 filter. Remember that you'll want something like MERV8 filters on the exhaust side of the core too to keep it clean.
I mentioned the ERV for $2K in my garage thread as I figure not many folks would want to go down the same path as I did. That said, I've managed to create a system that is likely more efficient than 99% of commercial offerings as I'm taking advantage of the temperature sensor inputs to optimise power use and delivery based on Co2 levels in the house. It keeps things remarkably close to 650-750 ppm co2, regardless of occupation, shutting down completely at 550 CFM. A windy day with zero occupancy will bring levels below 550 CFM and the system will shut down. The exception is when we have company over, where 90 CFM is not enough. That said, recovery happens in 1-2 hours so no large concerns there. A lot of energy is used up in defrost cycles (inside heat used to warm the core) but I've even optimised the power side of that by ramping the fans based on internal temps, and adjusting defrost times dynamically based on actual outside ambient.
The original goal was also to manage some makeup air function with the kitchen exhaust, and this is working great, even at very cold temps. It's only about 50 CFM makeup, but it does make a difference as our home is pretty tight. Power use by the induction cooktop triggers the kitchen exhaust ECM fan, which in turn toggles the HRV system to the asymetric flow profile (50 CFM more supply than exhaust). The end result based on the air quality monitoring is pretty much zero increase in PM2.5 during cooking...and no one needs to pay attention to switches etc.
I've learned a lot from this project.
Your CO2 modulation, fresh air delivery to bedrooms at night and automated HRV makeup air for the kitchen exhaust is exactly what I need at our primary home, so I may be back to ask you more questions about the details of your controls in the future! For the off grid setup, I'll plan to go with a 100' 6" buried duct. Luckily the property is 20 acres and on a hillside, so drainage of buried ducts will be MUCH simpler than in most situations. I hadn't thought of the shallow trench + 2" insulation under snow, (October-March-ish in our neck of the woods) which I may consider given how much less work it is. Then again my neighbor has an excavator, so he may not care 5' vs. 2', etc. I'll definitely design a box around a large core, but that leads me to my initial issue of what material to use for cost/longevity. Because the incoming air will be tempered, I don't anticipate having the same level of condensation issues that you face, but I'll definitely try to overdesign for drainage, (larger diameter drain tube, base of unit angled toward drain, etc.). Since I have 4" inline fans and ducting I'll test it out and see what kind of airflow I get, but will plan upfront for the potential to replace with 6" units as needed. Thanks for all the incredibly helpful feedback!
Scottie, glad to help. Most HRV/ERV housings are just a metal case with thermoplastic top/bottom with 1/2" to 3/4" foam insulation. In your case, I would not overthink it. A wood outer box (use treated plywood) with an inner lining of 1" EPS would be fine. You could line the inside with coroplast (laminate to the foam sheet first) and use caulk or canned foam to seal the seams. Line the door with closed cell foam (yoga mat?) to seal up against your internal bits. You could laminate up the ply/foam/coroplast first on a 4x8 sheet and then mitre your cuts at 45 degrees for the box.
If zip sheathing is available in your area in R-5 to R-10, you might consider using that for the box and use the coroplast to line it.
If you go ERV core, you don't need to worry about drainage. If using the HRV core, you'll need to figure out a tapered base and drain. Remember on a hot, humid day you'll have condensation in an HRV core that will need to be drained.
Dennis, I'm totally going to do the zip/coroplast or ply/foam/coroplast 4x8 sheets and then pull out the table saw to cut out box parts. I think this is just the ticket. Next steps are testing cores/fans/ducts/MERV13 filter boxes to confirm duct fitting and fan size requirements. Thanks for talking this through and pointing me in the right direction!
Scottie, did you have a source for the cross flow metal core?
The core in my "test" setup will vary between about 80% and 60% efficiency based on flow, and I can get it to 90% by skewing air flow asymmetrically. I also tested the core from a Panasonic FV-04VE1 (small ERV core) and it was pretty dismal in the 50% range. Size is your friend if you want efficiency...and clearly the Renewaire (and 3-4 other manufacturers selling the same unit) are exploiting this. The Zhender ERV cores are even larger.
For MERV13, if doing a DIY inline box, I'd grab a Filtrete 1900 20x20x1 and start there. I'm using the inline box from Hvacquick CFB-6 which shows less than .05" w.g. drop at 90 CFM or so with 14x14x2 MERV13 in place.
With those 12V fans, you'll find that as you add in the core, filtration, and ducting, it will be a challenge to get 30 CFM delivered to the room. I'd also insulated your intake and exhaust ducting well beyond R6. Do R12 at minimum.
Also, hot tip. The Fibaro Smart Implant allows you to run up to 6 DS18B20 remote temp probes as a "plug n play" monitoring solution for under $100 all in..including probes.
Hi Dennis, the metal core I have on hand is a counterflow unit produced in Europe. I believe it's a replacement core for a Recutech model HRV. It's undersized in comparison to the large ERV core from Renewaire, so I may have to purchase the larger unit after airflow testing in the coming weeks. If it doesn't work with the existing core+filter, then I'll step up the fans and ducts, then purchase a larger ERV core if needed. I was planning on using a 14x14x4 MERV 13, with the understanding that wider filters reduce the airflow penalty, but a 20x20x1 may make sense. I'm sure there is some database available to compare the different sizes and expected airflow penalties with standard MERV 8, MERV 13, etc. filters in different configurations. I also considered buying a 20x12x1 inline filter box off Amazon @~$100 which could work here. The Fibaro Smart Implant could be a perfect solution for this part of my project and other temp sensing I will probably want to continuously collect, so thanks for the heads up!
24h/day power draws in off grid are killers. Say you can get the ERV down to 40W, that is still 1kWh/day energy use. Producing and storing that much energy is expensive, add in there a day or two of low solar production and you need a very large battery.
The best ventillation option for off grid is cracking a window and putting another log on the fire.
There was a company for a while making a passive stack pressure driven HRV on the other side of the pond, might provide some ideas:
https://web.archive.org/web/20160305071138/http://www.ventive.co.uk/products/ventive-s
The power requirements are the real killer here for my situation. The intent is to reduce the power consumption to 20W or less, (hopefully) reducing daily energy use to 500Wh max and then implementing passive strategies if needed. I've come across ventive a number of times but they appear to have moved into automated/electronic solutions combined with passive ventilation. My current plan is to include a small solar chimney on the exhaust capped with a syphon ventilator. This should theoretically create passive pressure driven exhaust when the sun shines or the wind blows, modulated with a ball valve. I figure intermittent is better than nothing. This may also reduce power usage if it allows for modulating the exhaust fan when power is available. Thanks for the additional feedback!
That's why I asked about heat source. Sorting a decent exchange strategy may make zero sense vs just opening a window for 300 sq/ft.
Dennis and Akos are certainly right. But opening a window = zero percent fun. Building a perfectly balanced system to tinker with for decades = 100% fun! Perhaps until it isn't, anyway... :)
Scott, I'm still tweaking automation on my setup. The latest "additions" were implementing changes to run a more aggressive Co2 map at night which keeps the bedroom levels lower. I also cleaned up behaviour coming off a defrost cycle so that the HRV selects the correct CFM profile based both on Co2 levels and the kitchen exhaust status. The kitchen exhaust always has priority over C02 levels to balance air flow in the house. It's a working lab experiment that serves a pretty important function too.
The end solution for the drain vs air pressure issues was indeed inserting a 90 second pause (fans off) after each defrost cycle, or twice an hour when above freezing.
The next step when things warm up is to figure out a pretty aggressive smoke/VOC pre-filter setup for summer use. Wild fire, back yard smoke and resident skunks are seasonal irritants here.
Btw, you should check out the LUNOS setup/concept which may actually work better with low power 12 fans. If you can source cylindrical ceramic heat exchangers, you'd just need the fans and some programming.
I have one of these discontinued Bionaire mini HRV systems that I'm not using if you are interested in using that as a starting point to replace the 120 V blowers with your own system.
https://www.amazon.com/Bionaire-BAP336-U-EverFresh-Exchange-System/dp/B000H14B7U/
Hi Charlie, I'm not familiar with the Bionaire systems, but if it's 12V and the blowers are efficient and can be used in place of inline ducted fans, I'd love to see the details. I'm in Seattle, FYI. Thanks!
I think I explained what this is backwards. It's an HRV unit with 120 V blowers in it. It has a decent plastic HRV core, and two blowers on a single shaft, driven by an inefficient 120 V AC motor. I was imagining you using the case and the core, and replacing the 120 V blower with 12 V blowers that you sourced elsewhere. I'm attaching a photo of the inside with arrows for airflow: double line is the exhaust that goes straight through the core; single is the intake.
Hi Charlie, thanks for the clarification and helpful airflow drawing! I could find lots of uses for this machine, so if you're not using it I'd be delighted to take it off your hands. I'm in Seattle. Thanks!
You could email me at [email protected]; I'm a bit far from Seattle but it might be worth shipping.