low slope roof insulation

Hello,
I am thinking of taking over a job that is underway and wanted some advice on this problematic roof situation. Maine, zone 6.
It is a two story addition tacked on to the back of an existing house. Approximately 400 square feet total. Its framed out, so there is no wiggle room in the design. The single-pitch shed roof is 2.5/12 and dies into a vertical wall at the back of the house. The rafters are 2×8 on 1 foot centers. The CEO approved the design and now I have to figure out how to insulate it.
A vented roof is out of the question because there is no way to vent the high side that dies into the wall. Its also too flat for that. There can be no outsulation since the roof sheathing is at the limit that can be safely flashed- there are existing windows just above the roof sheathing. With 7 1/4 inches of rafter space and very limited headroom (already at code) it seems that cut and cobble is the only option, other than spray foam (which I am trying to avoid due to toxicity, etc. and the clients living in the home).
I have read the GBA articles warning about cut and cobble. Code is R-49 so 7 inches of polyiso would meet code. If I did a very careful job of this, using European tape and perhaps canned spray foam, I feel like it could work.
1. Would laying membrain interior of the polyiso, and taping it off as if to air seal it, be a wise approach in this situation? If the problem with cut and cobble is vapor intrusion into the assembly as the framing dries and twists, would adding a membrain allow this same vapor to dry to the inside?
Thanks, Stephen
GBA Detail Library
A collection of one thousand construction details organized by climate and house part
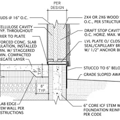
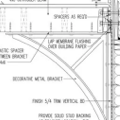
Replies
stephen r,
I would think very carefully about walking away. If the head room is already at code with drywall in place then you don't have any option for a final layer of polyiso to cap the shallow roof rafters. If you filled the rafter bays with closed foam you are just barely above R-38 between and only R-10 through the rafters. The 12 " spacing will ding your whole roof value. A one inch polyiso sheet to break the rafter thermal leak would be huge to the overall numbers. This assumes an unvented roof layup.
Aside from the venting difficulties, trying to incorporate a vented air space above a cobble job would be very scary in my opinion. I am a bit surprised that the job got this far without considering the roof insulation codes.
The idea of using a membrane of any type to protect an unvented cobble job is equally scary to me. The tail bays of the rafters would need to be sealed flawlessly to prevent air intrusion as well as the header at the current house side. More leak potential if there are any overhead fixtures or wiring to seal up.
Probably out of the question, but could the windows above the new roof be replaced with shorter ones to allow for above roof insulation? Sounds like the original house is older so maybe a two-fer. Better windows and a better result in the room below. The labor of cutting 10.5" strips of foam and stuffing them into place won't be small.
Onslow,
Thanks for the insight. It is one of those jobs that one might want to pass on but it does click some boxes for me, (clients are cool, good location, good winter work and lots of fancy woodworking) so I am kind of considering it. Also, its small enough, and I work mostly solo, so keeping it simple would be the best approach. First step is to meet the clients and speak with the code officer. Thanks for the reminder about air sealing the eaves, etc..
Cheers!
Cut and cobble is a PIA and is more likely to result in gaps and air leaks than a well-done spray foam job, but with attention to detail it can still work. This sounds like a poorly conceived design but if you don't have options for changing it, I think your proposed approach would work. If gaps occur between foam and framing, a variable perm membrane on the interior is good insurance.
There are some work-arounds in the code. R402.2.2 might be worth considering: https://codes.iccsafe.org/content/IRC2015/chapter-11-re-energy-efficiency#IRC2015_Pt04_Ch11_SecN1102.2. There are also some ways to reduce ceiling height: https://codes.iccsafe.org/content/IRC2015/chapter-3-building-planning#IRC2015_Pt03_Ch03_SecR305.1.
Another code-related item is that if you can provide 1/150 of the floor area in soffit vents, you don't need a ridge vent: https://codes.iccsafe.org/content/IRC2015/chapter-8-roof-ceiling-construction#IRC2015_Pt03_Ch08_SecR806.1. With a ridge vent you can reduce the area of the soffit vents.
Michael,
Thanks for those code references. This is a classic lumber yard designed addition. The clients have nickels and its right in downtown Newcastle so I can’t really understand why they didn’t hire someone to design it correctly. Nevertheless, here we are.
In reference to N1102.2.2 (R402.2.2,) Ceilings without attic spaces…when it states, referring to the r-30 reduction “ …limited to 500 square feet or 20% of the total insulated ceiling area, which ever is less.”…
is this 20% of the total ceiling area referring to the entire house, or simply 20% of the new addition? Thanks
Also, please see recent post “Michael: Need Help with Maine Codes” just posted, for my house build.
Thank you!