Low Pitch Unvented Cathedral Metal Roof Assembly and Avoiding Mold

Hi GBA folks. Nice website, very helpful resource. I would be very grateful if somebody with some knowledge finds this and has a moment to respond.
We are building a mobile home with slightly more than typical height limitation due to higher floor to make it removable from the trailer, which has other duties. 2×4 walls, 2×6 rafters, Zone 5 with humid summers, though it could be moved. Design priorities in order:
#1 Minimize chance of mold growth.
#2 Limit cost.
#3 Limit height (travel & possible future owners) while still maximizing loft area over 3′ (code & comfort).
#4 Compatibility with different climates.
Question #1: Should we do a 2″ pitch gable roof with a ridge (not centered) or a 1.5″ pitch shed style? The ridge approach improves the pitch and the height of the loft, as walls are framed and mostly sheathed already, but ended up a bit higher than expected. Would have to cut down walls to increase pitch on a shed roof above 1.5. If we go with the ridge, is the ridge cap is going to fail at such a low pitch?
Here is another discussion about an unvented roof on a tiny home with limited height but a better pitch: Vented or Unvented Cathedral Roof for Tiny House? – GreenBuildingAdvisor. Steve, the author of this thread, was in Zone 5 British Columbia, where local authorities called for “effective RSI 4.67 (R-26.5) which is nominal R28.” Code here wants R49, but it looks like that can be circumvented by increasing total envelope UA by adding (more) exterior board to the walls, see screenshot of 2015 EICC R402.1.5 Total UA alternative.
I’ve attached Steve’s details (please note ours has a 2 pitch and no purlins planned), which include Metal Roofing, 3/8″ Plywood, 1.5″ EPS, 5.5″ EPS, sheetrock. Martin didn’t love the plywood foam sandwich. The exterior insulation is less than 40%, but per EICC R806.5.1.1&3 (attached), no exterior insulation is required where air impermeable insulation is installed directly below the sheathing.
Questions:
2. Any ways Steve’s assembly could be improved without increasing height?
3. Why exactly doesn’t Martin like the EPS sandwich?
4. Why not install more insulation between sheetrock and rafters and eliminate insulation above deck? Easier to build, save 3/8″, $, weight, and roof deck no longer insulated at all, but in Steve’s plywood sandwich, you have another sheet of uninsulated (from the cold side) plywood anyway and are short of the 40%, right?
5. How about just remove the extra 1.5″ insulation altogether and make up for it on the walls?
5. Tape, or ideas to prevent air passage between rigid foam and rafter, besides tight fit? Seems like a potential point of failure in the air impermeable insulation requirement. I don’t trust canned foam on a mobile home, especially this one.
6. Roofing directly on ice and water, no mesh, furring? no venting.
Open to suggestions. The height restrictions are not that big of a deal in the short term — it’s wide so we’ll need an escort and a wide load permit to move anyway, but I think dealing with the regulations (route survey over 13′ 8″, two escorts over 14′, who knows what in other states) would reduce utility for future owners.
Big thank you to anybody who takes the time to read & respond!
GB1
GBA Detail Library
A collection of one thousand construction details organized by climate and house part
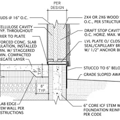
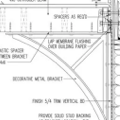
Replies
Greenbuild1,
Up here in Canada Tiny Homes on wheels like Steve's are simply site built RVs. They don't have to meet building codes (and couldn't be made to do so), meaning the solutions can be whatever will work, not what is required. It may be similar where you are. For a Tiny House there is no reason to adhere to code mandated levels of insulation, just the amounts and ratios of permeable and impermeable insulation, which dictate whether it will be safe from moisture concerns or not.
1. Go with whatever style roof works best for you. Both gable and shed roofs have caps at the peak. Both are more susceptible to leaking due to the low pitch, but it's much easier on an un-vented roof as you can completely seal it.
2. I would suggest not using using foam board in the cavities and instead fill them with high density mineral wool batts. Make sure the outer layer of foam is thick enough to prevent condensation on the sheathing, strap with 1"x material above the foam. Assembly #3 in this link: https://www.greenbuildingadvisor.com/article/five-cathedral-ceilings-that-work
3. If the sheathing ever does take on moisture there is no where for it to dry to. Typically assemblies with no drying path are riskier.
4. To reduce thermal bridging, and because cut & cobble (placing rigid insulation in your rafter cavities) can have problems with interior moisture making way to the sheathing and condensing there. The exterior insulation keeps that lower level of sheathing safer.
5. See $#4 above.
5b. Tape, or a flexible caulk like Contega HF
6. I would do as you suggest and eliminate the upper layer of sheathing (see #2 above).
Hi Malcolm! Wow, I can't believe you guys respond to everything, even on Sunday. Thank you for the time and attention.
Building Department may become involved if the unit becomes an ADU. In any case, preventing moisture issues is our chief priority.
I just enrolled, and that article is still paywalled for me currently. I look forward to reviewing that one and others. I do have access to the article below from BSC and EICC codes.
https://buildingscience.com/documents/building-science-insights-newsletters/bsi-100-hybrid-assemblies#t01
The attached table from the BSC article (and IECC) stipulates 40% insulation above the sheathing in order to keep sheathing above 45 degrees on average in the winter for zone 5, as a mechanism to "keep the [wintertime] moisture content of the sheathing below 20 percent by weight" if air permeable (fluffy) insulation is used in the cavity. In Hybrid Assemblies, he mentions 35% interior insulation for these numbers, but in RR-0404: Roof Design, says "an additional criteria is also necessary - that of keeping interior relative humidities below 45 percent," more easily attainable.
Short of that 40% ratio, which we can't achieve without a too-tall stack of rigid board on top of the deck (5"), or stripping a lot of insulation from the cavity, the insulation directly beneath the sheathing must be air impermeable, and further (this is Joe L quoting the code): "“in Climate Zones 5, 6, 7 and 8 any air-impermeable insulation shall be a Class II vapor retarder”…. Yup, only closed cell foam meets this requirement".
1. Thank you
2a. First, do the sealed caps present a problem for the air gap created by the furring in the suggested design? With a shed roof design, I thought we could vent the air gap downwards on each side, to the inside of the fascia with some low to high air movement despite the drop below the fascia on the high side.
2b. Given that we won't have 40% of the insulation above the sheathing, isn't air impermeable & class II vapor retarding insulation needed to prevent the cold sheathing from sweating? I don't want to use spray foam, but would a rigid foam product with the right perm rating, taped to the rafters to prevent air seepage, serve this purpose?
2c. Do you expect water vapor would reach the sheathing through failure of the ceiling air seal or some other route? Is some rigid above better than none? The BSC article and the code do not mention an intermediate scenario between the 40% top side insulation and air-impermeable insulation beneath cold sheathing with no top side insulation.
5 & 6. some top side foam and strapping. see 2a
5b thank you
Many thanks!
Greenbuild,
2a. No that isn't really a vent space, it's a small gap that will see an incidental amount of moisture from condensation on the cold roofing. That moisture can vent vertically though the raised profiles on your metal panels.
2b. Sorry I should have been clearer. I was suggesting you use sufficiently thick exterior foam to meet the safe ratio.
2c and a general comment: It's the failure of the perimeter sealing which it the main concern. Cut & cobble isn't something I would specify, or use on a house, but if done diligently on a small structure, with the first layer adhered to the sheathing, and subsequent ones well sealed, I'm pretty confident you will be fine. So maybe Steve's roof minus the upper sheathing is the way to go?
Here is assembly #3 from the fire-walled link:
Thanks again. I am aware the assembly you shared is better, but if we put R23 in the cavity, we need 4" of rigid on top, or with R19 fiberglass, 3.5" rigid on top, plus strapping. Air impermeable under the sheathing would save us a lot of height.