Insulating a Post-and-Frame Building

Hello community! I’m excited to get your ideas and opinions on my new post frame building design. Shout out to Martin Holladay for his article “Insulating a Pole Barn” in which he points to the house built by Ben Freed as an example of a well insulated post framed building. In this Q&A I’d like to incrementally advance the discussion on this site with regards to building a good post framed envelope to be heated in a cold climate. This post is about new construction so it won’t try to directly answer the questions of people trying to turn old pole barns into something else.
The plan I’m developing is for a 40’x60’x24’H carriage home (home above garage space) to be built on rural land I’m purchasing near my current home. I’m the owner/builder of my current home as well as the new one that I’m planning. The area is climate zone 6 in the Canadian rocky mountains. We don’t having zoning or permitting in my area so I am able to build without restrictions but I intend to honour the building codes unless I have a good reason to vary from their wisdom. My goal with this building is to erect the outer shell efficiently and get it insulated to use as a warehouse and workshop during the rest of the land development and remainder of the home build. In the coming years I plan to develop both a small apartment inside the building as well as a full upper mezzanine home. Cost efficiency is a primary objective for this project along with durability.
Building dimensions are 40’x60’x24’H. The height allows for a 13’H garage below the upper home. A thickened edge slab on grade, frost protected shallow foundation forms the base. Attic-style roof trusses above for utility access; unvented attic. Walls built with 6″x8″ laminated posts on 4′ centres, joined with 2×6 girts. No wall sheathing is necessary for the sake of shear strength as other details provide for that. Siding and roofing are ribbed or standing seam metal. I have been considering how best to insulate this building in a way that is time efficient, cost efficient and maximally durable. I want good air control but I don’t want to bird-dog every member of a large crew taping seams during the initial erection of the building. To this end I have developed an idea to insulate this whole envelope with 5″ closed cell spray foam directly applied to the interior side of the factory-painted metal siding and roofing, as soon as the building is closed in.
I like this method for the following advantages:
*exceptional air control
*workflow efficiencies
*no detailing of exterior or interior membranes
*eliminating sheathing and membrane $$ offsets spray foam $$$
*added strength of a fully “glued” structure
*industry bodies recognise this method of applying foam insulation directly to painted metal (see SPFA-134)
I see the following weaknesses, which I am comfortable accepting:
*cost of spray foam is higher than blanket insulation and blown-in cellulose
*re-roofing requires strapping over top of old roofing to add second roof
*requires thoughtful details around siding penetrations
I have the following concerns:
*spray foam off-gassing HFO and other gasses into building
*how to allow drying of wood around windows etc
*differential expansion of metal and wood components
*cracking and gapping of foam over time
*method is not yet widely used in residential construction
*what may I have missed?
So my thoughtful friends, what do you think about these methods? I appreciate that this idea is a significant break from the methods popular on this forum which tend to focus on great sheathing and membrane details. Can anyone offer advice or insight from experience with a similar build to mine, perhaps in the commercial space?
Dan
GBA Detail Library
A collection of one thousand construction details organized by climate and house part
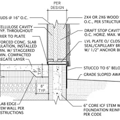
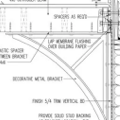
Replies
If you search on youtube, "marshall remodel" did a post frame house with spray foam insulation. Initially, they had moisture problems, because the foam wasn't thick enough in some areas, and screws had been used as thickness depth guides. They added more foam and it seems to have fixed their problems.
I am planning a 40x40 post frame home in MN with good energy performance. Below is a summary of the general details:
* Slab insulated with EPS, following frost protected shallow foundation detail.
* Vapor barrier under slab, tied into wall vapor barrier.
* Double wall, exterior is 2x8" bookshelf girts, interior is 2x4" standard vertical studs.
* Butyl rubber "joist tape" on outside of wall girts, to seal around exterior fasteners.
* Commercial tyvek with taped seams under exterior steel.
* Smart membrane vapor barrier inside of double wall.
* Rockwool insulation in walls.
* Blown in fiberglass in unvented attic, over vapor barrier and steel ceiling.
* "Condenstop" coating on underside of roof steel.
Just as with other construction techniques, it takes planning to have good and continuous air and vapor sealing. Unless you do it yourself, plan on bird-dogging whomever is doing the air sealing details.
Older video showing some of the design details of my project:
https://www.youtube.com/watch?v=IQvE9pc9tbE
Wow Erik, this build looks very well thought out. I like your detailed drawings and the way you explain your reasoning for many of your decisions. I expect to refer to your video again as I continue to develop my plan. Thank you for sharing.
One thing I noticed that might save you money is using a smaller electrical service. I believe 200A will suffice in your application unless you plan to add several more cabins or something else like that. The load calculation that you need is based on what's called a "diversity factor" which is meant to account for the fact that it's very unlikely that you ever run 100% of your electric loads at the exact same time. I don't want to derail the discussion on this thread too far so I'll leave it at that, and please message me directly if you'd like to discuss this further with me.
I'm still undecided about whether to use the "Perma-Column" direct buried post foundation system or instead anchor my posts on a monolithic slab, but I'm leaning toward the latter. Doing a more detailed cost analysis may convince me to go your way, but I think it's worth teaching people that post frame buildings don't necessarily have direct buried post bottoms; we can use any kind of foundation that any other building might use, but with the added option of burying the post ends. If you did detailed pricing on a thickened edge slab foundation in your area I'm interested to know how the cost compares to the Perma-Column option with floating slab. Perhaps my biggest concern with the Perma-Column foundation is air sealing around the bottom of the wall. With a thickened edge slab I can build my walls on top of a bottom plate sealed to the slab in all the usual ways.
I'm curious if you considered using sprayfoam directly applied to the interior side of metal as a method of air sealing and insulating, as I am suggesting I might do. If done as I'm suggesting, you would eliminate the expensive rockwool, house wrap, and vapour barrier, and potentially gain a heated attic to use for utility runs. A huge advantage I see combining this method of construction and insulation is elimination of thermal bridges. By spraying between the metal and posts, and covering the girts in foam, nearly all thermal bridges are eliminated. The building becomes a monolith of wood, metal and foam with exceptional air tightness and stiffness. Key to actually achieving air tightness, however, is the floor slab details and the join between slab and wall. Most post frame buildings that residential builders are encountering in a ranch/acreage setting have been built with buried post ends and a dirt floor, and that is a difficult situation to air seal.
See the following video detailing how to correctly apply spray foam in a post frame building: https://www.youtube.com/watch?v=cFwQ4CQH4lw
and this one addressing the issues encountered in the "Marshall Remodel":
https://www.youtube.com/watch?v=mVEfdVhaTDY
Spray Jones is based in Saskatchewan, Canada - not so far from you Erik and in a similar climate - and he has a whole lot of good educational videos about its effective use.
Hi Erik, Drew below has asked about the software used to make your design drawings.
Regarding the posts:
Am now considering "sturdi wall" brackets wet-set in insulated concrete pier forms. The logistics are easier than the perma-columns.
For air sealing, the vertical insulation around the slab will extend up into the wall. The outside WRB will connect to the insulation protection (pvc board) and the inside under-slab vapor barrier will connect to the wall vapor barrier.
Regarding electric service:
Will probably move to 200A panel. Am moving to cold climate mini splits and making other changes that cut down on loads. Am aware that the analysis is conservative due to not including "diversity factor".
Regarding suitability of spray foam:
Am planning on DIYing most things on my build. Spray foam isn't very DIY friendly. Also, it will make it nearly impossible to re-work areas later or replace panels. This is the main reason I'm not planning on using it. Since it is also used as the air and vapor barrier, there is very little margin for error in the application. With separate WRB, insulation and vapor barrier, each one can be applied, inspected and re-worked (if needed) at a leisurely pace.
Post spacing:
Noticed that you mentioned 4' post spacing. This is probably not necessary. Depending on wind, snow, etc loads a much larger spacing such as 10-12' might cut down on material use and save money, while still meeting the loading criteria. There are many companies that will engineer the building shell around these larger spacings.
Misc:
Have been doing a lot of thermal modelling in BEopt, and the impact of air tightness on performance is huge. Same for SHGC factor on windows. Would recommend modelling your structure in this tool:
https://www.nrel.gov/buildings/beopt.html
Very good Eric, thank you very much for your input.
Air tightness has a huge impact on the thermal performance of the building not only because cold air blowing into the interior space is cold, but I believe typically more so because air convecting around among the insulation can decimate the performance of insulation compared to its nominal R-value. A good thing about spray foam is that it's one trade and one application to get right instead of several. While this does make it very critical to get SPUF right, with batt insulation there are several things which must be done perfectly to achieve the nominal R-value in practice. Personally I have rarely seen even one of these steps done correctly (housewrap, batts, vapour barrier) never mind each of them done perfectly in tandem. Hence some spray foam applicators claim that 2" SPUF thermally outperforms R24 batt insulation. Given the many compounding errors typical in a batt insulation installation this may be true more often than we'd like to think. In your case if you're able to detail each of these layers yourself you should be able to achieve outstanding thermal performance with your design. Just be aware that the air seal at the bottom of your walls, if it's compromised over time due to differential shifting of building components, could reduce the thermal performance somewhat. That said, your control layer details at the wall bottom sound well thought out. I will draw from them if I decide to build my foundation similar to yours.
Unfortunately I'm not currently set up to run Windows executables but I'd like to check out the modelling tool you recommended.
I'm curious to know more about your interest in "cold weather mini-splits". I hadn't heard good things last time I looked into them but it wasn't recently.
Dan
There's a lot of good information on the cold weather mini splits on this website. This is the article that got me interested:
https://www.greenbuildingadvisor.com/article/do-heat-pumps-work-in-minnesota
These two features are what make the cold-climate operation possible:
* Enhanced Vapor Injection (Hyper Heat™ or similar). This allows for sub-zero operation.
* Pan heater. This stops frozen condensation from damaging the exterior coils.
Mitsubishi, Fujitsu and LG all have cold climate mini splits with these features. The Mitsubishi units have full rated performance to -5F, and 66% performance at -13F.
Using the BEopt tool, found that using south facing windows with high solar gain (Wasco) cut down on heating inputs substantially over low SHGC windows.
I would guess that the most cost effective way to build a building is by standard practice: conventional framing. People often think they can reinvent the wheel and do it cheaper than the next guy, buy this rarely is the result.
Pole buildings are great cheap buildings for their intended purpose- unconditioned storage. For a conditioned space, and particularly residential space, framed walls with batt insulation is the cheapest method.
Have you priced out what the ccsf costs?
Hi Bob, I agree with your guess that the cheapest way to build an insulated building is probably using stud framing and glass batts, with blown-in cellulose attic.
Have you seen wall cracking in stud framed houses? I have seen a lot of it in Canada, both in new and old homes. Commercial buildings rarely make use of a stud wall structure because conventional stud framing leaves a lot to be desired from a structural standpoint, especially in tall buildings, and mine is 24' tall. Thermally we see stud walls offer thermal bridges in ways that technologies like ICF, SIP, and post framing do not. Stud framing has the advantage that it's cheap and common, and I enjoy stacking stud walls as much as the next guy. For my next build I'm looking to do something better than a stud frame without breaking the bank.
Dan,
"We don’t having zoning or permitting in my area so I am able to build without restrictions but I intend to honour the building codes unless I have a good reason to vary from their wisdom"
The reasons to do that may be a bit more compelling than just preference. The BC Building Code covers the entire province whether there is permitting and enforcement or not - and I suspect the same is true of Alberta's. In the absence of inspections, there is still a requirement that the owner comply with all codes.
You're correct Malcom.
Dan,
I brought that up because to meet our building codes that method has to overcome at least two hurdles.
The first is the lack of a WRB between the cladding and insulation.
The second is structural. Part 9 only recognizes conventional framing with studs spaced no more than 24" oc. It also does not allow thickened slabs. Both of these move the project to Part 4, which requires an engineer.
Nothing insurmountable, just something to be aware of.
Thanks for the specifics Malcom. I have engaged two structural engineers on this project so far, one with a large post frame building company and one independent. With our combined expertise in design I'm not concerned about the structure of the building.
The matter of the WRB is actually at the heart of my questions on this forum. SPUF is used as a WRB in well established cases such as roofing. In the case I'm illustrating here it's performing as an integrated WRB, air barrier, insulation, vapour barrier, and adhesive which also doubles (at minimum) the shear strength of the wall and roof. A lot of roles for one material. Anecdotally, installers have been doing what I'm illustrating here for at least 20 years with good results. Installers say experience shows that adding a membrane between the metal and foam causes condensation problems that don't exist when directly applied. It also eliminates the structural bond the foam provides. Whether or not the SPUF qualifies as a WRB under code is another matter which perhaps comes down to the manufacturer of a specific foam having it tested, vetted and added to a list.
Malcom, replying to your question on my other thread here: https://www.greenbuildingadvisor.com/question/advanced-framing-method-with-integral-air-barrier-and-siding?cid=223986&discussion=response#comment-223986
You asked: What is the advantage over conventional framing that y0u see this method offers? For my project it is simply about reducing the cost of exterior sheathing on the walls and roof.
Here's my answer: Conventional stacked studwall framing of multi-storey buildings is inefficient and structurally inferior to post framing in the following ways:
-Stacking walls and floors and walls and floors creates pivot points where the floors meet the walls. These areas often leak copious amounts of air even when new and frequently are the sites where buildings movement leads to cracking finish material and torn air barriers. This can be mitigated by thoughtful carpenters doing exceptional work but fundamentally this is a weakness of the framing design that can easily become a large problem due to small mistakes during construction. I've built houses this way; it's easy, cheap and fast. My own buildings haven't failed (yet) but fundamentally I dislike the framing method for these reasons.
-Post and beam framing using continuous laminated posts distributes stresses more evenly along the posts. Where a conventional stud frame building has several walls stacked over one another (levers and pivots), a tall or multi-storey post frame behaves more like a continuous wall, because it is a continuous wall.
-For the above reasons, the likelihood of building movement concentrating stresses to the point of envelope failure at a floor is reduced.
-SPUF in a wall bonds everything it touches. This creates a structural monolith of the framing members near one another. Nails are no longer a weak link where your boards meet, or where sheeting joins your boards. Testing shows that SPUF in a wall makes it far stronger than without it.
-26ga ribbed metal siding is a strong structural diaphragm. The weak link when using it that way is the fasteners that attach it to the frame, and its potential to deform by bending slightly. SPUF directly applied to the painted metal bonds the metal fast to the frame, and slightly reduces its ability to bend.
-If one can take full advantage of the structural diaphragm potential of ribbed metal siding and roofing and make use of it in the wall, wooden sheeting can be rendered redundant in some applications. This is a major advantage if sheet lumber recently increased in price 4x-8x in your region.
-Stud frames have 10x the thermal bridging of post frames. In a stud frame, continuous wood runs from inside to outside making up between 16-35% of the wall area in a stud frame building (per Joe Lstiburek) and limit the performance of any insulation that you install in the walls. The best way to make a stud wall perform well in a cold climate is to install a continuous blanket of insulation panels over top of the sheeting to mitigate the thermal bleed through the studs. It works, I've done it, it's expensive and time consuming, it's lipstick on a pig.
-In a post frame wall, the thermal break is integral to the perpendicular framing. Continuous wood from inside to outside is only 1.5%-3.5% the framed area. SPUF in the wall cavity of a post frame covers all framing members on 3 sides except where the girts cross over the posts.
-ccSPUF performs exceptionally as an air barrier. This means it also normally insulates to its nominal R value. Most insulations don't perform to their nominal R value in practice because circulating air currents in the wall cavity commonly occur due to less than perfect installation of any of the following: inside air barrier, outside air barrier, insulation material.
-Workflow efficiency can arise from not trying to perfectly detail multiple control layers at multiple stages of the project. In my case I can hire a crew to quickly and efficiently erect a building to lockup without worrying about membrane details. It's one less thing to teach the crew, one less thing to worry about, one less thing to go wrong. The only trade that has to do a good job to achieve predictable, nominal thermal performance is the SPUF contractor.
-Did I mention that most buildings being built today leak a lot of air inside the walls? Most batt insulation jobs don't achieve their nominal R value. In the high-performance building community we all know that. Most of us focus on putting lipstick on the pig really well. I'm playing with a framing method that to my eye seems to be a diamond in the rough. I think she's quite a beauty underneath the greasy overalls and the dirt from her years on the farm.
Dan,
Thanks for the reply - and sorry if I was telling you things you already know. When you first reply to a poster here it's sometime hard to know if they are a first time DIYer or an experienced builder.
My only experience with post structures was building a single storey one. Have you given any thought to how additional storeys would be best supported?
Simple 2x6 cross grits with 5" of SPF won't reduce thermal bridging that much. You need to fully cover the 2x6 with SPF, about 1" at least. It doesn't mean that you need 6.5" of SPF, you can keep it at 5" inside the cavity and carry it over the 2x6. If you do that, that is a pretty decent wall assembly.
Lot of spray foam though still, far from green. Consider open cell spray foam for the walls at least, that uses about 1/4 the polymer of closed cell foam.
If you do spray over the 2x6, it means you need some extra framing to install any interior finish as it can no longer be mounted onto the cross grits.
I know it is common in rural areas, but I'm not a fan of any exposed fastener roofing. These will all eventually leak, which is not an issue for a barn, but expensive to fix for a house. Once they start leaking, you either have to redo the whole roof with larger new screws or play whack-a-mole till the whole roof is replaced. Spend the extra bit and go for a hidden fastener roof. I know the cost delta is pretty steep.
Loving your idea! Great to see you doing this at a younger age, too!
Here is my idea: https://www.youtube.com/watch?v=CSaow6ahLz4 sorry about the quality It's not a pole barn, but I have been trying to build for a couple years but cannot find resources in my area to help. Maybe I'll ditch the basement and do something like what you're doing! May I ask what software you used to create your illustrations?
Hi Drew, I haven't drawn this building up yet myself. Erik Olson above has done nice drawings for his build. Erik what software are you using?
With regards to basements, I haven't personally found a basement to be necessary. Many people like them however, and if you have tornadoes in your area there's a compelling case to build one. If I was going to do a basement on my home I would do a full ICF basement built up 4' above grade so as to provide space for large basement windows.
If low build cost is your goal and you don't require a basement for tornado safety or other reasons, consider pier and beam foundation if it's suitable in your area, or casting a slab on grade with frost protected shallow foundation detail.
Software is Autodesk Fusion 360.
I am not a big fan of spray foam, probably because of my experience with chemical sensitivities and because my first case as a law student/intern was defending the Urea Formaldehyde Foam Insulation (UFFI) industry as it imploded in a wave of lawsuits. Of course, modern spray foams now use different blowing agents, but still, something about curing complex chemicals on site makes me nervous...
On the other hand, I love the idea of using post frame construction for energy efficient construction for two reasons: (1) post frames outer shells go up quickly and the basic packages are cheap compared to stick build, and (2) they reduce the use of concrete in foundations. If you want an example of an inexpensive post frame house that is near near passive house standard built without spray foam or exterior sheathing, check out the this video on the Four Seventy Five High Performance Building Supply You Tube channel: https://www.youtube.com/watch?v=PKXNwdvUNj4&t=34s
I too have concerns about currently undiscovered or underreported harmful emissions from SPUF installed on site. And I too had some exposure to the boondoggle of UFFI doing some remediation during a house renovation in my youth. Apparently there have been many cases in the USA and Canada where either poor quality SPUF were used that didn't cure properly, or else (and more likely if using certified chemicals) the installer doesn't maintain the very tight ratio of chemicals being mixed as they're applied. I understand that a less than excellent installer can use expired chemicals, an improper mixture, or something like poorly maintained foam application equipment can lead to a foam that doesn't cure properly. Uncatalysed foam ingredients could emit odours or harmful chemicals that were supposed to be eliminated or neutralised during the application and rapid cure. All of my research to this point is showing the need for an excellent installer for this reason and others. The foam can do an excellent job at several tasks but if it's applied poorly it can fail at all tasks and leave a smelly and or toxic mess.
Post framing can be done with or without a concrete foundation but it's exciting how well it can perform without. I'm not entirely convinced that air sealing the bottom of the walls can be made to perform reliably without putting the post frame on a concrete foundation, however. If I have enough reasons to pursue the Perma-Column foundation approach I will try to come up with a good air seal design, but in the case of my main question now I am asking people to assume that I'm using a conventional slab-on-grade foundation which can be air sealed to the walls in all the usual ways.
This is similar to the 2000'sdecade when metal buildings were cheap. They are designed to deflection limits that are not compatible with drywall interiors. When you ask the metal building supplier to decrease the deflection limits to be compatible with drywall finishes the cost go up, and kill the cheap building shell concept. The youtube video's showing post frame buildings are most likely in Texas with no codes.
Hi Tim, shear strength in buildings is an important consideration. I would be very concerned about deflection in any building, post frame or stud frame, if it was built without without proper bracing. Wood sheeting, if done properly, is a good way to brace a wall for shear strength. In my case I'm considering using the post frame with heavy metal siding and spray foam adhered to the metal. In this case the metal acts as a structural diaphragm adhered tightly to the wood framing members because of the SPUF. My experience using this principle is that it does stiffen the wall far more than just using sheet lumber nailed to a stud frame. This document shows the results of tests, where spray foam in a stud wall sheeted only with drywall was twice as strong as a wall sheeted with OSB and no foam: https://www.sprayfoam.com/content/spf-strengthens-buildings/35
In this case, I would be concerned about deflection in a 24' tall building whether I build stud walls or post frame. I am far more confident in low deflection if I use SPUF directly adhered to the structural diaphragm members.
Be sure to read today's post and follow Randy's "barndominium" build: Post-and-Frame Construction. He plans to share details to improve what might otherwise be an inefficient structure.
Great, I look forward to seeing what Randy comes up with!
I looked at your SPUF link, It Iooks positive but I could not find any ICC reports for Spray foam as a structural building element. Can you post a reference for design values for shear?
I am familiar with steel deck diaphragms but not with metal siding used as shearwalls. Can you post a reference that has allowable shear values for metal siding?