Looking for help on our cathedral ceiling insulation detail
I’m the owner and builder. 1300 sq. ft. addition in southern Maine, Zone 6. Simple salt box design. Rear roof 3/12 pitch. Front roof, 6/12. 17′ high at ridge beam, sloping to about 8′ in rear.
Thanks for your time,
Tony
GBA Detail Library
A collection of one thousand construction details organized by climate and house part
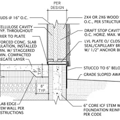
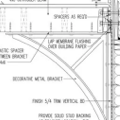
Replies
This article is a good starting point. https://www.greenbuildingadvisor.com/blogs/dept/musings/how-build-insulated-cathedral-ceiling
Tony,
I suspect that part of your question got cut off, because you tried to cram too many sentences into the title of your post. If you have a specific question, post it as a comment on this page.
Otherwise, as Steve suggested, you can read this article: How to Build an Insulated Cathedral Ceiling.
Martin,
New to being a member of GBA. I have read extensively about cathedral ceilings and talked to knowledgeable builders about it. But, still had questions. My post was very long, because I went into detail outlining how the building is constructed, how it will be used and two different assembly options. It did show up after I sent it. Was bummed to see only 2 sentences this AM. Didn't realize first box was for title. Will rewrite.
Tony,
When I saw the question this morning, it had only 7 sentences in the title, ending in the word "rear." The rest of your post was cut off by the site's software.
I transferred all of the sentences to the body of the question, where the sentences belonged. I didn't cut anything. Sorry that you have to re-write your post.
Thanks Martin,
The 1300 sq' addition, front section, will be a 2+ garage that 95% of the time will function as a wood and metal working shop for me. The rear of the building will be, a mudroom, my partner Marie's art studio and a storage room. Marie's studio and the storeroom have been configured and plumbed should we want to make them into a bedroom and bath. Floor is concrete with radiant heat.
Roof is 2x12's 2' O.C. Sheathed with Advantech. 3/12 pitch has full Ice and Water coverage. Rafters will have 2" added to bottom to allow for 11" Roxul Comfort Batts and 2" vent at top. I have spent a lot of time pondering ways to air seal the vent. East coast Roxul rep sent me this link and is swaying me away from air sealing at top.
https://static.rockwool.com/globalassets/rockwool-na/downloads/research-letters/research-letter-n11--anhab.pdf
So, that is one point of discussion. I have 3 ideas for insulation below rafters. All 3 include 1x3 strapping which drywall installer recommends and I fully understand. Part of my concern is fire. I will be welding in my workshop and it may very well become a garage when I move on.
#1. A vapor barrier across rafter bottoms to meet local code. Not a fan of Poly, but it may have to be. Then, 1 1/4" Roxul Comfort Boards. 1x3 strapping and 5/8" sheetrock.
#2. 1" taped XPS, strapping and S/R. Inspector said this would satisfy him for vapor barrier.
#3 1" taped Thermax, strapping and S/R.
My thoughts.
#1 I'm a big fan of Roxul, but this will be extremely labor intensive in many ways. Placing and taping the poly. Comfort Boards are heavy. 4x8 sheets very difficult to handle according to Roxul. Remember, ceiling is very high. 2x4 Comfort Boards mean 160+ pieces instead of 40+. Lots of screws and washers. There are in between sizes I could consider. Attaching strapping will be tedious to get into plane. I.E. driving screws to compress Roxul evenly.
#2. Cheapest assembly. Easy to install and tape. Horrible fire protection. I know, it's under sheetrock.
#3 Thermax polyiso. Has much higher fire rating than XPS. Can be left exposed in US, but not in Canada. Easy to install and tape. Most expensive assembly of all three. Double the cost of XPS, Roxul is in between.
Thanks,
Tony
Thermax is considerably more environmentally friendly than XPS due to the differences in blowning agents used.
Aside from the ignition time issue, even when burning polyisocyanurate (like polyurethane) chars in place rather than melting. Polystyrene (XPS, EPS) will melt, dripping burning liquid polymer as it burns.
The facers of Thermax are also true vapor barriers, eliminating the need for a separate vapor barrier layer to meet local code.
Tony,
If any GBA readers are wondering what "S/R" means -- I was certainly confused at first -- I think it stands for Sheetrock (that is, gypsum drywall).
Your local code official is wrong about the need for an interior vapor barrier. The code only requires a vapor retarder, not a vapor barrier. Polyethylene is not required; vapor-retarder paint on the drywall is adequate to meet code requirements.
Moreover, as Dana noted, either polyiso or XPS qualifies as a vapor retarder. So skip the polyethylene.
John Straube, along with colleague Randy Van Straaten, conducted the windwashing study for Roxul. For more information on the study -- which incidentally focused on wall assemblies, not roof assemblies -- see this GBA article: Windwashing in Exterior Mineral Wool.
If you plan to install 5/8-inch drywall, I think your worries about fire safety behind the drywall are overblown. Any one of the assemblies you list will be safe. I would choose the assembly with polyiso -- it doesn't have to be Thermax, because you won't be leaving it exposed -- to avoid the hassle of lifting heavy mineral wool panels.
Not only do XPS and EPS melt, they do so at a surprisingly low temperature--around 200°F.
I just spec'd a system similar to your #3 on a project in central Maine. I think it's a good way to get a decent roof assembly. You can get Thermax with a white facing ("Thermax WF") if you want to leave it exposed on the interior. If you are going to cover it with drywall or another thermal barrier, any polyisocyanurate insulation will do the job. You can get foam used and as factory seconds from a couple of places in MA and one or two in ME.
If you want to avoid using foam at all, you could furr the rafters down with separate 2x4's in plane with the rafters, connected with plywood gussets, and add a second layer of ComfortBatts. It would take slightly more depth to reach the same R-value as polyiso, but not much. If you need a vapor retarder other than painted drywall, Certainteed Membrain is much safer than poly sheeting (though it looks similar) and it isn't as expensive as the fancy European membranes, though it's also less durable.
I wanted to thank all of your for your responses. Sorry for the S/R (sheet rock) abbreviation.
I'm leaning towards the polyiso assembly. Reading about the shrinkage and drift issues with foam boards was confusing and has me a little concerned. Canadian commercial roof tests show 4x8 sheets with gaps around 1/4". Also their tests show the foam degrades over time and the studies weren't that long in my opinion. Its performance in cold and hot extremes is also not as good as Roxul, but it would be on the inside of the assembly where temperatures will not be as extreme.
Our 64 year old building roof and wall sheathing looked brand new last year after stripping off roof shingles and the original cedar side shingles and felt. Can I be confident that these products will be as long lasting?
Martin if I go with the polyiso I wouldn't be confronting my inspector over vapor retarders, but I am curious about only needing a Class 3 Vapor retarder in the ceiling here in Maine. I tried to find the code section, can you give me that code reference?
Michael, checked out your website, nice work!
Thanks,
Tony
Martin, Do you feel the Roxul windwashing study for walls, does not apply to a vented roof? Have about 700 lin feet of 2' rafter bays. This is a costly, tedious job in a ceiling that gets to 17 feet high.
Thanks,
Tony
Tony,
As John Straube discovered, wind-washing is less of a problem in the denser varieties of mineral wool than in ordinary mineral wool batts. It's also true that wind-washing is less of a concern in mineral wool than fiberglass.
There is a spectrum here: Fiberglass batts are the worst. Ordinary mineral wool batts are better than fiberglass batts. Semi-rigid mineral wool panels are better than ordinary mineral wool batts. And air-sealed ventilation baffles are the best.
As you develop your specs, you have to decide where you want to end up -- and that depends in part on the amount of time you have, and your budget. Good luck.