Log home insulation retrofit

I’m exploring strategies for insulating an existing log home. External insulation makes the most sense to me. What are thoughts and comments about this assembly: 2×4 stud wall with closed cell spray foam covered with r-sheathing? The sheathing is needed because I think the budget will require vinyl siding. I’m not sure about air barrier and a drainage plane tho. Any comments or suggestions would be appreciated. Also thought about a nail-base sip, but I’m concerned about how to attach it, and possible thermal bridging if long lag screws were used….
GBA Detail Library
A collection of one thousand construction details organized by climate and house part
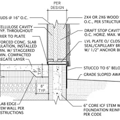
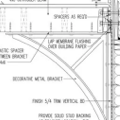
Replies
Closed cell foam installed between studs is waste of foam due to the severe thermal bridging of the studs: 3.5" of R6/inch foam in a 2x4 wall at a 20% framing fraction comes out at about R12.7 average performance for that layer of the stackup due to the thermal bridging of the R1.2/inch wood over 20% of the surface area.
Since the studwall is not structural, turn the studs sideways the bottom & top plate, leaving 2" between the stud and the logs, then spray 2" of closed cell to bring the foam up tight to the turned studs, then fill between the studs with the fiber insulation of your choice. (Split R15 rock wool trimmed nicely and compressed into place is probably the easiest/best DIY.) that stackup would run about R10 whole-wall for the foam layer (which still has the thermal bridging of the top/bottom plates and any window framing), but about R3 average for the fiber & turned stud layer for a comparable thermal performance using only 2/3 the foam at a lower cost, and lower environmental impact. You also get a continuous air barrier/vapor-retarder over the logs.
With 1.5" R-sheathing it would add about 6 to the total, so you'd be around R20 or the new exterior stuff, plus the R value of the logs & chinking layer.
A 4" thick nailbase EPS roofing panel approach, through-screwed to the logs 24" o.c. with timber screws would deliver about R15. 4" thick nailbase polyiso panels would be about R20 nominal, but would perform more like R18-ish in a US climate zone 6 winter due to the necessary derating of the polyiso for cold temp applications.
Thank you, very good detailing. I agree with judicious use of spray foam. Would the dew point occur at the rock wool so it would act as a drainage plane, meaning I should detail a way for condensation to leave the assembly at the base?
I forgot to state that we're in climate zone 5....
So my fears of thermal bridging with timber screws is unfounded with the nailbase panel approach? With this strategy, the sealing of the logs would be critical and more labor intensive/ fussy than applying closed cell, I think.
Don't forget that although your logs have dried and shrunk over time they still move seasonally more than you might think. Any strategy you devise should take this into account both in the way the exterior studs are fastened to the logs and whether you choose to use spray foam on a substrate that isn't all that stable.
"Dew point" is a temperature not a physical location within a stackup.
The dew-point of the interior conditioned space air is only relevant if there is air-leakage or significant water vapor diffusion paths out to a layer whose average winter temperature is below the the average dew point temp of the interior air, and accumulating in a material (like wood) that is susceptible to moisture.
With 2" of closed cell foam between the logs and the rock wool they are essentially isolated- since the foam is an air barrier, and a at 2" is class-II vapor retarder (at about 0.6 perms, give or take, depending on manufacturer and actual installed density.) Rock wool is not susceptible to moisture damage, and though it's fairly air-retardent it is extremely air & vapor-permeable. An exterior air-barrier is recommended for the rock wool, and a sheet housewrap will do, which is also highly vapor permeable, so the susceptible wood can still dry readily into the inherently vented air under the vinyl siding.
Spray foam is fairly flexible (though open cell foam is more flexible than closed cell), and is more likely to remain air-tight over time with the seasonal dimensional changes of the logs than a naibase foam panel approach, but if you detail an exterior housewrap as an air barrier (always recommended) the overall air-tightness of the assembly is preserved.
If we go with r-sheathing with taped seams, would housewrap be necessary?
Sandra,
If you are referring to the product from Huber Zip -- Zip System R-Sheathing -- then the manufacturer asserts that no housewrap is necessary. However, if you prefer to use a housewrap over this type of sheathing, there are no downsides, and several possible advantages.
For more information, see All About Water-Resistive Barriers.
Martin;
Thank you for pointing me to that article. If I'm understanding that correctly, if we add the WRB to the r-sheathing (yes, I'm referring to Huber Zip) that it won't be an air barrier but rather what the name states, a 'water-resistive barrier'. The r-sheathing, taped, would be the air barrier? I like the security of the WRB, but want to clarify in my mind what each element in the wall system is contributing.
Sandra,
You've got it right. If you install both, then the taped OSB is your air barrier, and the housewrap is your WRB.
How easy is it to 'split' a batt of mineral wool? Any tips/tricks on that would be appreciated, thanks!
A long scalloped-bladed bread knife works pretty well for splitting/trimming/shaping rock wool batts. Something with a blade 10" or longer works better for splitting batts than a stubby 8-incher, though shorties can be handier for shaping full-thickness batts around electrical boxes etc (which isn't going to be your issue here.) It doesn't take some fancy high-end Euro-designer knife, a $10 (or less) cheapie does the trick.
http://www.foodservicewarehouse.com/bread-knives-9-10-blade-length/c1962_88-75.aspx
Or you can see what the local box store has for insulation knives/saws, eg:
http://www.homedepot.com/p/t/203240686#specifications
http://www.lowes.com/pd_117475-1278-GRKNIFE_0__?productId=3467721
Thanks Dana - I hoped it would be that simple!