Leaky house and oversized new HVAC systems?

We bought the farm, so to speak in the deep South – a 1-1/2 story house built in 1950. We are looking for thoughts on dealing with a very leaky house with historic ductwork and new, oversized HVAC systems.
Upstairs are with two rooms and a bath finished in the old attic space with knee walls insulated with fiberglass batts. The attic space has very minimal blown in fiberglass insulation. The remainder of the exterior walls are, from inside to out – dimensional boards, asphalt paper, an air gap, and brick veneer. The subfloor is similar to the walls – constructed of diagonally placed dimensional lumber with nice oak hardwoods over them. The previous owner insulated the crawl space with fiberglass batts between the joists.
Blower door testing showed we had a whopping 84% natural air exchange (4300 CFM50). Duct blaster testing showed 34% leakage from the ductwork in the crawl space and 20% leakage from the ductwork in the attic.
To top it off the upstairs (about 500 square feet) is served by a 1.5 ton 13 SEER heat pump (2007) with ductwork in the unconditioned portion of the attic. Downstairs (about 1400 square feet) is served by a 3 ton 13 SEER gas pack unit installed in 2010 with very old ductwork in the crawl space that sweats and drips in the summer.
There is too much heating and cooling capacity for the existing house. When we tighten the building envelope, re-insulate the attic and kneewalls, and fix/replace the ductwork, the effect of the oversized HVAC systems will be amplified. The energy auditor cautioned that, if airseal and insulate but don’t replace the oversized systems we may end up with mold issues. His mechanical contractor thinks he can ratchet down the existing systems and it might work. He recommended humidity monitoring in the house, especially during the summer and noted that we may very well end up replacing the systems anyway. Moisture levels in the crawl space joists in August were 12-17% and there was no evidence of mold/mildew.
The house is managing the flow or moisture pretty well but not heat and air. I would prefer to control the source of fresh air entering the house. I’d like to replace the leaky crawlspace ductwork to reduce condensation adding to moisture in the crawl space and improve the air quality in the house. I don’t have the budget to replace basically new HVAC equipment.
If you had about $10k to spend on this, what would you do?
GBA Detail Library
A collection of one thousand construction details organized by climate and house part
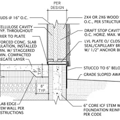
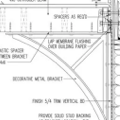
Replies
Are ductless heat pumps common in your area?
Sue,
So you have enough money for air sealing and insulation work, but not for HVAC equipment work? Well, I suppose that's better than the other way around.
Once your air sealing and insulation work is complete, you won't have to operate both HVAC systems any more. You may be able to heat and cool the house with just one of your two units.
David - Ductless heat pumps haven't really taken off here aside from in sunroom additions and historic homes. I met a dealer last night and am going to have him make a home visit. The quote to replace the ductwork under the house was $6k. If I went with a ductless heat pump, I could eliminate the ductwork in the crawl space. He suggested closed cell spray foam to insulate the crawl, which would help air seal it too.
Martin - the ductwork for the two systems is completely separate. One serves the upstairs and the other serves the downstairs. A home inspector suggested I run the fan 24/7 on one system and let the other heat/cool, swapping upstairs vs. downstairs seasonally to let cool air "sink" in the summer and hot air "rise" in the winter. We pretty much live in the downstairs, so running the first floor unit only would be an option.
I think the plan will be to air seal the house, insulate the attic, and then see how the house functions and how much money we have left to go ductless downstairs and spray foam the crawl. Save our pennies, and do it later next year.
It's a fools errand to try to air seal a knee wall to the mini-attic floors with good success. (Take it from somebody who has played that fool multiple times!) The easier and more reliable approach is to insulate and air seal at the roof deck, eliminating all attic venting.
Before you do that make sure that the brick veneer is vented to the exterior, not into the attic. If it's venting into the attic you'll have to provide top venting to the exterior under the eaves before sealing the top of the cavity. (Drilling 1/4" holes at an upward angle every 2nd or 3rd mortar seam is usually enough, or you could core out ~1-1.5" holes every few feet in the bricks themselves and use a screened vent-plug.)
If it's a plank-sheathed roof deck behind the kneewalls (as it might be in 1950 construction) you can do a world of good adding 5-6" of open cell foam to the roof deck all the way down to the soffits as part of the air-sealing, bringing the attic ducts inside of conditioned space. Pull any insulation on the kneewall space floor back from the soffits to allow the foam installers to get a good seal, but there's no good reason to pull it all out (or the insulation on the kneewalls) in your climate, and keeping it would still help reduce the cooling and heating loads for the house.
If it's a plywood roof deck that gets shade most of the day or with very-light/white shingles there's a very slight risk of wintertime moisture accumulation if you went with open cell foam, but a flash-inch of closed cell foam would be enough to protect it, and you could then do open-cell to fill it out to the full rafter depth (or a bit beyond.)
If it's a dark roof with little or no shade, don't sweat it, open cell is fine with a plywood deck. If you're planning to re-roof in the next 5 years you could go ahead with an open-cell solution and add an inch of EPS or iso beween the new shingles and it would be fine no matter what. The IRC code specifies R5 above the roof deck for climate zones 1-3, but there's some margin in that, especially with open cell foam rather than fiber on the interior side of the roof deck. The more R you put above the roof deck, the drier and happier the roof deck and rafters would be, but if you go more than an inch above the roof deck you'd have to hold it down with 2x furring through-screwed to the rafters 20" on center, and add an OSB/ply nailer deck to the furring. That would all be a good idea, but might not be in the budget relative to a 1" foam nail-through solution. But 3" of iso above the roof deck + 6" of open cell under the roof deck would put you at a pretty-good R40, and would outperform a fiber-solution R50 due to the R18 thermal break over the rafters.
Whether you go for a ductless solution or re-do the ducts it's still a good idea to seal & insulate the crawlspace to at least R8.
Vented crawlspaces represent a huge latent load to the air conditioning, and are usually a huge air leak adding to the heating load as well. A heavy 10mil poly or EPDM vapor retarder on the floor lapping up a good 8" onto the foundation walls and either 2" of closed cell foam sparyed on the wall or 2" of EPS or iso cut to fit with foam sealed edges all the way from the ground vapor retarder to the foundation sill & band joist is in order. The sprayed closed cell is quicker, but the rigid foam solution could be DIY a much lower cost. If the inspectors will sign off on it you can use furring through -screwed to the foundation 24" o.c. and use intumescent paint for an ignition barrier for the foam. If you used fire-rated polyiso you could skip the ignition barrier, and use polypropylene plug type fasteners, as detailed here:
http://blog.energysmiths.com/2011/08/basement-insulation-part-3.html
If this is in a termite prone area you may be required to leave a 2" inspection gap, but that shouldn't stop you from being able to air seal it.
As with the attic, any insulation between the floor joists can be left alone. But monitor the RH in the crawlspace with a cheap $10 battery operated humidity monitor (AccuRite or other), and if the humidity climbs to 60% RH @ 70F or higher you'll need to actively do a modest amount of air exchange with the conditioned space.
For less than the $6K quoted for the crawlspace ductwork you could probably install a pair of 3/4 ton mini-splits (one upstairs, the other down- maybe one of them should be a 1-ton if there is a lot of west facing glass making a high peak-cooling load), and get sufficient cooling & heating for the house at the "after" picture of air sealing & insulation.
In general insulating without air-sealing would be a problem using the old heat pumps for cooling since they wouldn't run long enough to keep the moisture levels down. But those latent loads are primarily from the air infiltration, so if you take that 4300cfm/50 down to under 1500cfm/50 that load is largely dealt with. If insulating the roof deck with open cell foam it's good to pressurize the house with large window fans blowing inward and smoke-test the soffits for leakage before they break down- sealing the soffits while crawling around in a space suit dragging a spray gun & hoses is an uncomfortable & awkward job, and it's easy to miss spots, but it's usually easy to fix those spots once you've located them.
Wow, Dana,
Lots of good info (and experience).
The house was an estate sale and the little lady who lived in it before us replaced the roof shingles in 2011 with high albedo asphalt shingles (very light) and also installed new Low-E argon filled dual pane windows and the heat pump and gas pack. If she had air sealed and insulated before changing the HVAC units we would have been in great shape..
We are in a termite prone area and the house had a terrmite and powder post beetle infestation in the past. We're also on the edge of a coastal flood zone (next street over is out of the zone) so we have to keep the crawl space drainable for insurance purposes. We have two layers of vapor barrier in the crawl space but it's not well sealed. The foundation is brick with brick piers with a capillary break. I'm still thinking closed cell spray foam under the floor would be the best way to go to airseal and insulate the crawl space and improving the integrity of the vapor barrier while allowing drainage for flood insurance (keeping the mortgage in tact).
On the attic, I had thought about spray foam and incorporating it into the building envelope - that would get the upstairs ductwork inside the envelope. The roof peak space is so enclosed due to the room additions, that I'm not sure they could sprayfoam it. There's a head and shoulder access where you can look into the space but I don't know how they'd manage to spray it. The roof has a ridge vent and I can't see the roof underlayment because there is plywood parallel to it supporting a layer cellulose insulation (old brown powder). We do have soffit vents but there's really no baffles to allow ventilation to flow from the soffits to the ridge.
I'm going to call the mini-split guy and have him take a look. He knew a bit about spray foam too. I'm seeing more and more spray foam installers marketing in our area and will have to figure who's good.
You can still insulate the crawlspace walls and use operable ports where the vents used to be. Insulating the crawlspace walls couples the house to the thermal mass of the earth, which has a fairly optimal deep subsoil temperature anywhere in US zone 2, and much of zone 3, which would lower the cooing & heating loads more than insulating under the floor. (It's probably less foam too.)
Without a continuous path between soffit and ridge neither are providing much function, and it doesn't really change the picture for insulating under the roof deck where it's accessible. Closing off the soffit vents won't affect the ventilation at the peak enough to really matter.
Dense-packing cellulose into the peak area (and in the sloped ceilings) and sealing the ridge vent holes with 1part can foam before putting the ridge-capping shingls down would probably be more protective to roof than leaving it as-is. See the WUFI simulations in the "cellulose" column for Miami, Houston, and Atlanta in Table 3, p.12 (.pdf pagination) of this document:
http://www.buildingscience.com/documents/reports/rr-1001-moisture-safe-unvented-wood-roof-systems
Anything over 2.8lbs/cubic foot dense pack pretty good- more than 2x tighter than loose-blown low density, but it'll be measurably tighter if you get it over 3lbs. At 3.5lbs it's about 2x as tight as at 2.8lbs.
One real virtue of dense-packing cellulose over a "point and shoot" foam application is that the blown fiber finds and wedges into the exfiltration area, since it's pressurizing the cavity. This tends to seal it up VERY well, even if it's not perfect, usually better than a typical imperfect & untested/spot-remediated foam job. (Some foam installers will use theater smoke generators and blower doors to find & fix the leaks, but that's probably fewer than 1% of the foam contractors out there.)
As a general rule it's better to skimp on closed cell foam, since the current generation of HFC blowing agents pack a significant lifecycle greenhouse gas potential, as does rigid XPS (the pink/blue/green, sometimes gray stuff.) EPS (the stuff with visible beads) and polyiso (off-white, usually with foil facers) are primarly blown with pentane, which has less than 1% of the greenhouse potential of the other stuff. There are newer/better blowing agents coming on the market soon, but most cc foam is still blown with HFC245fa. The only exception I know of that might be available in your area is water blown Icynene MD-R-200 (and NOT the MD-C-200, which is HFC blown). Open cell foams do not have this issue, but are more moisture permeable, and less suitable for a flood prone crawlspace.
On that subject, EPS is a better choice than iso if it is likely to flood, since it will take on water if submerged, and give it up only very slowly through foil facers. EPS on the other hand takes up about 7% water by volume when submerged for a day or ten, but will give it back up in under a week when the tide goes out if you actively ventilate the space during the drying period. (EPS is used for everything from dock flotation to surf boards to lobster-pot buoys- it will still function as insulation when wet, but it'll lose about 10% of it's R at full saturation, which is restored when it dries.)