Laminate my 2 x 4‘s with another 2 inches or more insulation?

I have a table saw and can rip all day long, plus I have the time, so I was thinking of upping the exterior insulation thickness.
I am insulating the exterior wall in my laundry room plus the framed area above the finder block wall in the corner of my basement that is above ground.
Between the Roxul and the drywall I am putting into those exterior walls I am planning to use Membrain vapor barrier, with staples and acoustic sealant of course. The laundry room is on a slab in my large 50’s split-level home.
Then I plan to insulate the open ceiling in my basement – it’s making the wood floor in my living room and tile floor in my kitchen very cold. This is after I get 2” of rigid foam in my rim joist sealed in with spray foam.
What are your thoughts? I’m in southern NY.
GBA Detail Library
A collection of one thousand construction details organized by climate and house part
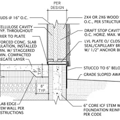
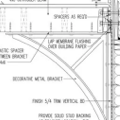
Replies
Jake,
Your question is unclear.
Do you want to thicken each 2x4s with ripped lumber, turning each stud into something like a 2x6? (If so, that's not a good insulation strategy.)
Do you want to add thin strips of rigid foam to your studs (the so-called Bonfiglioli approach)?
Do you want to add horizontal framing on the interior of your stud wall (the so-called Mooney Wall approach)?
Do you want to add a continuous layer of rigid foam to the interior side of the wall? (For more information on that approach, see Walls With Interior Rigid Foam.)
If your furnace or boiler or water heater is in the basement the there is much greater value to be had from insulating and air sealing the foundation walls than there is to insulating the basement ceiling. If you use reclaimed rigid foam for that it can even be cheaper than insulating between the joists.
It's nearly impossible to adequately air seal the basement ceiling due to the myriad plumbing & electrical & flue penetrations. It's easier and more reliable to air seal and insulate the foundation walls, and it puts the basement and it's contents inside of conditioned space, where it's warmer & drier, lowering the mold risk and increasing comfort.
IRC 2015 code min for basement walls in zones 5 or higher (that would include all of NY except Westchester county, NYC and Long Island) would be R15 continuous insulation- 3" of reclaimed roofing polyiso is ~R16-R17.5, and it can be cheaper than R19 batts per square foot(!). If insulating at the basement ceiling between the joist code min would be R30.
https://up.codes/viewer/utah/irc-2015/chapter/11/re-energy-efficiency#N1102.1.2
A description of "southern NY" could more than 200 miles wide, but there are multiple foam reclaimers operating in NY state some of whom advertise here:
https://fingerlakes.craigslist.org/search/sss?query=rigid+insulation
https://binghamton.craigslist.org/search/sss?query=rigid+insulation
https://elmira.craigslist.org/search/sss?query=rigid+insulation
https://hudsonvalley.craigslist.org/search/sss?query=rigid+insulation
https://catskills.craigslist.org/search/sss?query=rigid+insulation
https://newyork.craigslist.org/search/sss?query=rigid+insulation
https://longisland.craigslist.org/search/sss?query=rigid+insulation
https://newjersey.craigslist.org/search/sss?query=rigid+insulation
I was going to thicken my 2x4s into 2x6s. You think I should go the rigid over the insulation route? Maybe 1”?
It's not a matter of "should", but a matter of what you want.
A full sheet of foam over the interior will inhibit drying toward the interior, so a better description of the total wall stack-up (including sheathing & siding types, any weather resistant layers such as #15 felt or housewrap, etc. ) would be useful.
If cutting framing-edge strips of rigid foam, a 4-5" steel wallboard mud knife sharpened on the edges and a straight edge is a lot cleaner than ripping it with a table saw:
https://www.youtube.com/watch?v=KuFWRTEULD0
Or longer straight bladed utiltity knife:
https://www.youtube.com/watch?v=Ckmo6vhSkIY
People also use hot knives, but the fumes aren't exactly the healthiest thing to be breathing.
Jake,
Either adding a continuous layer of rigid foam, or using thin strips of foam at the studs (following the Bonfiglioli approach) does a better job of reducing thermal bridging through the studs than fattening up the studs with lumber.
For that matter, the Mooney wall approach is better, too. Your chosen method is the least effective of the methods under discussion for reducing thermal bridging.
I’m in Westchester County.
I have no furnace. My whole house is electric, but I use wood 24/7 and my wood stove is in an ideal location and heats the house. My basement is a sub basement and is under 50 degrees often. The basement is under the living room and the kitchen, and butts up against the playroom and laundry room, and the ceiling of the stairs going from my basement to the playroom is the underside of the stairs going from the living room to the bedrooms and main bath. We crawled around and air sealed the attic over the living room, laid batts, and blew in fiberglass on top of that. I made sure to put on the vents from OC as well. The attic immediately made a huge difference. My wood stove is in my living room and heat flows across my living room up the stairs to the bedrooms and the main bathroom. We leave our doors open at night and we stay warm that way. Nothing feels warmer than wood heat!
I have an “insulation knife” and I like it- it works well, so I wouldn’t rip insulation on my table saw.
Westchester is zone 4A. IRC code min for zone 4 is R10 continuous on the walls, or R19 under the sub-floor. You may want to do both.
A sub basement is a space below the basement floor. I'm not sure that's what you really mean. Is the basement used for anything, such as storage, laundry, water heater, etc? Is access only from the exterior, or is there some sort of interior stairway or hatch / ladder?
A sub-basement that drops below 50Foften in a location with a subsoil temp of ~52F (typical of Westchester County) is an indication of air leakage into the basement. If the walls are insulated to R10 and air sealed the temperature down there will rise to the high 50s or even low 60s, depending on how warm you keep the first floor.
Is there any potable water or drain plumbing down there? Insulating between the basement and the first floor without insulating the basement walls increases the freeze-up risk.
Summertime air leakage into the base space will load up the floor joists with more moisture after insulating between the joists, increasing the mold risk.
An all electric house heated by baseboards or electric furnace may qualify for decent NYSERDA subsidy on a mini-split heat pump. If a wood stove does a pretty good job of heating the whole house, so would a single mini-split pump. Unlike a mini-split, a wood stove doesn't provide high efficiency cooling & dehumidifcation.
I'm aware of at least one house in Idaho where the house is heated with a mini-split head in an insulated crawlspace (which may or may not work for you), where floor grilles are strategically placed to promote convection, with grilles below the larger windows to put the window-draft into the crawlspace instead of along the floor, and grilles toward the interior of the house to allow the warm air to rise. The fact that the crawlspace ceiling is always north of 70F when the mini-split is running, the floors are never cold, and the utilization of convection to move the cold air to the bottom of the crawlspace minimizes the drafts felt in conditioned space.
Of course that wouldn't do much for you during the cooling season, eh? :-) The owner of the house in Idaho uses a night-time ventilation strategy, which works there due to the low outdoor air humidity and reliably low overnight temperatures. Night time ventilation strategies don't really cut it in Westchester when it's sticky out.
I don’t recall where I got sub-basement from- probably the realtor. It’s a basement- 23’ x 25’.
We use the basement for storage, and I am setting up a wood shop down there. I already am all setup with my dust control.
The insulation I pulled out of the wall had foil on both sides, was labeled Sears Roebuck & co., and for 3” or dirty yellow insulation it weighed a lot.
I really appreciate your help!
My house has vinyl siding. Underneath the vinyl is a light blue rigid foam, under that I believe is the original wood shakes on exterior sheathing. Ipull a lot of water out of the air in the summer in my basement, but then again my air has very humid summers.
Attached is a photo of a wall join in my laundry room. Not sure what to do with that corner, but it’s tempting to pull that inner wall stud out, add insulation and replace it.
My basement wall had so many penetrations it was ridiculous- 2 eclectic, 3 cable tv antennas that easily slide in and out, and a huge hole where the electrician who worked for the NYSERDA certified HVAC contractor ran the electric through to the pump for my ductless mini-split in the living room above.
Re: crawlspace as duct/radiant floor
> Of course that wouldn't do much for you during the cooling season, eh? :-)
You won't get natural convection, but you will still get radiation and conduction and with just a little bit of fan, enough air movement to dehumidify. So would be interesting to see figures on the efficiency loss in the cooling (and heating) season.
How thick is the blue XPS under the vinyl siding? In US climate zone 4 you don't really need interior side vapor retarders, but rigid insulation on the exterior inhibits the sheathing from drying toward the exterior, which would make interior vapor barriers a bit riskier. If it's an inch thick you'd meet IRC 2015 code minimum with just R13 in the wall cavities, though going thicker is still financially rational.
Summertime humidity in basements in northeast is often/usually from outdoor air leakage, with the minor fraction coming from ground water though the slab or foundation walls. Insulating and air sealing the foundation walls with a combination of rigid foam and spray foam can reduce the amount of mechanical dehumidification by quite a bit. If using polyisocyanurate the cut bottom edge should be kept off the slab, since it can wick moisture. If there's a flooding history doing the bottom portion of the wall up to the high-tide mark with EPS would be better. Tape the seams of the sheet foam, and can-foam seal at least the top edge to prevent convection behind the foam. Leaving the bottom edge unsealed to allow drainage is often better to allow a drainage path for any bulk water incursions. Sometimes it's worth putting dimple-mat between the foam and wall as a drainage path, but it doesn't sound like that would be necessary in your case.
JON R: At that house in Idaho the latent loads are all negative, so he didn't need the dehumidification the way Jake surely will. Unless there is a lot of west facing basement window taking in solar gain it's unlikely the basement would have a sensible cooling load.
I justfinally had the opportunity to go outside and look under my siding. There are sheets of light green (not blue) 1” XPS. The seams are not taped or caulked. I lifted the siding around my outside light fixture which is a 1 gang box, and there is a good 6” x6” cutout for the box- which is not weatherproof (yet).
I had a contractor give me a bid on my work a couple of months ago and he wanted to air seal gaps with spray foam and install Intello smart vapor barrier over Roxul. He wanted $1150.00 to do my outside laundry room wall which is 6’ x 7.5’- and that was with me removing the Sheetrock. It seemed outrageous to me.
So, since there is XPS on the outside do I skip Intello or Membrain on the inside after I plug up the air leaks and do the headers with rigid and spray foam?
With an inch of XPS on the exterior, for long term performance derate it to R4.2/ at a mean temp of +75F through the foam (a hot day in summer) to R4.5/inch at a mean temp through the foam of 40F, which is roughly the mid-winter perforamnce. ( see: https://weatherspark.com/m/24859/1/Average-Weather-in-January-in-White-Plains-New-York-United-States#Sections-Temperature << this is the temperature on the cold side of the XPS- it's temp will be warmer at the sheathing.)
Even in climate zone 4C, which has a much longer (if more temperate) heating season and higher anticipated indoor dew points than zone 4A, R4.2 would provide sufficient for 5.5" of fiber insulation in the wall cavities, without interior side vapor retarders:
https://up.codes/viewer/wyoming/irc-2015/chapter/7/wall-covering#R702.7.1
So yes, SKIP the Intello/MemBrain. Just do a good job of air sealing the framing to the sheathing, and make it reasonably air tight at the wallboard layer. Be sure to put a bead of polyurethane caulk on the seam between doubled up framing such as headers and jack studs, and where the bottom plate meets the subfloor, and (of course) the full perimeter of each stud bay.
Thanks for that great info, this brings me back to the point that my framing is 2x4 not 2x6, what method should I use to get to the 5.5” of Roxul I need?
Jake,
If you want to thicken your 2x4 studs so the studs resemble 2x6s, go ahead -- it's your house. But as I advised you in Comment #5, it's not really the best way approach from a thermal perspective.
I saw and understood your answer in comment #5. Comment #13 states “R4.2 would provide sufficient for 5.5" of fiber insulation in the wall cavities,” and I thought that Dana’s statement is telling means I should get 5.5” of insulation in the cavities 2x4 framing, which of course only allows 3.5”.
I live just a couple of blocks from Putnam which is code 5A.
Jake,
To avoid moisture problems in walls that combine exterior rigid foam with interior fluffy insulation, thicker rigid foam moves the wall in the direction of safety; thinner rigid foam moves the wall in the direction of more risk.
With the fluffy insulation, the effects are opposite: thicker fluffy insulation moves the wall in the direction of greater risk, while thinner fluffy insulation moves the wall in the direction of greater safety.
So if your framing doesn't provide enough room for 5.5 inches of fibrous insulation, don't worry. If you install 3.5 inches of fibrous insulation, you won't be increasing the moisture risk.
For more information on this issue, see Combining Exterior Rigid Foam With Fluffy Insulation.
My statement should have read "...R4.2 would provide sufficient _DEW POINT CONTROL_ for _UP TO_ 5.5" of fiber insulation in the wall cavities..." (I plead insufficient caffienation levels :-) ) . With less cavity insulation there is even greater dew point margin.
In zone 4A you don't even need the exterior foam for dew point control to be able to skip the interior vapor retarders. But since foam is vapor retardent it inhibits drying toward the exterior, so it's good to have sufficient foam to keep average temp at the sheathing above the dew point temperature of the conditioned space air. Since this discussion has been about deepening the stud cavities to 5-5.5", it's important to know whether the exterior foam is going to be a problem for thicker cavity insulation, ergo the reference to 5.5". But it is has margin at 5.5", it has substantilly more margin at 3.5".
Martin- got it. Now I can finish my basement and laundry room today and take the money I’m saving on not putting up a vapor retarder and buy Dana some coffee and another tool for my wood shop. I keep trying your link to your “musing” on combining rigid with fluffy but it tells me I have to sign in when I’m already am signed in, and it eventually leads to a page stating this site is down for maintenance. Do you have aPDF handy that you can send me?
Dana- I totally understand the role of caffeine in our lives, and your use of the margin throws me.
Is the site down or maintenance? Because that is the webpage I get every time I try clicking on your link above.
Jake,
Our web site is experiencing problems today, and our technical team is now working on a fix. Sorry for the slowdown.
The rest of the basement is cinder block walls, and I have successfully coated them with dry-look paint over a year ago. I notice in other articles you stated you can use EPS, XPS or ISO, but in this thread you have made it clear about XPS. So, use EPS from the top of the above ground blocks under the rim joists down 4’ will make a noticeable difference? 4’ down would put me at 2.5’ underground. It’s a shame with XPS having a better insulating value, I originally planned on 2” XPS.