Kraft paper on batts with polyiso

I am building a separate accessory structure in Southern California. It has an unvented cathedral ceiling. It has an asphalt shingle roof sheathed with radiant barrier. The plans call for closed cell rigid R-12.5, then batt R-30, then 5/8′ drywall. My plan was to use 2″ polyiso tight against the radiant barrier (roof sheathing). The polyiso would have the foil toward the inside (against batt). Is it better to install the batts with or without kraft paper and which way should the paper face? Toward the drywall or toward the polyiso. Also, would it mater if there is gap between the drywall and the batt or the batt and the polyiso due to the rafters being deeper than the insulation buildup. Thank you.
GBA Detail Library
A collection of one thousand construction details organized by climate and house part
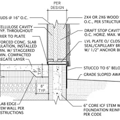
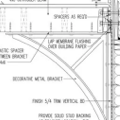
Replies
A radiant barrier only works if it's facing an airspace. If you push something right up against it, you've totally defeated the purpose of having a radiant barrier.
What you are describing is a "cut & cobble" insulation method that is fiddly, time-consuming, and risky in wet climates (thankfully you don't have that problem). The optimal way to do it in this case would be to use the polyiso use to make rigid ventilation channels in each rafter bay by offsetting the polyiso boards about 2" away from the foil surface of the roof sheathing. Face the foil on the polyiso towards the foil on the roof sheathing. Then fill the remainder of the rafter bay with your fiberglass batts and install the drywall. With a vented roof like this, make sure not to forget your ridge vent and soffit vents at every rafter bay.
I assume the sheathing has an aluminum facer on the interior? That facer is already a fairly powerful vapor barrier limiting the roof deck's ability to dry toward the interior and adding foil face polyis would only make that worse. And drying to the exterior through a ~0.1 perm shingle & felt layup is " solamente en sus sueños". It's better to use unfaced sheathing, and an interior drying stackup:
Put 1" of polyiso above the roof deck, between the roof deck and shingles for dew point control per IRC chapter 8, then fill up the rafter bays completely with cheap fluff tight to the interior gypsum board, painted with standard latex paint as the vapor retarder.
http://publicecodes.cyberregs.com/icod/irc/2012/icod_irc_2012_8_sec006.htm
(You are probably in zone 2B or 3B.)
Batts need an air barrier tight to both sides. In a perfect world the kraft facer would provide that function, but it's easier to use the gypsum board for that.
How deep are the rafters?
Thank you for the info. Unfortunately, the roof is already on with the radiant barrier facing the interior and no insulation above the roof deck. It was also designed and approved as non-vented (see attached), so I have no roof vents. After review of the CBC it looks like the this design is in compliance. I am wondering what would be the best way to build this and do you foresee any problems with this design?
The rafters are 2 x 10.
Aaron,
Unless California codes differ, most code authorities would not approve a cut-and-cobble approach. This type of unvented roof assembly (with no foam on the exterior side of the roof sheathing) requires spray polyurethane foam on the underside of the roof sheathing.
For more information, see How to Build an Insulated Cathedral Ceiling.
Martin has it right. Looks like you've painted yourself into the spray foam corner. It's always cheaper to design before building…
So, an inch (R6) of closed cell polyurethane on the underside of the roof deck will set you back about a buck a square foot, then stuffing the rest of the rafter bays with a compressed R38 would get you to about R38 center cavity performance required by code for zones 2B & 3B. Even though a standard density R38 designed for 2x12s would get you there with an inch of ccSPF you may have to go with high density R38s designed for 2x10 framing to please the inspectors, even though the performance difference will be small.
https://www.greenbuildingadvisor.com/sites/default/files/Compressing%20fiberglass.JPG
http://publicecodes.cyberregs.com/icod/irc/2012/icod_irc_2012_11_sec002.htm
That kneewall & ceiling joist insulated mini-attic section is an air sealing (and overall performance) disaster waiting to happen. It's better to take the flash-inch of foam and compressed R38 approach all the way, skip the insulated and air sealed kneewall.