Kraft facing OK if latex painted drywall?

in zone 4c, in the ceiling, is kraft facing needed on fiberglass batt insulation if the drywall has latex paint? Attic is vented. I should ask not f it’s needed but if it’s OK, considering a lot of the ceiling is this way current and would be a lot of work to go back.
One room in the house has a different ceiling assembly, wondering if this is ok:
latex painted drywall -> foil faced poly -> rockwool -> foil faced poly (batt baffle)? This is the only room in the home that is vaulted/cathedral
GBA Detail Library
A collection of one thousand construction details organized by climate and house part
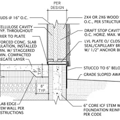
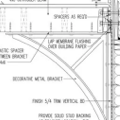
Replies
Anyone have any thoughts?
You don’t need faced insulation in a vented attic, but it won’t hurt if you used it. The facing should face down (towards the warm interior of the house).
I’m not sure what you have for cathedral ceiling. Is this assembly vented? You do NOT want poly on BOTH sides for sure though! You never want a double vapor barrier like that. Your best setup is probably going to be drywall / smart vapor retarder / Rockwool / baffle.
Bill
Bill, thanks for the reply. Please help me understand better the cathedral situation you mentioned. Or let me know if what I have is OK.
The cathedral is what I described in paragraph 2, sorry for the confusion. It is a drywall ceiling with latex paint. Then there’s 1” polyiso foil foam over the face of the rafters w/ seams taped (in between rafters and drywall), then in the rafter bay there’s 3.5” rockwool, then 1” polyiso foil faced. And then there is a 1” air gap.
Kevin,
Having foil-faced polyiso sandwich isn't ideal, since any moisture that slips in (from exterior or interior) won't have a good path to dry. The foil facing effectively makes it a vapor barrier.
It's probably not the worst stack-up possible since you mentioned taped seams on the inside which will help keep moisture entrained air out... but it's still a sandwich with impermeable bread and any little malfunction (water ingress/ air hole) could lead to rotting meat.
https://www.greenbuildingadvisor.com/article/how-to-build-an-insulated-cathedral-ceiling
It's actually pretty good if the seams are taped, since air transport from leaks is a much stronger mechanism than vapor diffusion. It's not a terrible way to go.
With only 1" of rafter between the fiber insulation and the vent space the drying path via adsorb & vapor diffusion through the rafter itself is sufficient even for Class-III vapor retarders on the interior in that climate, and taped foil faced polyiso is a powerful Class-I vapor retarder. It's highly unlikely that a nail hole through the interior side polyiso is going to create a moisture problem here. Any bulk water from roof leaks will roll down to the soffits and have a good chance to drain or dry.
Kraft facers are "smart" vapor retarders, and cannot create moisture traps. When bone dry they run about a half-perm, but when there is enough moisture in the cavity to support mold/rot the facer becomes more vapor open than standard interior latex paint on wallboard.
See also:
https://www.greenbuildingadvisor.com/article/should-the-paper-facing-of-batt-insulation-face-the-inside-or-outside
Dana thanks for clarifying my potentially misleading advice.
So I understand, having a vapor barrier sandwich isn't a problem in this case due to:
1) the rafter allowing drying into the vent space and
2) the seams of the interior polyiso being taped (air-tight)
?
I kinda get it, though its hard not to still feel like it contradicts most given advice, e.g. if using cc spray foam followed by fluffy (flash and batt) don't use interior poly, just for one example.
The more time I spend researching building science (bs) the more I come across seemingly endless contradictory claims made by nearly every prominent building scientist or 'expert.' Sometimes its because our collective knowledge base has changed; other times it's on me for not picking up the nuance that differentiates situations; and other times, I'm convinced, the experts can't make up their minds. With so many words documented, some are bound to fall out of continuity.
edit: this isn't in reference to your advice Dana, so much as the collective building science community. I've been reading enough stuff on various air, vapor, thermal, etc. matters recently to be feeling like the different lines of thought out there are a bit of a snare. The world wide 'web' sometimes lives up to its name...
The difference between the vented roof example and the flash'n'batt wall example is the 1" layer of dry exterior air between the susceptible sheathing (roof deck) and the interior side moisture drive. The interior moisture drive essentially never reaches the roof deck, whereas in a wall it would have to pass through the sheathing (ideally into an exterior side vent gap aka "rainscreen").
In full gut wall retrofits it's often useful or even essential to make a baffle in wall cavities to insulate them. The classic case is stucco clad walls where the lath holding the stucco is nailed directly to the studs, with no sheathing or vent spaces exterior to the studs. While it's arguably to use sufficient R-value foam insulation for dew point control on the fluffy stuff as the exterior air barrier in those assembles, thin rigid plastic or even metal can still be used, letting the fluffy stuff dry through the studs into the cavity space, since the path through the stud is so short and vapor permeable. Insulating right up against the lath all but guarantees failure in most climates, whether the insulation is closed cell foam or fiberglass.
With sufficient exterior side R for dew point control, interior side vapor barriers aren't really necessary or desirable, since it impedes the overall drying capacity of the assembly.
Hmm, interesting. I'll have to ponder this one a bit more.
I do understand that the roof sheathing isn't the component in danger, which is admittedly the bigger challenge to keep safe in comparison to studs/rafters which are not total x-y axis blockages but rather narrower paths with z-axis communications to other areas of the assembly (and can therefor dry via absorption and redistribution when there is a vent space as such).
I do see how this assembly is not 'that bad' or is 'ok,' but I'm still not sure I'd choose (given the option) a foil faced polyiso for the baffle in this case vs something with at least a bit of vapor permeance.
My initial concern was less about the interior moisture drives (unless of course some big hole was created by an unknowing homeowner) but more about a roof leak, which if it did enter the sandwich, would seemingly not have great drying potential.
I would worry that a roof leak (which is admittedly a problem of its own in need of fixing) might not slide harmlessly down the vent space and out if the vent baffles are not sealed against the rafter, and perhaps may be slightly cocked so as to direct water through the crack between baffle and rafter thereby entering the sandwich...
>"I do see how this assembly is not 'that bad' or is 'ok,' but I'm still not sure I'd choose (given the option) a foil faced polyiso for the baffle in this case vs something with at least a bit of vapor permeance."
That's a pretty good instinct to have, but bear in mind that the vapor permeance of milled lumber is pretty high when it's humidity content is high enough to support mold- more vapor open than OSB or plywood. In a standard ASTM E96 wet-cup test a milled 2x plank is about 1-1.5 perms even when the wood itself is relatively dry.
Asphalted fiberboard sheathing makes for a very moisture tolerant vapor permable baffle for insulation. It's normally >10 perms even when dry, yet is pretty much a WRB for liquid water. If asphalted on one side only, have the asphalt facing the vent space.