Kraft-faced Insulation at Shed Roof

The shed roof shown in the attached photo is built with 11 7/8″ high I-joist rafters. After reading this article once again (https://www.greenbuildingadvisor.com/article/how-to-build-an-insulated-cathedral-ceiling), I’m embarrassed to say that I still have a question. For the ceiling insulation, we are planning on using R-38C, which will give us about 1 5/8″ air space above the batts. We have created vent holes in the webs of the I-joist blocking, and rigid foam baffles at the top and bottom of each rafter bay. Please see Eave and Ridge Details, attached. The R-38C is below the code minimum, but we have approval from the building inspector. We have insulated the walls with Kraft-faced R-21. The project is in the Columbia Gorge, in Climate Zone 5B.
Please also see my other question, here:
https://www.greenbuildingadvisor.com/question/insulation-at-lookout-rafter-bays?discussion=edit
Question 1) We DO want to use the Kraft-faced R-38C, right? To provide a vapor-retarder layer. The ceiling will have drywall, with latex primer and paint.
Side note: thanks to supply-chain problems, we’re not sure when the R-38C will be available again.
GBA Detail Library
A collection of one thousand construction details organized by climate and house part
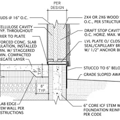
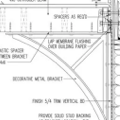
Replies
Miles,
R-49 is usually the recommended target in your climate. Why are you shooting for R-38?
Thanks, Steve. To maintain a 1 1/2” vent channel above the insulation, there’s only enough room for the R-38. I could furr the rafters down, but there wouldn’t be enough headroom. We have approval from the building inspector for the R-38.
For what its worth: R-38 is prescriptively code complaint for vaulted ceilings (greater than 2:12 pitch) in 2017 Oregon Residential Specialty Code:
https://up.codes/viewer/oregon/irc-2015/chapter/new_11/energy-efficiency#new_11
TABLE N1101.1(1) PRESCRIPTIVE ENVELOPE REQUIREMENTS
- note (g) Vaulted ceiling surface area exceeding 50 percent of the total heated space floor area shall have a U-factor no greater than U-0.026 (equivalent to R-38 rafter or scissor truss with R-38 advanced framing).
This holds true all along the Oregon side of the Columbia River Gorge from 4C (Portland/Multnomah County) to 5B (Hood River County and eastwards),
though experience suggests that ‘Dry’ doesn’t really start till slightly further east in the Cascades ‘rain shadow’!
Thank you. And yeah, the fact that our area is considered 'dry' always seemed a bit funny to me. ;-)
Hi Miles,
The inspector may accept R-38, but you have to live with the sub-optimal insulation. If it were my house, I would try to get closer to R-49 to increase comfort and efficiency. You could do this by using a combination of reclaimed exterior rigid foam (5 inches of EPS) and interior air permeable foam or opting for an unvented roof with HFO closed cell (R-20) and air permeable.
It's a lot easier (and cheaper) to do things right at this point in the process.
Thanks, Steve. The metal roof has already been installed. For the reclaimed exterior rigid foam, are you talking about using that on the inside, in combination with the interior air permeable foam?
For either scenario that you suggest, what thickness and spec of interior air permeable foam would you recommend?
Also, reclaimed exterior rigid foam was suggested earlier, when I was insulating the slab, but I could not find a local source. I live in Portland, OR.
For my idea on how to insulate the Lookout Rafter Bays (the ones that are perpendicular to the main rafter bays), please see my other post, here:
https://www.greenbuildingadvisor.com/question/insulation-at-lookout-rafter-bays
The flash and batt approach (the second strategy) is probably the most practical option at this point. Go with the HFO closed cell if possible since this type of blowing agent is less adverse for the environment.
Let's see if one of the experts will chime in. He/she might have a better or cheaper suggestion.
OK, thanks Steve.
I agree that R-49 is a better minimum roof insulation level, but every project is a balance of priorities and the climate impact of a few inches of foam is likely higher than the increased operating emissions of going only to R-38 would be over the next few decades. However, if you can find reclaimed rigid foam you could have the best of all worlds--better energy performance, improved comfort, reduced energy bills and no material-based climate impact.
You will be code-compliant with just painted drywall at the interior--you don't need to add kraft facing, though it won't hurt anything either. It's important to keep the ceiling free of penetrations, or to seal any penetrations--"airtight" electrical fixtures are rarely actually airtight, and cause energy loss and moisture-related problems.
Hi Michael,
Thanks very much. Do you have time to also look at my other question here?
https://www.greenbuildingadvisor.com/question/insulation-at-lookout-rafter-bays#comment-194890
> no material-based climate impact
Every time someone buys reclaimed rigid foam (eg, XPS), they are encouraging the use of more of it. If there were no 2nd buyers because of the climate impact, the original user would re-calculate their net cost and be more likely to buy something they could sell later. So there is an impact. And then there is the fact that around here, it costs the same per R as new EPS.
Jon, I agree, and had second thoughts about wording my response the way I did, in the interest of keeping things simple. Of course providing a secondary market encourages continued use of climate-damaging products. I'd like to know how much the end-of-use value of foam factors into the decision to install it in the first place. I'd guess some, but not a lot--probably close to zero. I am fairly confident that considering all factors, recycled XPS has a lower environmental impact than new EPS, but I'd love to see some data.
I agree, we need more data wrt how much impact. But in the mean time, my advice is to treat it like ivory and "don't buy HFC-134a XPS - ever". Recycled polyiso or EPS - might be an OK idea if the cost is right and non-foam insulation can't be used.
The energy loss difference between an R38 and R49 roof in zone 5 is small enough to not worry about. At my design temp of 2F a 1000sqft roof looses about 1800BTU through an R38 roof and 1400BTU through an R49 roof. When it comes to the energy use of a whole house, I would call that difference noise.
The more important part when dealing with I joists is to get insulation designed for metal studs. These are wider and will fit snugly between the joist webs unlike regular batts.
Getting these and installing them with care is much more important than a bit of extra R value plus you'll loose a lot more by having gaps around your insulation.
P.S. Nice looking build. I like the simple clean shape. Also great job with proper shading.
Hey, thanks! And thanks for the tip about insulation designed for metal studs. I’ll look into that. I’ve always thought it was strange that they don’t make Insulation design for a I-joists.
> We DO want to use the Kraft-faced?
Lstiburek says Class II or Class III in Z5 with a vented roof. I'd use a somewhat smart Class II, so < 1 perm paint, kraft facing or a nylon film (eg, MemBrain).
Not often discussed is that it's all about how much moisture gets in vs how much moisture gets out. So air seal the interior side very well and if you use a vent baffle, make sure it is high perms (let the moisture out).
Hi Jon,
Thanks for the info,
Miles