Knee wall issues in 1.5 story, with added wrinkles

I live in a 1.5 story house, built in 1960, in Zone 5 (Indiana), with knee wall attics in the two upstairs bedrooms. The upstairs has the classic problems associated with this type of construction: it’s cold in the winter and unbearably hot in the summer. I’ve read Martin’s article on two ways to insulate knee walls (which was very helpful!), and I have perhaps foolishly chosen to try to keep the attic as an unconditioned space. I’m also trying to do as much of the work myself, because I’m on a tight budget. I’ve mainly been learning about insulation and energy efficiency through online articles, so my knowledge is a bit sketchy. I know that air sealing is very important for any home efficiency improvements.
A few details about the attic. There are fiberglass batts between the joists and between the studs on the walls, going up the sloped portion to the triangular portion of the attic above the ceiling. I’m not sure what’s in that small triangular space, because there is no access hatch. The roof has several of those box-shaped vents (no ridge vent). There aren’t any ventilation baffles, but there’s a gap between the batts and the slopes and the roof sheathing.
The first thing I did was solid blocking in the joist bays. After that, my attention has shifted to other ways to improve comfort and save on energy costs. One thing that seems like a significant issue is the knee walls themselves. They’re just thin wooden beadboard panels attached directly to the studs. I haven’t encountered any information online about this type of of setup. Above that is drywall, but I discovered there’s about a 1/2 inch gap between the beadboard and drywall, which is covered by a piece of wood moulding. There are also some cracks at some of the seams between panels. I’m looking at replacing the beadboard with drywall before I do any other insulation work, mainly for aesthetic reasons. So my questions:
1. Is this beadboard likely causing a lot of air leakage? I can’t imagine that it’s an effective air barrier, even if it didn’t have cracks or the huge gap.
2. Would drywall possibly create a noticeable improvement, even without additional insulation work?
3. If I can’t get drywall done for a while (or at all), is there any reason to try to seal the gap hidden by the moulding and the crack at the seams, or would it be wasted effort because of the inherent air permeability of the paneling?
GBA Detail Library
A collection of one thousand construction details organized by climate and house part
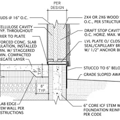
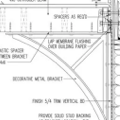
Replies
You should really create some sort of access to the "triangle" attic space at the top of the house to see what is going on up there. The ceiling in a closet is a great place for this if it is an option. How much space is up there? You will want to get up there if possible to seal any openings at fixtures and walls.
Beadboard is not a very good air barrier and drywall sounds like a good idea. Filling gaps and holes is always a good plan. I was thinking you could throw drywall up over the beadboard, but it may make it harder to air seal, although you may be fine. Sketch a profile of the house with all the materials and draw a continuous line that is the air barrier. Think about what is at the transitions between wall, floor, ceiling, and outlets.
Was the solid blocking you did at the floor joist at the bottom of the knee wall and may at the top if there is no header? Some 1.5" rigid foam on the backside of the knee wall to cover the exposed batts would be good, but I would do that after the interior drywall to make it easier to seal outlets.
I would just plan for a proper fix unless it is going to be a few years to do the drywall.
Thanks for the response. As far as accessing the upper attic, there wouldn't be any way to hide it in a closet, since the closets are tucked underneath the sloped portions of ceiling. I'm not too worried about hiding the hatches though. I think there's at least 24" of vertical space up there, between the ceiling and the crest of the roof. I could probably work that out mathematically if I knew the pitch of my roof. The only penetrations in the ceiling that I know of are two ceiling fans and a couple light fixtures.
I'm a little unclear on your question about the blocking. I put 1.5" rigid foam into the joist bays and sealed around them with expanding foam.
I guess one of the overarching questions I have about insulation is whether it makes sense to try to make incremental improvements, or if it makes more sense to just wait, and try to "do it right" in one fell swoop.
Sorry, I may not be picturing things correctly, which joist bays got the 1.5" rigid foam? A photo is always great. Was there a GBA detail or article you were following?
Many approaches can work, but there are a lot of constraints in terms of project scope. It's a complex question that no one here can answer in general as your life is different than any of ours.
I've attached an image from the article showing where I added blocking (https://www.finehomebuilding.com/2012/09/06/two-ways-to-insulate-attic-kneewalls). I completed the blocking at the ends of the floor joists, just below the attic side of the knee wall. I've also attached a photo of the work, and another photo showing the attic space.
One thing you can see in the last picture is that I have ducts in the unconditioned attic. And also a lot of discolored fiberglass.
Looks like my attachments failed to upload. Trying again.
1. headboard air leakage - yes, very leaky
2. gypsum wallboard - is an airtight material (in fact the material on which the definition of air barrier is based: 0.2 liters per second-meter squared at 75 Pascals pressure) BUT each element of an air control layer has to be connected to the next. This is what makes knee wall air control layer continuity so challenging.
3. you can't really seal interior trim: all these materials move so much over time with changing temperatures and moisture content that even if you get them sealed initially, over time they crack and leak.
"Kneewall,"
Can you tell us your name? (I'm Martin.)
In the above comment by Peter Yost about "headboard," I think he meant to type "beadboard."
Yes, tongue-and-groove boards are, indeed, very leaky. So you need an air barrier. You need to install drywall over the existing boards, and seal the seams between adjacent materials to create a continuous air barrier without gaps. That's tough. You also probably need to improve the R-value of the existing insulation.
Thanks Martin. My name is Matt.
Adding insulation is next on my list, but I've been a bit paralyzed on what to do. I've had two insulation contractors out. The first proposed rigid foam over the knee wall studs, blowing in loose cellulose in the flat portion, and blowing loose cellulose into the top triangular area. I don't remember what he proposed for the sloped area. Curiously, he didn't mention sealing the floor joist bays. When I asked him about it, he said it would be a good idea, but it was like it hadn't occurred to him. The second guy proposed doing open cell foam directly under the roof sheathing. I asked him whether any sort of vapor barrier would be used, and he said it wasn't necessary. That set off alarm bells for me because I had been reading a lot of your articles at the time, and that seemed counter to what I had read. Granted, that was only two companies, but it put me off for a while.
Right now, I have two main questions/concerns holding me back.
1. I've read a lot about energy codes and required R values for particular zones. Am I allowed to add insulation that increases the R value, but doesn't meet the code standard? The rafters are 2x6, which means I have very little space to work with, especially if I keep the attic vented.
2. If the answer to #1 is yes, is there a viable way to add insulation to the slanted portion without completely opening up the ceiling (or roof)?
When we bought the house a year and a half ago, I had no concept of any of this stuff. We wanted to use one of the upstairs bedrooms as a nursery for our baby girl, but that's not going to work if it gets 85+ on sunny summer days.
Matt,
Q. "Am I allowed to add insulation that increases the R-value, but doesn't meet the code standard?"
A. In almost all jurisdictions, home improvement work doesn't need to meet current codes, unless the renovations are very extensive. To learn how local code inspectors interpret the code in your area, call up your local building department.
Q. "If the answer to #1 is yes, is there a viable way to add insulation to the slanted portion without completely opening up the ceiling (or roof)?"
A. Maybe. If your third-story attic is large enough, and you are skilled, it's sometimes possible to slide insulation (plus a ventilation baffle) down from the third-story attic into the insulated sloped ceiling. This approach is easier (1) if you are skilled, (2) if the roofing nails don't protrude very far past the sheathing, (3) if the rafters are deep, (4) if the sloped portion of the ceiling isn't very long, and (5) if the third-floor attic is roomy.
In many homes, the only way to insulate this type of sloped ceiling from the interior is to remove the drywall or plaster.
Following up on your answer to #2, on trying to slide in the baffles and insulation. Would the ventilation baffle be attached to the roof sheathing in any way in this scenario, or just sort of held in place by the insulation? Also, what type of insulation would be viable for just sliding into place like that?
It sounds like my space doesn't meet too many of those conditions. I'm not especially skilled, the nails probably protrude about a half inch, and the rafters are only 2x6s. The actual rafter depth, rather than the nominal board size, is 5.5" max. The sloped portion is maybe 4-5' long. I'm not sure how much headspace there is in the upper attic, but it really can't be much. It's probably not viable. If I have to open up the whole ceiling, then I guess I have more options, like making the rafters deeper to accommodate thicker insulation, but the ceiling can only be brought down so much.
At this point, I'm just trying to improve comfort in any way I can, in the most cost effective way. Thanks for providing your input.