Kit Home Wall and Roof Assemblies

Hello! I am considering a “kit” house from Ekobuilt (https://ekobuilt.com/energy-efficient-home-plans/), which bills itself as North America’s most affordable Passive House.
Their strategy is they worked hard on building a weather tight shell plan that they will then ship to folks to work with a local contractor to build. This way, Passive House compliance is easy – just follow the instructions.
On page 8 of this PDF is their wall and roof assembly: https://ekobuilt.com/wp-content/uploads/2022/02/Pine-Valley-House-Plan-2022.pdf
Does this look like a solid, fool proof plan? Our other consideration was to work out the wall assembly ourselves without a kit doing it for us, but I admit I’m attracted to the idea of someone else having worked it out for a similar climate zone, especially since I don’t know what I’m doing.
It seems like there are decent air and water barriers on either side of the insulation. I’m in climate zone 6 by a big lake, so warm humid summers and cold winters. If the insulation gets humid, which direction does this dry?
Thanks!
GBA Detail Library
A collection of one thousand construction details organized by climate and house part
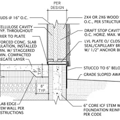
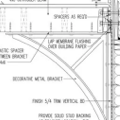
Replies
They appear to have a video with a tour of their model home, the same floor plan, on their website. That might help you visualize the space.
https://ekobuilt.com/ekobuilts-services/ottawa-passive-house/the-new-ekomodel-home/
While watching the video, I did not get the sense that the windows in the model home are in fact in the middle of the wall as suggested in the plans.
Very important, read all the notes in the margins of the drawings and make sure you understand the notes. If you don't I would suggest you ask some questions to the builder.
Slab
The concrete slab calls for wire mesh with some rebar at the point loads. Make sure you or your builder understand how this works. If you want to build with rebar in the entire slab vs using mesh, you will need different plans for the slab.
The text description of E for the slab on page A6 mentions "-VAPOUR BARRIER OVERLAPPED MINIMUM 12"-RADON BARRIER". Just make sure you understand what this means so you can explain it, or if you feel it is necessary ask for the drawing to be clarified. Note that the description of E is just slightly different on page A6 and page A7
Staying with the slab, the insulation is described as -EPS CONCRETE DETAIL (AS PER A1)
40PSI (SRP 400) HIGH STRENGTH INSULATION @ LOADBEARING
AREAS/ EGDES. OTHER LOCATIONS BELOW SLAB CAN BE INSULATED WITH 16PSI
(SRP200). If you are counting on using SRP200 or something with 16PSI, just understand that you have a few posts in the middle of the slab and mixing insulation density might be confusing. Maybe just stick to the 40PSI and keep it simple.
Also, there are no measurements to indicate where the plubming should come through the floor. Just know that you will need to figure that one out youself unless you get those details from the builder. These details are not normally required for a residential building permit so should not expect the city to push for these details on your behalf.
Make sure that you understand where your plumbing vent will exit the roof and how that will work with a prefab roof. It is not a big deal, just understand that. Also think about the connection of the different plumbing fixture (like kitchen sink) to the vent stack - if this is going below the prefabricated roof and how you box that in.
Make sure you understand that the electical is likely coming in under the slab to the electrical panel.
Interior walls
Interior walls, make sure you are happy with 2x4 walls with studs 24" on centre. Normally it is 16" o/c and 24" could result in the drywall being less sturdy, unless you use 5/8" drywall ... which would reduce sound transmission and improve fire resistance rating.
Assembly B1 walls
The wall assembly B1 on the image shows a green line being the vapour barrier under the drywall but I think that the vapour barrier is the OSB in the middle of the assembly. This would be something to check to be sure you don't have any issues with the person approving the building permit. If the vapour barrier is in the middle of the wall, the drawing should be adjusted for you to submit for a permit.
-EXTERIOR FINISH AS SPECIFIED
-1/3" STRAPPING @ 24" O.C.
-AIR BARRIER
-3/4"FIBRE BOARD
-12" I-JOISTS @ 24" O.C. w/ DENSE PACKED CELLULOSE
INSULATION
-7/16" OSB SHEATHING
-2X6 WOODS STUDS @ 24" O.C. w/ DENSE PACKED CELLULOSE
INSULATION Ground Flr. -1/2 GYPSUM BOARD
Wall assembly B2
Wall assembly does not appear to mention the vapour barrier being used on the inside of the wall - required in cold climate. There must be one but it is not specifically identified from what I can tell. Also, I don't see an image of the cross-section of the B2 wall assembly and it might be required for permit purposes.
Windows
The detail of the sloped sill on the window makes me pauses. Look at the attached image. It is not clear how the exterior sloped 2x lumber is attached to the level horizontal 2x lumber under the window. Area is highlighted in yellow.
Roof
The text description of the roof assembly R1 indicates that there is a 5/8" plywood under the metal roof. I don't see the 5/8" plywood identified in the cross-section.
That's all I got.
Okay, very thorough, thank you! I have reason to believe later drafts of these plans (beyond this sample one on the website) has some of these issues fixed (the vapor barrier green line is in the middle of the wall at the OSB panels in later drafts). But fundamentally, I guess a higher level question is "are there any red flags here?" and my summary of your answer is "no, only yellow flags", which is good!
Overall I fully support the prefab idea. We did a site build on the most recent project. I have had experience with prefab construction and you get to iron out all the details upfront - the details that we are discussing here.
I don't have any particular issues myself with double stud walls. You should understand that double stud walls are know for two issues. This plan appears to address those 2 issues relatively well. You can read about these 2 issues in this GBA article. Again, only for your awareness and understanding.
https://www.greenbuildingadvisor.com/question/possible-condensation-risk-in-double-stud-wall-assembly
That GBA article was something I found when replying to another question on double stud walls (you have one stud wall and one I-joist wall). You can read the question and the responses to one of the owner's follow up question if you like to understand on technical issue the owner/builder had to resolve with their city inspector. This is again for your awareness and understanding.
https://www.greenbuildingadvisor.com/question/building-official-questioning-continuous-insulation-of-a-double-stud-wall
Some items i mentioned are actually just for your considerations, like whether you would want rebar in you slab.
The yellow flags are
- the items that would need to be corrected on the drawings. Don't under estimate the importance of this. It is super simple to fix up front, but can be more complex if you don't address it up front.
- the issues of knowing where you plumbing goes is something that they should be able to provide very easily. This is often not on residential plans. BUT! the calculations you need to do can be time consuming and subject to human error. Then you need to communicate that to your plumber with some sort of hand made drawing. Again, don't underestimate the value in getting this level of detail on a CAD drawing. This is something you can negotiate fairly easily before you enter into a sales agreeement but harder to negotiate afterwards.
The issue of the venting stack is not an issue, electrical under the slab are highlighted just for your awarness and nothing more. Similar to the plumbing under the slab, you could easily ask the prefab manufacturer to identify exactly where the electrical conduit needs to come up through the floor. It is so easy for them to do on their CAD drawings and it will remove some of the stress from you. I just can't recommend this enough.
An additional item for consideration is that if you get your window/doors supplied by them, you would want to know who to turn to if there are adjustments required. Tilt and Turn windows are excellent - no argument. They do sometimes need minor adjustments. If they are shipping the assembly to you they will likely not be around to address any issues related to post-construction adjustments.
You may also want to find out about window bug screens because often these tilt and turn windows most often don't come with bug screens. If you want to leave your windows and doors open like they suggest in their video, then of you might want to verify this detail with them.
So thumbs up on prefab
Thumbs up on the assembly
Work to be done
- Get the issues with the drawings sorted out - listed in detail in earlier reply
- Get the plumbing and electrical conduit elements that go under the slab to be identified on the drawings.
- Ask about window adjustments
- Ask about window screens
- Ask about the vent stack through the roof - if the roof is also prefabricated.
Jtolio, I was thinking about your comment that the drawings on the website are rough drawings and not final drawings. I just remembered seeing that those drawings are stamped by an engineer so they are very likely the final drawings. Not a big deal as long as you make sure you get things corrected BEFORE you make a financial commitment. Protect yourself.
Nice job Hugh. We might have to give you a raise!
:)