Judge my insulation plan

Hi All. I’ve been browsing GBA and I think I’ve got a good insulation plan for my remodeling project.
House Stats:
-Fully gutted for remodel
-6″ block walls
-Built-up, low-slope roof (no attic–2×8 joist between roof and interior ceiling)
-House currently has a foam roof (looks like spray foam)
-Phoenix, AZ (dry, hot climate)
Plan:
-We added added furring strips over the existing so that there is 1.5″ of space between drywall and block
-Plan on installing rigid foam board to block on the walls between furring strips. Sealing with tape and spray foam. I realize it would be better to put furring strips on top of foam for thermal break, but we decided not to due to time requirements.
-Planning on using faced fiberglass insulation batts in joist space of ceiling.
Questions:
-Is faced batt installation the proper choice for the ceiling or should I use unfaced?
-By installing rigid foam board to the interior walls, am I limiting myself to not using foam/stucco on the exterior at a later date? I am under the impression that it’s no good to have foam on two sides of block since it locks in moisture.
-What am I missing?
GBA Detail Library
A collection of one thousand construction details organized by climate and house part
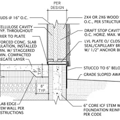
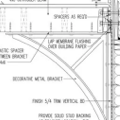
Replies
Will,
This article will tell you how to insulate your roof: Insulating Low-Slope Residential Roofs.
Your wall insulation plan is weak -- low R-value, and made even less effective by cutting the foam into strips. It would be much better to have a continuous layer of rigid foam on your walls.
If you insulate your walls as planned, you can still add exterior rigid foam later.
Thanks for the quick response, Martin. I did read the article (but perhaps I am missing some key points). One of the things I was confused about was whether or not faced batt insulation was impermeable or not. The article recommends having a permeable insulation so that moisture can escape from the inside, but does faced insulation fit this criteria? Also, I have some circular vent holes in the roof soffits on the exterior. Since the article recommends a non-ventilated setup, I'm guessing I would need to seal these off?
Also, do you mind providing a brief explanation of why it would be OK to add rigid foam on the exterior later if I continue with my current interior wall plan?
Phoenix AZ is in climate zone 2B. The large daily temperature swings in arid climates like Phoenix makes the thermal mass of block walls valuable, but you only get that benefit if you put the bulk of the insulation on the OUTSIDE of the block.
Code minimum insulation with at least 50% of the R on the exterior would be R4, but it would still meet code min with only inerior-side R6, if it's a continuous R6. See:
http://publicecodes.cyberregs.com/icod/irc/2012/icod_irc_2012_11_sec002.htm
Unfortunately you've broken it up by furring, which dramatically lowers the performance. If you put 1.5" polyiso between the furring it would hit R9 center-cavity, but the furring itself is less than R2, which robs it of it's performance.
Instead of foil faced polyiso, use 1.5" unfaced EPS, which will deliver ~R6-ish center cavity performance, then install 3/8" fan-fold XPS siding underlayment, which will raise the center-cavity R to about R8, but would raise the furring to about R3.5, which would get you pretty close to code min. The facers on the fan-fold XPS is an issue- try to use something with a vapor permeance greater than 1 perm in an ASTM E96 specification, above 2-perms is better.
To get the benefit of the thermal mass you can then come back at a later date and install at least 2" of exterior EPS or 1.5" of foil faced polyiso.
The block is very tolerant of moisture, but in your climate it's somewhat better to have the lower-permeance layers on the exterior, but not critical. The furring and the wallboard facers are susceptible, but in your climate, with 1-3 perm EPS &/or 3/8" fan-fold on the interior it won't be a problem.
As an alternative: If you're willing to remove your added-on furring and tack strips of 3/4" polyiso onto the old furring it would very nearly meet code-min without the 3/8" fan-fold. At 1.5' thickness unfaced Type-II EPS at would have a vapor permeance of about 1.2-1.5 perms, and the furring would still be able to dry toward the interior through the foam, even if the polyiso is foil-faced. If you go that route you'd be able to reap the mass benefit with as little as 1.5" of exterior EPS added later.
If using faced batts between rafters, they must be kraft faced not foil. If unfaced, it still needs an interior side air-barrier, but it must be vapor permeable.
Dana, I really appreciate the in-depth answer. One final question: should I be sealing the vent holes in the exterior soffits?
Will,
Q. "One of the things I was confused about was whether or not faced batt insulation was impermeable or not."
A. The article distinguishes between air-permeable insulation materials like fiberglass, celluose, and mineral wool on the one hand, and air-impermeable insulation materials like rigid foam and spray polyurethane foam on the other.
With or without kraft facing, fiberglass batts are considered air-permeable.
Q. "The article recommends having a permeable insulation so that moisture can escape from the inside, but does faced insulation fit this criteria?"
A. At no point did the article said that permeable insulation is recommended; nor did the article recommend a roof assembly that allows moisture to escape from the inside. I'm not sure where you got that impression.
You face a basic choice here: whether you want a vented roof assembly or an unvented assembly. In either case, I advise you to follow the recommendations in the article.
A. "I have some circular vent holes in the roof soffits on the exterior. Since the article recommends a non-ventilated setup, I'm guessing I would need to seal these off?"
Q. The answer depends on whether you want to create a vented or an unvented assembly. If you are convinced by my arguments concerning the advantages of an unvented assembly, then you definitely want to seal the soffit vents.
Q. "Do you mind providing a brief explanation of why it would be OK to add rigid foam on the exterior later if I continue with my current interior wall plan?"
A. Concrete blocks are not harmed by moisture. In any case, adding rigid foam on either side of a concrete block wall limits moisture flow -- it doesn't increase moisture flow. A common example of a concrete wall with rigid foam on both sides is an ICF wall. ICF walls perform well, so don't worry.
Will,
When it comes to insulating your roof, here's an important question: Are you willing to install one or more layers of rigid foam above your roof sheathing, followed by new roofing?
If the answer is yes, then I urge you to go with an unvented solution.
If the answer is no, then you either need to install spray polyurethane foam on the interior side of your roof sheathing, or you need to build a doghouse-style cupola in the center of your roof to allow for effective ventilation.
If I understand it correctly, there already is foam insulation above the roof deck:
"-House currently has a foam roof (looks like spray foam) "
That is probably more than an inch of 3lb spray polyurethane at about R6/inch, and even an inch would be sufficient protection from interior moisture drives in that climate.
If that's the case, YES, you absolutely should seal up the soffits, and it's perfectly safe to install batts between the rafters, as long as they don't have a super-low-permeance facer such as foil. Kraft facers are fine, and unfaced is fine, but to get the full performance out of unfaced requires an interior air barrier of some type, but it must be at least semi-permeable to water vapor.
Dana,
Thanks -- you're right, of course. I somehow missed Will Clinton's reference to a "foam roof."
So -- unvented is the way to go.