Arranging rigid foam in roof of workshop

hello, I am in 4a climate…
Tips needed on best arrangement of Rigid Foam install…
Due to condensation issues, need to finish proper underside of ceiling insulation..& add air channel to this 4/12 pitched barn roof.
Layout…
Top layer….Painted steel Ribbed roofing sheets
next layer: Fastened to 1×4 Slats
next layer: which are fastened to 2×4 rafters
(planned) next…narrow end of another 2×4 fastened atop original 2×4…Allowing 7 inches.
This… in order to provide space for 1.5 in air channel gap ( up against metal underside) with a 3/4 in furring stip beneath…and more space for Rigid insulation.
I already have in my possession (donated free) XPS (2in & 1in) foam and PolyIso (foil faced) 1/2 in sheets. I understand that i dont need a vapor barrier…but it seems i have some materials that operate as vapor barriers ( PolyIso) and Vapor retarder (XPS).
What would be the best way to arrange these sheets, and not trap moisture w/in the small cathedral like ceiling insulation? And maybe help with thermal bridging if possible? Will i need to obtain different insulation? (By the way, the finished ceiling will be 6 inch tongue & grooved pine boards which i also received cheaply.)
(Uses of stucture: Involves high moisture activities, canning etc…and heated in winter, either electric, double split, or mr buddy propane. Stucture will have frequent use.)
So, essentially, can i make the system work with the materials i have? And if so, the best arrangement? Thanks much
Giovanni
GBA Detail Library
A collection of one thousand construction details organized by climate and house part
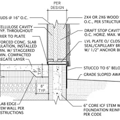
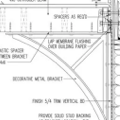
Replies
Hi Giovanni.
Just to be clear, there is no sheathing or roofing underlayment. Is that correct?
The 1x4s are run perpendicular to the rafters. Is that correct?
yup, that is the case. perpindicular.
I'm always reluctant to say to much about atypical buildings in design, construction, and use. But if you treat this like a vented, insulated cathedral ceiling, you could use some of the rigid foam to make vent baffles between the rafters, then fill the cavity with fibrous insulation for R-value, then use more rigid foam, continuous along the underside of the rafters to mitigate thermal bridging.
In this arrangement and your climate and given the high-humidity activities you plan to do in the workshop, I think you'd want to make the ventilation baffles from the most vapor-permeable material you can, maybe EPS foam, and use the more vapor-closed rigid foam for the continuous insulation. In this way, you'll have a warm-side vapor retarder and an assembly that dries to the outside.
You should do an impeccable job air sealing the interior side of the assembly. You can install the continuous rigid foam air tight with caulks, sealants, and tapes. If you don't install continuous interior rigid foam, install an airtight drywall ceiling before the tongue-and-groove ceiling (the paneling will not be air tight). And manage humidity with a dehumidifier or depressurize the building during these activities (you could simple put a box fan in a window blowing air out during canning, for example).
Again, because this is not a common situation, I'm not positive about this approach and hope that if any other GBAers have experience with a building/use like yours, they will chime in.
Brian,
thanx much for your insights, on helping me think through this. Totally understand your initial reluctantcy, but any and all insights will help me think through the various options.
Been a huge fan of the siga sicrall tape, and likely will use it for air sealing in this scenario.
Any more thoughts, confirmations, etc. would be great as ya'll have time. many thx
Giovanni
Btw, say i obtain the EPS board foam, to dry to the outside, is a thinner piece advisable, say a 1 in verses a 2 in of the EPS, (since the thickness can affect density, and thus permeability/or permeance...before i layer a fibrous insulation for example...)
Or in other words, put more simply...what proportion of the sandwiched layers ought be higher permeability to lowest permeabilty?..If i basically have 5 inches within the interior rafter cavity...after the air channel...say, maybe 2.0 inches of material with highest permeability facing outward, and the remainder 3.0 inches inward the least permeabilty Interior? or would something more like 1 to 4 inch ratio....work similarly?
( i do realize i am limited in making this a VERY cosy place, due to lower R-levels in gen). My idea is do my best to seal internally while preventing trapped moisture from foolish decisions on my part).
You are correct that the thicker the rigid foam the less permeable. In the case of the site-made ventilation baffles, use as thin of material as you can that won't deform. Seal it in place with caulk, sealant, canned spray foam, and/or tape. This way you will promote proper ventilation and maximize drying potential.
Of course you will cover the foam with something with a 1 hour fire rating as require by code? If for any reason there will be no inspection making you cover the foam, I say you would be crazy not to as the fire rating will give you the time needed to escape before the fumes from burning foam kill you.
Be sure find and read both of Martin’s articles on how to insulate a pole barn.
In my opinion every cent you saved and more by building a barn will be spent in a failed effort to make it be a high performance house.
Walta
Here is the article on how to insulate a Pole Barn: How to Insulate a Pole Barn
Brian, yup, had looked through some of those various barn articles. Good guidance. i suspect since my scenario had somewhat slightly different conditions, and materials i had that werent the ideal...( range in permeabilty..) specifically in 4a... i couldnt determine necessarily an ideal way to proceed. (I am a bit too detail oriented, but not necessarily a perfectionist). Different perspectives help.
Any more tips or suggestions from the Pro's?