Is Thoroseal good for the capillary break on footing?

I’m looking for something that can be applied to green concrete (7 days after pour ok) that would provide the capillary break on top of the footing before the foundation wall is poured. Is Super Thoroseal (or regular Thoroseal or Thoroseal foundation coating) going to work?
Thanks!
GBA Detail Library
A collection of one thousand construction details organized by climate and house part
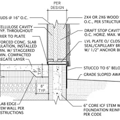
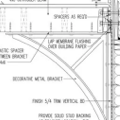
Replies
E.C.
Several people posting comments on the Web write that they have used Thoroseal for this purpose.
http://forums.finehomebuilding.com/breaktime/construction-techniques/footing-capillary-break
"My contractor... used Thoroseal, which was sprayed on the footer before the wall was poured."
http://www.nesea.org/uncategorized/using-insulating-concrete-forms-to-make-a-frost-protected-slab-foundation/
"I coated the top of my footing with “Thoroseal,” which acts as a capillary break and a vapor retarder."
You might want to contact Thoroseal, and ask the company for advice on this matter.
Thanks for the extra links, Thoroseal recommends any of those 3 for that purpose. Just curious if there was anything better suited, since I didn't see much mention of Thoroseal for that purpose from you/GBA or BSC. Open to other suggestions that don't require waiting 28 days.
E.C.,
Options include:
1. Asphalt-based dampproofing
2. Latex-based low-permeability paint (elastomeric paint) -- for example, UGL DryLock latex masonry paint
3. Delta Footing Barrier.
4. Cementitious coatings (cement-based waterproofing) -- I assume that Thoroseal is in this category.
Some builders have used 6-mil poly, although poly isn't easy to work with in this location.
More GBA links to threads on this topic:
https://www.greenbuildingadvisor.com/community/forum/green-building-techniques/36923/capillary-break-over-footing-vs-vapor-barrier-under-
https://www.greenbuildingadvisor.com/community/forum/green-building-techniques/36926/capillary-break-between-footing-and-foundation-wall-
I spoke with a technical representative at BASF who produces Thoroseal and was told that instead of using Thoroseal, they recommended Masterseal 500, as it was better suited for the application due to it being cementitious. I have been speaking with different contractors and waterproofing suppliers all day and have been getting conflicting answers as to the integrity of adhering concrete to anything other than concrete.
Here is the link to Masterseal 500.
http://www.construction.basf.us/products/view/family/masterseal-cementitious-waterproofing/product/masterseal-500
cementitious
Chris,
Here's what I found when I researched the issue:
"I also spoke with Jason Theis, a technical help representative at BASF, the manufacturer of Thoroseal. (BASF sells its Thoroseal product under two brand names. When sold at Home Depot and Lowes, the product is labeled “Thoroseal.” When sold directly to contractors, the product is known as “MasterSeal 581.” It’s the same stuff, regardless of the label. Super Thoroseal is Thoroseal with an acrylic additive mixed in.)
"On the first question, Theis advised, “Thoroseal should only be applied to fully cured concrete, not green concrete. You have to wait until the concrete reaches 80% of its design strength, which takes 28 days. If you apply it early, you might not get a good bond, and you might get cracking.”
"On the second question, Theis advised, “You need a two coat-application. Cure time will vary, but generally the cure time is 2 to 3 days.”"
For more information on this question -- and on other products used to provide a capillary break above footings -- see Capillary Breaks Above Footings.
Thank you Martin! I was not told that it needed that long to cure. I am considering my options right now, and since my footings were poured today (with walls to come in the next few days to week), it seems that I will have to go with another one of the options mentioned in your capillary break article.
I have been getting a lot of push back from local suppliers regarding the use of products such as asphalt dampening (they are all adamant that I need to have cement on cement for the wall the remain structurally adhered). Since I have a rebar to deal with every few feet, peal and stick options also seem to be off the table. It seems to me that Asphalt Damproofing is my best option at the moment due to time constraints, but I will admit I am nervous it could have long term problems. It amazes me how little I am getting for information on this from local contractors, for what seems to be a simple yet important step.
Chris,
It may be "a simple but yet important step", but I bet capillary breaks are used on far less than 1% of foundations. While I'm certainly not saying they aren't a good idea, foundations don't generally suffer significant problems from their absence, and whatever you choose will be a lot more effective than the nothing that usually occurs.
Chris,
I just went through this and here are my observations:
1) The determination of whether a concrete to concrete connection between footing and wall is required is a decision that should be made by a structural engineer. Lot's of people have opinions, but not everyone is qualified to make decisions.
2) Assuming your engineer gives you the green light, then you have 2 options at this point, 1) liquid applied or 2) do nothing
3) I too had a lot of rebar to deal with so I opted for a liquid applied membrane made by EPRO called Ecoline-R. It can be applied to green concrete, it can be brushed on or sprayed on and it cures quickly. It looks and smells a lot like acrylic driveway sealer.
4) Brushing a liquid applied membrane on to green concrete is a lot of work. Think painting drywall, but much rougher surface with larger pores to fill. The top of the footings are not so bad to deal with and I used a 3/8" nap roller as recommended by the manufacturer, but trying to fill in the key and the rebar holes was a PITA.
5) The roll out membranes are not recommended for use with rebar, but in hindsight I think it is very doable and easier. My mason had a "sophisticated' jig comprised of a 2x4 with nails protruding every 12" to make the key and mark the rebar locations. I don't see why the membrane could not be placed on the footing and then cut and marked with the jig. Even if the nails would not penetrate the membrane, then it could just be marked every 12", cut with a razor and then keyed into the footing with a 2x4.
6) The do nothing option depends on your site conditions and interior insulation plan. In my case, I have 2 different slab heights. The higher slab has a lot of sand is bone dry. The lower slab has clay and is wetter. With the pit open, I have to pump out water in the lower slab when it rains, but the higher slab remain bone dry. I am glad I have a capillary break on the footings in the lower slab, but probably did not need it on the higher slab. In addition, I am insulating the inside of the basement walls with EPS, so that provides a class III vapor retarder on the walls.
Hope this helps.