Is this wall/roof assembly going to have problems?

mikeysp
| Posted in General Questions on
Two young friends of mine are building a small 14’x28′ cottage house out of a fancy storage shed. I stopped by to see how they were doing, and I got a little concerned about their wall/ceiling assembly. I took a couple pictures and offer these details in hopes of someone allaying my concerns or offering some sound advice I am all too glad to pass along.
Zone 4a, Mixed Humid (Nashville, TN) Lot’s and lots of humidity.
ROOF ASSEMBLY:
Latex paint
Drywall
2″ Polyiso board between rafters (2×4-16″ O.C.)
1×4 purlins 24″ O.C.
White bubble wrap
Metal Roofing
Additional roof assembly notes:
“NO” Gap between 2″ polyiso and purlins.
“NO” Gap between 2″ polyiso and purlins.
“NO” roof sheathing
“NO” Eve vents
Only 48″ Ridge vents midway of the 28ft ridge
WALL ASSEMBLY:
Latex paint
Drywall
2″ Polyiso board between rafters (2×4-16″ O.C.)
White bubble wrap
Cedar Siding
minisplit heatpump
1 Bathroom
Two sleeping bays
Kitchen/living area
Shell was constructed on skids and it is sitting on leveled blocks.
My concerns:
1. Lack of air gap between rafter polyiso and purlins.
2. Eve vents – None.
3. Ridge vents – Only 4ft of the eve in center of the 28ft ridge.
4. few inch gap between the insulation where the rafters meet the ridge.
5. Wall assembly
6. Outside was very likely not air sealed, just layered bubble wrap with no tape.
7. They have hung several sheets of the drywall and did not air seal it.
Any advice to improve their final outcome or relieve my concerns would be welcome.
Thank you.
-Mike
GBA Detail Library
A collection of one thousand construction details organized by climate and house part
Search and download construction details
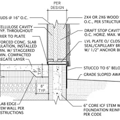
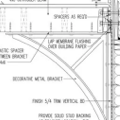
Replies
Hi Mike -
Hard to know where to start on this one but here is my shot:
1. Venting assemblies is a good thing, but continuous bulk water and air control layers are much more important; you can't vent your way out of wetting from liquid water leaks or condensation from air leakage.
2. Venting only works if there is air flow; air flow requires two holes and a driving force. Gable to gable venting give you two holes but little driving force. Soffit-to-ridge gives you two holes and a driving force (stack effect), at least SOME of the time.
HOW often you get soffit-to-ridge air flow is actually a great question, one I am working on right now: hoping to find the time to do "Wingnut" smoke stick air flow testing at soffit venting...stay tuned.
Mike,
Couple of issues from experience. They used paper faced polyiso insulation which, if the paper facing gets wet, it tends to bow. Since the roofing insulation is not attached to anything, any amount of water (could be condensation from night radiation or a small water leak) will cause it to taco and pull away from the purlins. No amount of spray foam will keep that air tight. They should consider putting in something bellow the insulation across the whole roof that can be sealed up properly (membrane, plywood, osb, drywall or layer of taped rigid insulation that is not paper faced)
Same issue with the wall except less of a air seal issue with decent drywall work.
The ridge vent is for venting the space between the insulation and roofing, it should not be a giant hole at the highest point from inside the house to outside. That just wastes a lot of energy from inside the building.
Mike,
There are lots of obvious problems here. The ridge vent shouldn't communicate with the interior conditioned air of the home, as it does in this case. The ridge vent should only communicate with the ventilation gap above the insulation. There needs to be an air barrier between this ventilation gap and the interior space.
It almost never makes sense to cut rigid foam into narrow strips and insert the strips between rafters. Instead, the rigid foam should be installed as a continuous layer.
The bubble wrap is a true vapor barrier, and compliant enough to slow the drying of the back side of the siding, making them more prone to seasonal cupping/splitting and rot. What is the intended purpose of that bubble wrap?
Also note, 2" polyiso and a layer of bubblewrap will woefully underperform R13-R15 batts (and no bubble wrap) in the walls. The high R/inch of the polyiso is being severely undercut by the much shorter thermal bridge through the framing. Blowing cellulose or fiberglass into the remaining 1.5" in the wall cavities would make it perform slightly better than a 2x4/R15 wall, but that would still underperform IRC's 2x6/R20 prescriptive minimum for zone 4A, and wouldn't come close to meeting code-min on a U-factor basis either. See:
https://www.greenbuildingadvisor.com/article/installing-closed-cell-spray-foam-between-studs-is-a-waste#comment-form
https://www.finehomebuilding.com/membership/pdf/184243/021269086NRGnerd.pdf
For the walls that don't already have the wallboard up, compressing split R13-R15 batts (nominally 1.75" thick) into the 1.5" deep cavity would be fine. hit code min performance on the walls would require adding Bonfiglioli strips or 1.5" wide strips of foam board (3/4" foam is enough) to the framing and correspondingly deeper cavity insulation:
https://www.finehomebuilding.com/membership/pdf/9750/021250059.pdf
Cutting 3/4" closed cell polyiso into 1.5" wide strips is pretty quick and easy using a steel wallboard taping knife that has been sharpened on the edges, and a straightedge:
https://www.finehomebuilding.com/2009/01/29/theres-a-better-way-cutting-rigid-insulation
With only 3/4" foam edge strips the wallboard can be long-nailed screwed to the framing. Compressing low density R11s into the 2.25" nominal cavity depth is pretty easy, performing at about R8 at that thickness. Kraft facers are fine (though there's nothing to really staple them to) or unfaced are fine, but avoid foil faced batts in this application.
Thank you gentlemen.
What is the minimum repairs you would recommend at this point?
Akos, they are going to have drywall walls and ceilings.
I have thought of a few solutions, but I am new to building science... a "white belt" in Building Science Kung Fu and have learned enough to get myself into trouble if I "invent" any solutions short of building the assembly exactly as it should have been done to begin with.
Is the only acceptable solution to pull it all apart?
Some speculative ideas that I have had:
1.
1. leave wall assembly as they have it.
2. Eliminate the gap at the ridge with a small piece of foam and have no vents.
3. Remove and reinstall the roof polyiso with a 1" min air gap between foam and purlins, add eve vents and additional ridge vents. Make sure there is a shared air space from gable-to-gable if there will not be a continuous ridgevent. The house is 392 SQ FT so it only needs about 1.5 sq ft of venting.
What think you?
Thanks.
-Mike
Mike,
I'm going to go by the assumption that the folks are looking for a simple/cheap way of turning the shed into a living space that is reasonably comfortable that won't be used all year.
I don't know enough about warm/humid climate issues to comment on mold problems (up here we deal mostly with icedams and soggy ceilings in the winter), would be good to get somebody local to give pointers on that.
For the roof, if you treat the roof the same as an un-vented assembly with exterior rigid foam (it looks that way if you squint a little bit), the two things that need to be addressed are:
-seal up the ridge vent
-decent air barrier under the foam
Adding in insulation under the rafters/foam would not hurt but not a must if it doesn't need code compliance. There are sometimes condensation issues down south with lighter metal roofing, it would be good to get a local's view that.
The walls are fine if they just drywalled. Adding more insulation into the cavity behind the foam doesn't hurt, but I doubt it would be worth the cost/work.
Best of luck.
If the bubble pack or siding isn't yet installed on the walls, adding 3/4" asphalted fiberboard sheathing on the exterior would provide a vapor-permeable moisture tolerant nailer for the siding, and would add another R2.5 or so to the whole-wall performance, which is almost enough to get it to thermal performance compliance. Blowing the remaining cavities behind the wallboard full of cellulose or fiberglass would get it closer still (maybe even all the way there, depending on the actual framing fraction.)
I don't see any cheap or easy way to compliance and resilience on the roof. Is the metal roofing already up?
Dana, this was a delivered storage shed. It arrived as a dried-in shell with siding, roof, door, windows, and white bubble wrap insulation.
Arrived with siding over bubble wrap on cross braced walls (no sheathing).
Metal roof sets directly on the bubble wrap which sets directly on the purlins.
The floor assembly is advantech on 2x6 floor joists on 4x6 treated skids with no insulation.
Whole structure setting on leveled concrete blocks every few feet.
I am hoping to give him a "passing solution", a "C" if you will. Anything short of an "F", big problems, mold, moisture problems. It is small, so the energy bill will probably not be too bad.
If the "ONLY" feasable solution to a "C" is too pull the building apart, I will let him know.
My plan is to print this exchange and hand it to him, so he can make an informed decision.
Thank you again. -Mike