Is this wall insulation idea ok for humid south?
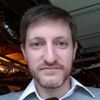
House: built 1892 in Birmingham, AL. Currently little to no insulation anywhere. Exterior studs are 3.5″. Original pine siding (pattern 117). 11.5′ ceilings. Daikin multi-split system (2 zones) on bottom floor.
We’ve started renovating a few rooms and my idea for the insulation is (from the inside, with walls fully opened up) cut foil faced 1/2″ polyiso to fit in stud cavities and caulk in place all the way around the stud bay, pushed firmly up against the back of the siding. Install (properly) R-13 paper faced fiberglass bats on top of that.
Do you think this is a good plan of action. Also, do you think I would have moisture problems in the sandwich space between the polyiso and the back of the siding during the humid summer? My guess is no, since the siding lap joints aren’t sealed well.
GBA Detail Library
A collection of one thousand construction details organized by climate and house part
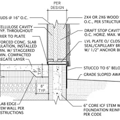
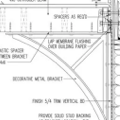
Replies
Hi Time is not money,
I like the sentiment behind your screen name. It would be nice to know your actual name too. It makes the forum a much friendlier place.
When houses don't have sheathing or a WRB, it is best to create an airspace between the siding and insulation. There are a number of ways to do that. I suggest you start with this article: Walls without Sheathing
What Brian said- it needs the air gap as a capillary break & drain space. A half-inch gap is plenty- even 1/4" is enough, but cutting 1" wide strips of half-inch polyiso along side each as spacers to keep the fuller-sheet away from the siding is easier that 1/4" spacers.
Cut the foam a 3/8-1/2" narrower than the cavity to make it an easy fit, and use a thin bead of polyurethane caulk to glue the sheets to the spacer strips, and seal any horizontal seams of the foil faced foam with a temperature rated HVAC tape. Then use can-foam to fill in the gaps along the edges to the studs as a more secure air seal.
Half-inch polyiso isn't always going to be rigid enough to provide enough resistance to compressed batts to keep it away from the siding mid-way between the studs, unless the cavity depth for the batt is 3.25" - 3.5". But the cavity from foam-to-wallboard should not be more than 3.5" or it won't fully fill the space. Using 3/4" or 1" for the cut'n'cobbled sheets might work better, depending on the full cavity depth. If the studs really are as stated only 3.5" (4.0" was more common in 1892), with a half-inch spacer and half-inch foam you'd be looking at only 2.5" of cavity, in which case a split high density R21 fiberglass 0r R23 rock wool or 3" sound-abatement batts would be more appropriate. With a bit of practice splitting a 5.5" nominal HD batt into two 2.5" + batts can work, but soundproofing batts (rock wool or fiberglass) would be less labor.
With foil faced foam on the exterior it's fine to use kraft faced batts with the facer next to the wallboard from a moisture control point of view, but the facers make it harder to inspect. Unfaced batts are preferable, and no interior side vapor retarder tighter than standard latex on wallboard would be needed on the interior.
While you have the wall opened up it's worth taking the time to paint the back side of the siding with latex primer paint. If it's left as bare wood the moisture cycling in the siding will cause the paint on the front side to fail, or even cause the siding to split, now that it no longer has a deep empty cavity to dry into. Even when back-primered a century's worth of exterior paint build up can still fail after insulating, but the risk is much lower, as is the risk of the siding boards curling or splitting.
Thanks for all the info guys. Very helpful.
Yes, the studs are 3.5" rough cut. I was surprised as well. Some studs are full 4" in another part of the house, so I'm assuming they just used whatever was available in the area at the time.
---
An aside:
Is it fair to say (generally speaking) that the lack of insulation in a house like this is a big factor in how it's been able to stand for so long with basically zero mold or water damage? Having no insulation may be detrimental to the comfort of the occupants, but it seems like a bonus when it comes to the health of the structure itself - allowing it to fully dry in both directions and not giving any condensation points.
To be clear, when I say "lack of insulation", what I mean is the lack of someone in the past just going in and stuffing the walls with batts, cellulose, foam without clearly mapping out how it would affect the structure. I see a lot of old houses in my area where cellulose was blown into the wall cavities years ago and I always imagine it's just a wet mess on the sill plate now and will lead to premature failure over just never insulating to begin with.
I do find it odd that you are proposing an exterior side vapor barrier and an interior side Class II/III vapor retarder in a climate that requires neither.
Air sealing is critical - use a blower door (or equivalent) to verify air sealing. Consider two air barriers.
I was basing this design on the LSU university wall construction advice for hot-humid and mixed zones: https://www.lsuagcenter.com/topics/family_home/home/design_construction/construction/foundation%20floors%20roof%20walls/exterior%20walls%20roof/walls%20wall%20covering/ideal-wall-assemblies-for-hothumid-and-mixedhumid-climates
I think we are classified as mixed climate. I may have easily misunderstood something in their design though.
I liked the kraft paper for making sure the batts don't sag over time. It's more of an installation helper than anything else. Given that, would it suffice to make a long vertical cut down the face of the kraft paper with a razor knife to open that up and increase flow once installed?
I believe your are close to the hot/humid border, so I'd be conservative and pick a wall design that works well in both areas.
Consider EPS and no kraft paper and see how this compares to some other sources. You could use a mesh rain-screen product to maintain a ventilation gap between foam and siding.
Consider Rockwool batts? Easier to install well, since they give a friction fit. Still end up with itchy bits, but for me not nearly as bad as fiberglass.
Anyone thoughts on whether using Intello as an internal air barrier (with full 3.5 inch batts behind it) might be easier than cut-n-cobble? I checked the "no sheathing" article but I'm wondering whether one needs the air gap if using Rockwool? Wouldn't that be very similar to using a mesh rain-screen product?
I'm in a similar boat (climate zone 2, no sheathing in an 1895 house) and face the same dilemma. I'm curious whether you have contemplated pulling the clapboards, and insulating and sheathing from the outside? I don't have any numbers to back this up, but at some point (interior trim vs exterior, two stories vs one, etc) wouldn't that be cheaper? If it's a DIY project, then I totally understand working from the inside, room by room. I'm actually holding off insulating the walls in a similar fashion until I can come in from the outside - the lack of a proper WRB has always bugged me.
"I'm curious whether you have contemplated pulling the clapboards, and insulating and sheathing from the outside?"
The expense would be way out of whack for our situation. The siding on our house is in good shape for it's age, but brittle. So, there would be no way to remove it without damaging a large percentage of it and having to replace it with new. Pattern#117 siding is pretty expensive per board foot. It would be at least 3 times the cost of doing from the inside where drywall and trim is cheap.