Is this wall assembly safe?

Hello,
In the midst of an exterior renovation on Long Island, NY, climate zone 4a. Current wall assembly is .5” drywall, 2×4 stud wall with kraft-faced fiberglass, fiberboard “nailbase,” Tar paper, and cedar shingles. The planned assembly is .5” drywall (existing), mineral wool batts, .5” plywood sheathing, Henry Blueskin, .75” Dow Thermax, .25” rain screen and LP Smartside.
Does this sound safe? My contractor wants to leave the existing fiberglass due to the built-in vapor retarder. I think that as long as the drywall penetrations are sealed, the benefits of mineral wool outweigh any benefit to the kraft-facing and that given the presence of a vapor-impermeable material outside of the sheathing, maximizing inward drying potential is more important than minimizing outward vapor diffusion.
Thanks!
GBA Detail Library
A collection of one thousand construction details organized by climate and house part
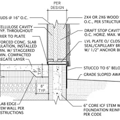
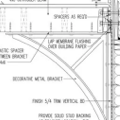
Replies
Here is good vapor barrier advice. Also, don't add vapor barriers (like Thermax) where they aren't required. Always air seal well with blower door verification/fixes.
https://www.buildingscience.com/documents/digests/bsd-106-understanding-vapor-barriers
My guess is in terms of dollars and cents, you will never save enough energy with rock wool over the current fiberglass to pay for the labor and materials to remove and install the rock wool.
If the fiberglass and fiberboard are still in good condition I see no reason to remove them.
I seem to recall that in zone 4 any combination of interior and exterior insulation is safe. It is just not cold enough for long enough to be a problem.
Walta
Cody,
I'm with Walta.
Assuming R11 batts in the existing walls, keeping the fiberboard and just add in the exterior insulation brings up your whole wall R value to around R18.5.
Replacing the batts with mineral wool and the fiberboard with plywood, you end up with R19. That is a lot of extra work for not much gain.
I feel the full peel and stick installation is a bit overkill. Taping the seams of foam would be much simpler and cheaper.
Thanks for the replies. Unfortunately the fiberboard is quite deteriorated in large sections and the let-in bracing is inadequate, so it’s definitely being replaced with plywood sheathing. I’m going with the peel-and-stick membrane as I can only get one layer of foamboard, and am uncomfortable relying on it for an air-barrier due to shrinkage concerns. The seams will be taped as well.
If the Kraft-facing on the fiberglass isn’t of concern, it certainly would be easier to leave it (perhaps just peeling back enough to air-seal penetrations).
Hi Cody,
Your proposed wall assembly is safe. All you need is a class three vapor retarder, basically painted drywall. Vapor diffusion is much less of a concern than air leakage. With the fully-adhered WRB, you'll have an excellent exterior air barrier, you'll also want to do a good job detailing the drywall as an interior air barrier. And don't forget about all of the penetrations in the walls and the plates. Air sealing in this way will be your best return on investment.
No practical difference, but In Zone 4A you don't need any vapor retarder at all.
Thanks for the help!