Is this a good plan for updating our wall layers?

This site has been a HUGE help with putting together our plan for updating our 1986 built home while replacing the roof and siding due to a hail damage claim. We live in Columbus, Ohio (zone 5). We have a gas furnace. Thank you!
Our recently updated plan is described below. We plan to have the install done within the next week or two.
Questions:
1. Should I be concerned about having multiple vapor barriers on the interior with the addition of foam on the exterior? I’ve read your articles which express concerns about that because of the need to dry to the interior.
2. Can you look over the layers and see if you spot any other issues?
- Existing wall layers (built 1986): Here is a grainy copy of the original wall sections. From the inside, out: existing drywall, plastic vapor barrier, 2×4’s with fiberglass batt insulation, 1/2″ Owens Corning “rigid polyisocyanurate foil faced foam board” with R3.6, aluminum siding (which we will remove).
- Exterior layer 1: 3/8″ Thermal 3Ht*, ~R1.5, applied over existing rigid foam insulation to provide sealing of all exterior walls and gaps. Seams joined by manufacturer recommended tape.
- Exterior layer 2: Tyvek*, water barrier. Seams joined by manufacturer recommended tape.
Exterior layer 3: Cedarmax insulated vinyl siding by Provia*, – R:2.4, thickness: .050, 6″ double. Color: Pueblo, Aluminum trim pieces will be custom bent to fit the 2×3″ trim boards around the windows, corners, etc.
GBA Detail Library
A collection of one thousand construction details organized by climate and house part
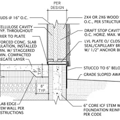
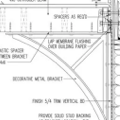
Replies
FYI:
- the Thermal 3HT has foil on both sides. I know the foil is unnecessary but our contractor said he can add that at no additional charge because he is a dealer. We could use Dow Styrofoam (no barrier) instead but it would cost us around $600-800 more. Specs: http://www.thermalbuildingconcepts.com/technical/propertySheet/ps-PhysicalPropertiesofThermal3Ht.pdf
- We are using Tyvek and foam backed siding because they are covered with the insurance claim.
Chad,
To translate for other readers, the Thermal 3HT is foil-faced EPS.
You have a (barely) adequate amount of exterior rigid foam for your 2x4 wall in Climate Zone 5.
Feedback:
1. Don't use insulated vinyl siding, since this type of siding doesn't drain as well or dry out as fast as ordinary vinyl siding. (One of the best features of ordinary vinyl siding is the built-in air gap -- something that you lose if you choose insulated vinyl siding with its integral rigid foam.)
2. The multiple vapor barriers on the exterior of the wall aren't a problem, as long as these vapor barriers are associated with rigid foam of an adequate thickness (as they are in your case). However, the interior polyethylene isn't ideal.
3. I will cut and paste my standard answer to the frequently asked question, "What about the interior polyethylene? Isn't that a problem if I install exterior rigid foam?" Here's the answer:
Many energy experts worry that it may not be a good idea to install exterior foam on a house with interior polyethylene. Although it would be better if the poly weren't there, the fact is that tens of thousands of Canadian homes with interior poly have been retrofitted with exterior rigid foam, and there haven't been any reports of widespread problems. According to building scientist John Straube, all indications show that these retrofits are "not so risky as most people think. These homes will probably be fine."
That said, the installation of exterior foam is not advised on any home that has suffered wet-wall problems like leaking windows, condensation in stud cavities, or mold. If you plan to install exterior foam during a siding replacement job, keep an eye out for any signs of moisture problems when stripping the old siding from the walls. Investigate any water stains on housewrap or sheathing to determine whether the existing flashing was adequate.
If there is any sheathing rot, determine the cause -- the most common cause is a flashing problem, but condensation of interior moisture is not impossible -- and correct the problem if possible. If you are unsure of the source of the moisture, hire a home performance contractor to help you solve the mystery.
If your sheathing is dry and sound, I don't think you need to worry about adding exterior foam. Adding a rainscreen gap will certainly go a long way toward avoiding future moisture problems. Of course, it's important to be meticulous with your details when you are installing your new WRB and window flashing. It's also important to keep your interior relative humidity within reasonable levels during the winter. Never use a humidifier.
To summarize, here are four caveats:
1. Be sure that your foam is thick enough to keep the wall sheathing above the dew point in winter. Read more on this topic here: Calculating the Minimum Thickness of Rigid Foam Sheathing.
2. When the siding is being removed, inspect the existing sheathing carefully for any signs of water intrusion, and correct any flashing or housewrap problems.
3. Install rainscreen strapping so that there is a ventilated gap between the new exterior foam and the siding.
4. Keep your interior humidity under control during the winter; if the interior humidity gets too high, operate your ventilation fan more frequently.
Martin, thank you again. This is very helpful. I plan to do most of what you explained. A couple of follow-ups...
A. "Don't use insulated vinyl siding" - Your advice makes great sense. We were leaning toward the insulated siding because we like the look, added noise reduction (we live near a busy street), and it is it costs us nothing extra (with our insurance claim). Do you feel the drainage concerns should still trump all of those pros?
B. If we use regular siding, does 1'' Thermal 3HT sound like a good idea? They told us 1" is the max width foam they can do with the type of aluminum trim/j-channel they use.
C. "Install rainscreen strapping so that there is a ventilated gap between the new exterior foam and the siding". I would love to add strapping/furring strips under the siding but our installer said that would cost an additional $2000 (out of our budget). I may try to do it myself -- do you have an article on installing furring? Plus, I think we may run into the maximum wall depth issue with that as well. If I have to pick between more rigid foam and the ventilated gap, which is better?
Thanks again!
Chad
Chad,
If this were my house, I would choose regular vinyl siding, not insulated vinyl siding, for the reasons I provided (drainage and fast drying).
If you take my advice and use regular vinyl siding, you'll save the $2,000 cost of the furring strips. Vinyl siding is naturally well ventilated and doesn't need furring strips.
You can use 1-inch-thick foil-faced EPS if you want. It's a good choice. Several other types of rigid foam would also work, but the EPS is environmentally friendly, so go ahead and use it.