Is this a good exterior wall design for climate zone 5?

I’m building a house and want very energy efficient, durable (100 yr), efficient to build and not outrageously expensive. I’m willing to pay up for an insulation system, but am not convinced that very high R values are economically justified in the way that good design and better materials are. So I have been debating a conventional frame 2×6 24″oc, sheathing, 1.5″ cc spray-foam outside and over rim joist, 3″ foam inside stud bays and rim joists, and rest of stud bay left empty. Seems this would give good insulation, eliminate bridging, compensate for fine flashing mistakes, eliminate condensation and vapor driven issues and not require design changes outside the norm of our local builders knowledge. 1. is this sound? 2. how durable is spray foam? relative to foam board? exterior applications? 3. if real R value diminishes quickly with additional inches of insulation, is leaving the rest of the stud bay empty better for durability? 4. are there siding attachment issues thru spray foam?
Thanks,
Kirk
Upstate NY
GBA Detail Library
A collection of one thousand construction details organized by climate and house part
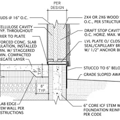
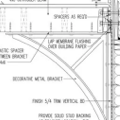
Replies
Kirk,
It's better to install your closed-cell spray polyurethane foam on just one side of the sheathing, not both. After all, you want the sheathing to be able to dry if it ever gets wet.
I think it's better to put the foam on the outside of the sheathing rather than on the inside. That way you address thermal bridging and rim joists.
You can use spray foam if you want, but most builders prefer to use rigid foam, because it provides a planar surface. Sprayed foam has a bumpy surface.
Put as much foam as you can afford on the outside of your sheathing. Then, if your wall R-value isn't as high as you would like, fill your stud bays with dense-packed cellulose (if you want). The cellulose is optional. If your exterior foam is thick enough, the cellulose can be omitted. (That's the PERSIST system.)
Then you need to do a cost-benefit analysis, including projecting future energy costs.
Good? It would provide a whole wall R-value of about 23.5, barely more than code minimum. And it would control moisture migration only if the foam never shrinks or separates from the framing and sheathing and if the sheathing never got wet during that 100 year life of the house.
If by "sheathing" you mean OSB, then you're creating a potential rot nightmare.
1. is this sound?
No.
2. how durable is spray foam? relative to foam board? exterior applications?
That's largely an unknown. But two-part petrochemical foams require a precise mix ratio and precise temperature control which is not practical in the field. Manufactured rigid foam board can be produced under controlled conditions.
3. if real R value diminishes quickly with additional inches of insulation, is leaving the rest of the stud bay empty better for durability?
Real R-value increases proportionally to the thickness of the installed insulation. The argument for "diminishing returns" is a logically fallacious one that the spray foam industry uses to sell limited thicknesses (often less than code minimum) of an overly expensive product.
4. are there siding attachment issues thru spray foam?
Yes, as there are through any exterior foam but moreso.
There are quite a few discussions on this website comparing the value of high-performance mechanicals vs. a better thermal enclosure. There is a general agreement that better insulation is more useful, because it can be inherently low-tech and low in embodied energy / global warming potential, requires basically no maintenance for the life of the building and enables survivable conditions in your home even with no power. It becomes cost effective when a high performance enclosure allows downsizing the mechanical system.
Closed cell SPF insulation doesn't qualify as low-tech or low embodied energy / GWP, and may have issues with usable longevity based on shrinkage, UV degradation and the possibility of being removed to address air quality problems.
Thanks guys! Martin, my thought on using it on both sides was that with the continuous coverage of the spray foam the sheathing couldn't get wet (thus my questions about durability), and though I have read about the PERSIST method I thought limiting whatever outinsulation to 1.5" eliminated any adaption/implementation issues our local builders/code might have with a system they're not used to (we are not exactly on the cutting edge here). Robert&Tom, I completely agree with the insulation and life of building idea and I know the R value is just over code min, but I am having a hard time coming up with any cost benefit analysis that justifies very high insulation levels more than that with good air sealing cause I will still need a heating system for code. No, I didn't mean OSB anyway. Plywood or 1" diagonal lap. I guess I am also trying to see this holistically. I am willing to use foam if it is durable and lasts the life of the building as long as it is the best product. I would of course have mechanical venitlation. Seems the consensus is I do use foam, foam board is better all around choice...???
Kirk
Kirk,
It is dangerous to assume that sheathing will never get wet. Flashing can fail, spray foam can shrink, and installers can make mistakes. Any sheathing should be able to dry in at least one direction.
For new construction, as I said before, I definitely think it makes more sense to use rigid foam rather than spray foam on the exterior of wall sheathing.
You didn't mention it, but it is certainly possible to build a foam-free wall. The current favorite seems to be a double 2x4 wall, up to 12 inches total thickness, filled with dense-packed cellulose.
Kirk,
Air sealing is a given in any new construction for a durable and efficient structure. That's not an option.
So the option becomes: how much to exceed the code minimum R-values (and how much can the required mechanical systems be downsized with increased envelope insulation, making them initially less costly and less costly to operate).
The purpose of all codes is to establish MINIMUM acceptable values. As a veteran poster on another expert builder's forum used to say in his signature line: "Congratulations, you've met code. You've earned a D-".
The cost-benefit analysis is really quite simple. It costs about 5%-6% more than conventional (code minimum) construction to upgrade to an Energy Star 5+ or even to a super-insulated house. If you calculate the additional monthly mortgage cost of that 5% and deduct the monthly energy savings, you're ahead the very first and every other month of occupancy.
As for the durability of foam insulation - all plastics have a limited shelf life, in terms of original specs. They may last forever in the landfill or out in the Great Pacific Garbage Dump, but they will lose their plasticizers over time, shrink, become brittle and degrade their thermal properties. And in a fire they are a disaster.
Martin, that certainly makes sense. That's what I was trying to avoid. Yes Robert the mortgage analysis does make sense too. And so does all the advice. I guess I have been over thinking this...which seems easy to do because there is sooo many new products and everything else out there, and I'm trying to make a smart choice. I will look into the double wall system that you and Martin recommended. Thanks again
If I went with a double wall, adding 1.5" XPS on exterior of weather barrier help lower risk of condensation? Or am I creating more problems?
Kirk,
Yes, there are far too many "new" building products which are over-hyped, over-marketed, and over-used.
A good example is the plywood, and now much worse OSB, sheathing that is more vulnerable to moisture accumulation and less breatheable than sawn board sheathing so that it accumulates more moisture. This now requires a good WRB on the exterior and perhaps additional outsulation to reduce condensation potential on the inside of these more vulnerable materials.
And, while the outsulation is intended to minimize condensation and hence moisture problems at the sheathing plane, it also slows or prevents drying to the outside and keeps the sheathing warm enough to mold and rot year round. Unintended Consequences - the foundational law of technological "solutions".
Going back to basics, the materials and systems which worked for hundreds of years, avoid many of these conundrums. Diagonal board sheathing (or horizontal with let-in metal T-bracing) offers good shear resistance and allow a breatheable exterior skin that is not vulnerable to normal moisture loads. Then #15 felt is more than adequate a weather barrier and no outsulation is necessary to correct a problem created by a common but less durable and less breatheable sheathing.
KISS. Keep it simple and sound.
Great. Thanks