Is this a feasible basement retrofit detail?

I’m puzzling over how to maintain a continuous air barrier at the 1F/basement transition on an energy retrofit and I’m curious what folks think of this potential detail.
Project specifics:
– This is a retrofit on a 1912 house with minimal insulation and no real air barrier
– Site conditions make it nearly impossible to trench the outside of the basement walls
– Stick-framed walls are being re-sheathed, air-sealed, and insulated as part of this project
– The site has a substantial slope, allowing french drain to be daylighted
– The existing slab is heavily sloped and the ceiling heights are low. We’re planning to remove the slab and extend the foundation downward.
– We’re pushing for some level of Living Building Challenge certification, so we’re avoiding spray foam wherever possible.
Since the site doesn’t allow for the installation of a drainage plane on the outside of the foundation wall, I’m going with the “drop a bathtub inside the existing space” approach to keeping the basement dry. It seems like the trickiest part is connecting the drainage plane’s air barrier through to the new air barrier that’s going on the sheathing. By my understanding, losing continuity at the top of the dimple mat would have two major undesirable effects:
– The french drain and radon vent pipes become pathways for conditioned air to escape, reducing energy performance
– Humid air would rise between the basement wall and dimple mat into the rim joist cavities, potentially causing a rot problem
Is it too cute to roll poly back over the dimple mat and flash it to the sill plate?
Is there some simpler non-spray-foam solution to establish air barrier continuity at the top of the dimple mat?
If the dimple mat is replaced by moisture-resilient insulation and the poly is run all the way up to the top, is the 3-1/2″ surface on top of the foundation wall actually large enough to securely adhere the poly?
GBA Detail Library
A collection of one thousand construction details organized by climate and house part
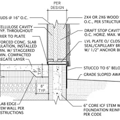
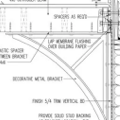
Replies
manbeardo,
Unfortunately all the options that don't use foam require exterior insulation, which you are not going to have access to install. Permeable insulation allows warm moist air to reach the cold concrete foundation walls and condense. Martin explains what at play in these articles:
https://www.greenbuildingadvisor.com/article/how-to-insulate-a-basement-wall
https://www.greenbuildingadvisor.com/article/three-ways-to-insulate-a-basement-wall
Wouldn't that issue be solved by sandwiching the poly between a moisture-resilient insulation on the inner face of the foundation and insulation in the stud bays? That assembly would basically be a sheathing-free "perfect wall" that's nested inside the basement's footprint.
manbeardo,
No. The reasons you don't see it being done or recommended, are in the first link I posted, and this one from BSC: https://buildingscience.com/sites/default/files/migrate/pdf/BA-0202_Basement_Insulation.pdf
As far as I can tell, my updated (attached) assembly is roughly equivalent to a combination of the assemblies in figures 14 and 15 of that paper. The key differences are:
- Using poly to create the air barrier instead of taped XPS panels
- Going slabless with a raft subfloor
- A more complicated transition at the sill plate because there's no existing seal there
manbeardo,
Your assembly is much closer to figures 4, 5, 6, 7, and 8. Permeable insulation with an interior air-barrier is not the same thing as a layer of foam. That's why building codes don't allow the two to be used interchangeably in roofs or walls.
There is no rule against not accepting advice. I'm just pointing out there is no support for what you are suggesting.
What behavior does taped XPS provide that this doesn't?
Taped XPS behaves as a mid-wall air barrier that's thermally insulated from the cold foundation wall.
In this assembly, everything between the foundation wall and the poly is moisture resilient and free draining. The interior face of the poly is kept warm so as to not be a condensing surface.
manbeardo,
It has permeable insulation that can accumulate a lot of moist air when it moves though the the air-barrier. That void or cavity doesn't exist with foam.
It is much the same situation as you find in roofs, and why codes don't allow them to be built with permeable insulation simply because there is an interior air-barrier in place, unless they have some way to exhaust that accumulated moisture (venting).
We do not build completely air or vapour tight assemblies. What we consider a tight house is 1 ACH50. That is a house which is exchanging the whole of the air inside it every hour. If interior air-barriers could save these basement walls, there would have been no problems with them, and no reason to recommend foam.
I'm as a bit of a loss to know how to continue this discussion, and am going to bow out.
Good luck with your renovation.
Well, you certainly have the Challenge part of LBC!
I generally agree with Malcolm.
Couple of questions.
Why is exterior excavation "nearly" impossible?
Is foundation concrete or concrete block or something else?
The foundation wall is 4 feet away from the neighboring lot's retaining wall. The shoring required to keep that retaining wall supported while trenching would interfere with the application of any products to the exterior of the foundation wall.
I have some experience with this. In my case generally flat lots, full clay. Yes engineered shoring required within 4 feet of property line. Certainly adds to the cost. Maybe more in your case but there is always an engineer that can do it!
Is that cost close to your proposed digging under footings from the interior?
edit:
We did an excavation for infill where the engineer came back with excavate to neighbour's foundation and pay for complete foundation wall with new footings. Was cheaper than shoring.
It's a 4000sqft (0.09 acre) lot with an 11.8% grade. The soil on the neighbor's side of that retaining wall is higher than the top of the foundation. When you dig down to the footing of the retaining wall, it's closer to 3-1/2 feet from the foundation wall.