Is there a way to move forward without removing the exterior 1″ XPS rigid foam, Tyvek, and windows?

Last February I started the project of adding an entire second story to our 1946 1,550 sq. ft. ranch home in Southern Wisconsin. It is on the border of WI and IL. It could be considered in the northern part of climate zone 5A or southern part of zone 6A.
I wanted to make the most energy efficient home I could afford. After the house was gutted inside and out, and roof and ceiling joist were removed, I added a foot to all the walls to keep the second story duct work inside the envelope of the house and hide it in soffit. A second furnace was added on the first floor for the second story duct work. When it came time to build the second story walls, I hired a framing crew to complete the second story walls and dry the house in.
The first floor is constructed primarily with original 2×4 wall studs and some 2×6. The second story addition is all 2×6. 7/16 OSB sheathing, 1″ XPS rigid foam, and Tyvek house wrap were applied to the entire house in that order, mostly while the walls were laying down. The windows were installed after that. The XPS, Tyvek, and windows were all poorly installed. Lots of gaps in the seams of the foam and not taped. When I questioned the framer/owner he got angry and quit with 2/3 of the agreed amount of money already paid.
I will be using LP Smartside strand lap board siding, and considering Cor-a-vent rain screen or wood firring strips as a rain screen? Some full thickness stone on the front side.
I thought the 1″ XPS was a good idea at first to insulate the 2X framing studs and rim joists, but after reading Mr. Martin Holladay’s articles and many others I am deeply concerned, to the point of loss of sleep, about moisture problems within the wall cavity on the OSB. I have fear that the XPS is not thick enough for my climate zone and concern with the dew point. I thought that I would be able to use close cell spray foam to insulate the inner wall cavities and air seal gaps from inside, but close cell is a vapor barrier. Possibly faced or unfaced fiberglass instead without poly plastic vapor barrier? I’m unsure about air sealing now if I’m unable to use close cell spray foam? Plaster will be the new wall covering.
Is there a way to move forward from the inside, with piece of mind, without removing the 1″ XPS foam or adding more foam to the outside? Either adding or taking away foam is going to make me remove and reinstall all 25+ windows on the two story structure. Time is critical for me because I have to paint the siding after installing it and fall is here. Do you think the 1″ XPS is adequate for my zone as it is considered a semi permeable vapor retarder not barrier with a perm of almost 1?Do you think that the house could breathe to the outside with the low perm rating and poor installation of gaps and untapped seams of the XPS? Or am I way off on that? I know responses are just advice and I will appreciate what you offer. Thank you.
GBA Detail Library
A collection of one thousand construction details organized by climate and house part
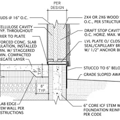
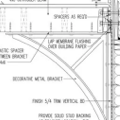
Replies
Steven,
You are going to have to do at least some exterior work to address the issues you listed ("The XPS, Tyvek, and windows were all poorly installed. Lots of gaps in the seams of the foam and not taped.") It is essential that your water-resistive barrier (WRB) be installed properly to manage wind-driven rain. If there are lots of gaps in the rigid foam seams, it's probably worth addressing that problem now, before the siding goes up.
When you write that the "windows were all poorly installed," we don't know what that means. You need to be sure that the rough openings were properly flashed before the windows were installed. Was that done?
If indeed the "windows were all poorly installed," that fact alone may dictate removing and reinstalling the windows. It all depends on what "poorly installed" means.
If you install a couple of inches of closed-cell spray foam from the interior, your sheathing will be enclosed in a foam sandwich. Although that's not ideal, it may be the best way to go. (If the sheathing is dry on the day that the spray foam is installed, the sheathing will probably be OK.)
But you can't install closed-cell spray foam on the interior side of your wall sheathing until you are confident that the water-management details are done properly. That means that you need to have a well-installed WRB and properly flashed windows before you can sleep well at night.
If you limit the interior side closed cell foam to 1" it won't be a vapor barrier and it's safe to fill the rest of the cavity with fiber insulation. when combined with the R-value of the exterior XPS there is sufficient dew point control at the foam/fiber boundary even without an interior side vapor retarder.
In zone 6 as long as about ~1/3 of the total center-cavity R is on the exterior of the fiber you're good-to go. In zone 5 it only takes 25%. So assuming zone 6, 1" XPS (R5), and 1" ccSPF (R6) you're up to R11, which would be sufficient to have R30+ total, or something like R19-R20 in the cavity.
With only 4.5" of remaining space in the 2x6 stud cavity you could hit R19-ish with compressed rock wool batts or with 1.8 lbs dense-packed fiberglass the fiberglass. With dense-packed or damp sprayed cellulose it would be no more than R17, which would have signficicant dew point margin.
At 1" most ccSPF is about 0.8-1.2 perms, which is almost a class-II vapor retarder. With R5 the exterior of the sheathing and ~1 perm vapor retardency toward the interior there is very little winter moisture accumulation in the OSB from interior vapor drives, but it can still dry toward the interior. If you bumped it to 2" you'd have huge dew point margin at the foam/fiber boundary, but very limited drying capacity for the sheathing. If you're concerned that ~1 perm vapor retardency would be cutting it too close (it isn't, IMHO), installing a smart vapor retarder such as Certainteed MemBrain or Intello Plus under the interior side wallboard, detailed as an air-barrier would give you much reduced wintertime vapor diffusion without limiting the drying rate of the sheathing toward the interior during the warmer ~8 months of the year.
I share Martin's concern about the window & housewrap installation. If the window flashing is not properly lapped with the housewrap it's a MUCH bigger problem (100x) than mere vapor diffusion/dew-point issues.
MemBrain or Intello might be worth the investment to ensure you sleep well even if it's not necessary for preventing condensation.
Even though the foam sandwiching the OSB is fine from a vapor diffusion/condensation point of view, it won't work well if liquid water gets into the OSB from poorly done flashing. Maybe post some pictures of what you think is not done well there?
Some factors that might shift the balance one way or another:
1) If you've got big roof overhangs, that makes good flashing slightly less important, especially on windows right under the overhang. Not a substitute for doing flashing right as wind and rain tend to coincide, but a factor to consider if you are on the fence about redoing the windows.
2) Your interior humidity will affect the potential condensation issues. An HRV in the winter can help keep the humidity low. If you are planning on that, you've got some extra insurance built in.
If you do take out the windows, you could consider putting another 1" of foam on the outside; that would be cheaper than 1" ccSPF on the inside in materials cost, but more expensive in labor at this point. It would also be better for the planet if you use EPS, but that's presumably low on your priority list given the bind you are in.
Gentlemen,
Thank you for your responses. I will be more descriptive in the details ("The XPS, Tyvek, and windows were all poorly installed.)
Foam was not staggered or offset to osb when applied over osb. Many foam and osb seams align. Day light can be seen in spots from inside house. No tape was applied to foam. At outside corners, foam doesn't always make it to the corner and without the wrb the osb would be exposed. Fair amount of gaps and cracks in foam placement throughout.
WRB application. WRB is not lapped at any of the inside corners so foam is exposed. WRB is not lapped at some of the outside corners either. It just ends at the corners from both directions and osb and foam are exposed. At windows and doors wrb was not folded in on rough opening sides or lapped over top of window or door flashings.
Door and window installation.1. Tyvek was cut out in the rectangle shape of door or window. 2. window or door was placed in, leveled, plumed, and nailed in nail flange. 3. Vycor flashing tape was placed around door or window in shingle fashion covering nail flange and tyvek. Done. There is no sill flashing applied in rough opening. There are no shims on the bottoms or sides of doors or windows.
I know that I was going to have to do some fixing to the wrb and tops of window and door flashings. I just don't know to what extent each has to be done.If I wanted to fix the foam gaps, I would have to remove and replace the wrb. If I wanted to flash and shim the window sill rough openings, the flashing tape has to come off and windows pulled out. I had window Rep. come out. He agreed they are not installed correct, buts said if they were his windows, he would not remove them for sill flashing and shims as long as they were plumb and square, which they are. Rather he would rework the wrb to overlap the top of the window flashings. If I pull the windows to fix the flashing and shims, and pull the wrb to tape and caulk the foam, I might just pull the foam, because of the risk that according to an IRC chart it isn't thick enough . Climate Zone Minimum R-Value of Foam Sheathing
Marine Zone 4 R-2.5 for 2x4 walls; R-3.75 for 2x6 walls
Zone 5 R-5 for 2x4 walls; R-7.5 for 2x6 walls
Zone 6 R-7.5 for 2x4 walls; R-11.25 for 2x6 walls
Zones 7 and 8 R-10 for 2x4 walls; R-15 for 2x6 walls.
The over hangs are 18".. I can't buy any more rigid foam. I f I pullthe windows, I'm pretty sure I will pull the foam off, and just install new wrb, rain screen, and reinstall windows, fiberglass batt the cavities, spray foam the small cavities and gaps,with poly plastic vapor barrier, with plaster. Not the senario I wanted, but its whats normal and not risky for here I believe. I don't know if I like the idea of sandwiching the osb. Comments or suggestions please,
Steven,
You have a mess on your hands. It's hard to give you good advice without a site visit.
If you pull the foam and go with a batt-job, caulk the OSB to the framing inside EVERY cavity with the appropriate products (there are several application specific caulks for this now, ProPink, etc.), and tape every horizontal seam with the appropriate tape. Using R23 rock wool has better fire resistance than R21 fiberglass, and isn't usually dramatically more expensive. (DON'T use low density R19s!).
Rather than polyethylene sheeting, install a smart vapor retarder on the interior as an air barrier. ( MemBrain is only ~2x as expensive as 6-mil poly.)
Rather than dropping the foam in the dumpster it makes sense to re-install the 1" XPS on the interior side, cap-nailing & gluing it to the studs with a bead of foam-board construction adhesive for air tightness, taping the seams with an appropriate tape. Tape the bottom of the XPS to the subfloor, since that's a more-likely joint to leak over the long term. Installing wallboard over 1" foam with longer screws isn't very difficult, but it gets more awkward the thicker you go. If you do a perfect job of air-sealing the XPS, it's ~1-1.5perm vapor retardency is a sufficient vapor retarder, but using MemBrain as an air barrier is probably more reliable. A key detail to get right is air-sealing the electrical & plumbing penetrations of the sheet goods.
I like Dana's idea of moving the foam to the inside.