Is there a maximum thickness for exterior rigid foam?

Hi all,
As a general question, I was wondering if there is a maximum advisable thickness one can reasonably expect from (multiple layers of) exterior rigid foam, assuming the use of furring strips. Reading through the REMOTE manual, it explicitly mentions that layers of “4 inches, 6 inches, or greater” can be used, and the structural screws they recommend for attaching the furring strips are available in lengths well beyond that. That being said, I haven’t had any luck finding someone who has installed more than 6 inches of exterior foam (probably for good reason, but still). I imagine one might have to find an engineer to approve a fastener schedule or something, but as far as I can tell there are no other concerns that would limit the foam thickness. I seem to recall someone (Joe Lstiburek?) remarking that furring strips over foam could hold up a car.
As for a more specific case, I was absent-mindedly entertaining the idea of a cathedral ceiling with an exposed frame (faux rafters are less cool), and remembered ~R60 is usually recommended for roofs. That would be nearly a foot of rigid foam! It seems pretty ridiculous, but is anything stopping anyone from doing it? Sure, using fiberglass batts for some of the insulation would be a little more economical, but how much more could, say, some recycled polyiso and fancy screws possibly be?
GBA Detail Library
A collection of one thousand construction details organized by climate and house part
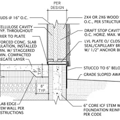
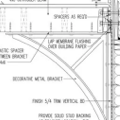
Replies
An R49 code-min roof really only needs to be R38.5 "whole assembly" after thermal bridging of rafter to meet code, and that includes the R-value of the roof deck, roofing, ceiling gypsum, interior & exterior air films etc. In practice 6" of foil faced polyiso with a nailer deck or 6.5" of fiber-faced roofing polyiso will usually push it over that mark even with nothing between the rafters. At 6" most fiber faced roofing polyiso is labeled R34-R35.
If you have 2x12 rafters you could install R23 rock wool and half inch gypsum or pine bead board planking or whatever floats yer boat under that and still have over 5" of exposed rafter. with R34-ish polyiso above you'd have R57 of insulation-only layers, 60% of which is above the roof deck, which is ultra-safe from a dew point control perspective in US climate zones 6 or lower, and still squeaks by in zone 7 if you count the R-value of the exterior nailer deck.
Hi Dana,
Thanks for the quick reply. I know R60 is above code by a good amount, but I hadn't considered the whole assembly code exemption worked so well in this application.
Partially exposed rafters was a something I had considered, and is likely the sane solution to this specific issue.
Based on you providing two solutions that avoid thick foam, I take it using more that 6" of foam is usually a bad idea? Or just silly and not cost effective?
>"Or just silly and not cost effective?"
Silly sometimes, awkward and hard to assemble when going thick, always.
Cost effective, almost never, below US climate zone 6, but maybe if using reclaimed foam. The fastener budget doesn't get cheaper with longer screws and the tighter spacings sometimes necessary on high-pitch roofs.
For the likely cost effectiveness crossover range, see the "Compact Roof" column in Table 2, page 10:
https://buildingscience.com/sites/default/files/migrate/pdf/BA-1005_High%20R-Value_Walls_Case_Study.pdf
Note that R60+ whole-assembly can still be cost effective in climate zone 4 if it's deep fluff on the attic floor, but R60+ is at the edge of cost effectiveness for zone 6 in a compact roof, per that table.
Thanks for the extra info! That Building America report has some useful information, and with the cost of solar panels coming down so much since 2010 I bet even Zone 6 is questionable for a full R60 now (I happen to live in zone 5 with plans to move to zone 6). I am reminded of Martin's article on the subject:
https://www.greenbuildingadvisor.com/article/r-value-advice-from-building-science-corporation
Unfortunately, I can no longer access it due to the paywall (someday I'll be able to justify a subscription to the spouse!), but I can still run the numbers through BEopt and see what I get. It could be that beating the code isn't worthwhile any more, though it is worth considering comfort advantages extra insulation provides.
Not only has the cost of PV been cut by 2/3 since then, the efficiency of residential panels has increased from ~15% to ~20%, so it takes less roof area to hit Net Zero.
The efficiency of best-in-class cold climate heat pumps have also jumped from about HSPF 10-12 to HSPF 12-14, taking less overall power, and heat pump water heaters have jumped from ~EF 2.0 to EF 3+.
There's more to high-R than the net-present-value-of-avoided-future-energy costs, there are comfort issues too, that make better than code windows "worth it", and in heavily snowy parts of zone 5 the ice damming mitigation of something better than U0.026 can be too.