Is it the average mean, or the average low temperature I should use to calculate BTU needs and condensation points?

So I am calculating whole wall R-values and condensation point within the wall…..
In my calculations so far I have used the average “low temp” of the coldest month. Actually I used a temperature just a bit 1-2 degrees colder than the average low temperature listed. But in further reading, I noted that some only use the average “mean” temperature of the coldest month, and not the average of the “low” temp. Which is it…cause it would “mean” the difference in a few inches of insulation on the exterior?
Zone 6A – 8200 or so Heating degree days
For my town – January 30 year data is: MAX 27.1F / MEAN 15.3F / MIN 3.5F
GBA Detail Library
A collection of one thousand construction details organized by climate and house part
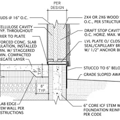
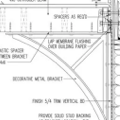
Replies
Brad,
Joe Lstiburek advises using the average of the mean temperature of the coldest three months of the year.
For more information -- and full instructions on dew-point calculations -- see Are Dew-Point Calculations Really Necessary?
Martin,
Thank you for linking to the 2010 discussion on this subject. That discussion would clear up Brad’s questions considerably.
It is not ASHRAE’s position to use the average of the coldest three months in some version of a steady-state tool. Perhaps it came from Joe Lstiburek’s shop? It might work pretty well. I haven’t compared it to transient results.
ASHRAE developed Standard 160 precisely to answer questions like Brad’s. It uses transient rather than steady-state analysis. It uses hourly outdoor conditions over a year—or over ten years—rather than some average. And it uses a wetness criterion that is very different from “condensation”. Whenever I hear someone use a term like “condensation point” I realize we’re not getting the word out like we should.
Bill,
Thanks very much for the added information on this topic. Needless to say, I defer to you.
I've been trying to do my part to clarify the "condensation" question by emphasizing that, in discussions of cold wall sheathing, we are talking about moisture accumulation rather than condensation. However, explaining the difference is somewhat of an uphill battle. Eventually these concepts will be better understood by builders, although I foresee years of repitition ahead.
I have corrected my earlier response to credit Joe Lstiburek rather than ASHRAE for the dew point calculation method discussed in my 2010 article.
Having read the article Martin alluded to, I can concur that it is BSC that published the three month average assumption. I do realize that it is not truly condensation to a point, but that it is a moisture point, that has many variables, not just including the single path talked about when calculating wall point values. Trying my best to design and build a healthy (the only true green), and sustainable home, that is also energy efficient for the long haul..........just like I practice evidence based medicine in my "full-time job as a firefighter and paramedic - I am trying to adapt the same philosophy here with my home. Having just part of the answer or a generalization is not satisfactory for me.....I am also trying to determine the calculations on my own (with help of course) to give me a fuller understanding of the why, and the recourse of each decision.
What other wetness criterion should I be figuring for - or better yet what am I overlooking?????
By the way thanks for the feedback!
Brad,
“What other wetness criterion…?”
Condensation, strictly speaking, is the change in phase from vapor to liquid water. Mold is not a fish. So the presence of liquid water (as a consequence of condensation) is not a good criterion for preventing mold on organic materials and for preventing corrosion of metals. Corrosion and mold growth require a high level of surface wetness over a long period of time. A water activity of 0.8 on average over 30 days at a high enough temperature seems to support mold growth, though there is a lot of back-and-forth on that. Water activity of 0.8 translates to surface RH of 80%. Transient hygrothermal models such as WUFI can handle this criterion.
For dew-point calcs relative to moisture accumulation in wooden sheathing I tend to use the January mean temp for a location rather than the 3-month winter average, and for cold climates (US zone 5 or higher) assume the conditioned space air is controlled to a max of 40F dew point (about 35% RH @ 70F), which is easily accomplished by adjusting ventilation rates in US zone 6.
It's a very crude model, doesn't tell the whole/real story of what's going on, but it yields a reasonably "right" answer for US zone 6A without a more sophisticated model, and without building-in excessive & expensive margin when looking at exterior-foam as the solution for protecting the sheathing from wintertime interior moisture drives.
Using cellulose cavity fill also protects the sheathing and adds resilience, but I too rely on more sophisticated modeling (WUFI: http://www.ornl.gov/sci/btc/apps/moisture/ ) to gain comfort on it when I'm not sure.
IIRC in Canada code requires that the sheathing remain at or above 5C even at the outside heating design temperature to be able to skip interior side vapor barriers, which is a MUCH more stringent (and unnecessary, IMHO) design constraint.