Is building science ahead of code or just the code official?

I used 6 inches of glass faced polyiso in a wall assembly (two 3″ layers). I based my assembly on the high R wall case 12 (Exterior Insulation FS) tested by Building Science Corp. Actually, my assembly is also like the REMOTE wall tested by the CCHRC.org in Alaska. Or the PIMA ‘Warm Wall”…
Anyhow, for some reason the building official for my community seems to think that the code restricts the use of anything more than 4 inches of foam plastic anywhere in the building assembly. He also wants me to produce documents that show that the specific brand of polyiso which I am using has been tested in this exact assembly. The material is stamped “Approved to comply with Factory Mutual… Class I …”
On one wall of the building I applied 5″ (one 3″ and one 2″ layer) of expanded polystyrene. This material was salvaged from a ballasted roof deck… So, maybe he can get me on a technicality. But why does he want to get me? I thought I was delivering above and beyond the code. How could it hurt? I could post a copy of the assembly…
So, yes, I had a building permit. Yes, I have installed everything except the finish. Yes, my architect signed off on this. Yes, I called for an EIFS system on the exterior of the building. Yes, the plans call for exterior insulation. No, they did not call for 6 inches. Yes, several inspectors gave me the thumbs up on the insulation. I even asked if they wanted to inspect again before i applied the finish assembly–light weight perlite based stucco. (Originally planned to use hardi but zoning code pushed toward stucco)
Is there anything in the code that says I can not use 6 inches of insulation? Is there any polyiso insulation that can be applied at 6″ thickness and meet code requirements? Is there any polystyrene that can be used as I am using it…
my layer are as follows from the interior…
1/2″ gypsum board > 2x framing > 1/2″ or 3/4″ OSB sheathing > bitumen primer > 60mil modified bitumen covered with cross laminated poly applied from below grade to top of parapet wall > 2 layers of aforemetioned polyiso > 1/2″ osb attached with 9″ XHD roofing screws and 2″ galvanized plates to studs >………. expect to add the following…. tyvek > type d double layer building paper > j-channel for stucco > expanded metal lath > 3 layer stucco using perlite as aggregate substitute for sand.
Am I not getting something?
I am doing my best to be green and better than required but I am treated like I am the bad guy from another planet.
Links
http://www.cchrc.org/docs/best_practices/REMOTE_Manual.pdf
GBA Detail Library
A collection of one thousand construction details organized by climate and house part
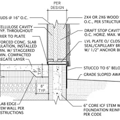
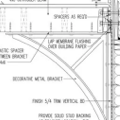
Replies
You don't indicate where you're building, so I can't speak to local codes or the motivation or interpretation of your code official...
...but from where I'm standing, building oversized beer coolers for people to live in is something I might expect from extraterrestrials, since it's surely not a technology indigenous to planet Earth. And there's nothing "green" about creating dead hermetically-sealed boxes for living creatures to inhabit.
Green means nothing if it doesn't mean organic, living, breathing and natural. Homo (not so) Sapiens spent the last 25 million years evolving with natural materials and habitats. We are not biologically suited to plastic air-tight enclosures.
Maybe your code official is tapping into the collective unconscious or hearing a message from Gaia.
William,
You write that your local code official objects to your foam "for some reason." You can't address his concerns until you understand his reason better. Ask, "Please cite the code provision that my wall may violate." Unless he can cite a code provision, it's hard to know how to reassure him.
Your next step is to contact the Foam Sheathing Coalition, an industry group set up specifically to help builders like you navigate code questions with local code officials. Here is the Web page with contact information:
http://www.foamsheathing.org/contactus.php?PHPSESSID=nm47kt0srrcn9cu9e20ee10k50
I was in a similar situation, Timberframe, REMOTE curtain wall, 5.5" of foilfaced polyiso...the building officials wouldn't touch it with a ten foot pole.... Funny because the REMOTE is based on a Canadian PERSIST system used since the 70's...you would hope a Canadian building official would welcome the idea of applying this system to a residential project with full support... not so...They all liked the idea, but would not put their sigs on the approval...After playing "pass the buck" game with various levels of their organization, I finally got the idea stamped by a Peng, submitted it, and moved on...