Is an HRV/ERV system necessary?

My husband and I are building on our own a small house that we’ve tried to make as green as possible. Neither of us are familiar with green building (he’s conventional framer) and we rely on this website and green building books to answer our questions. The one thing I’m stuck on is, do we need to have an HRV or ERV system? We are building the house as tight as possible, sealing all leaks, and have an inch of rigid foam on the exterior and will have R-21 cellulose interior insulation. The house is 24×24, two floors and an unfinished basement. It will be heated with a wood stove on each floor and the bathroom will have a small electric heater. We’re on Cape Cod (Zone 5). We want fresh air circulating in the house to have a healthy home, and we’d also like to have enough air for the wood stoves to run. A quote to install an HRV system was way too high for us, so my husband thought he could install the product the company recommended himself. But now when I’ve talked to other HVAC specialists, they say the products don’t even work that well and are a waste of money. Does the house need an HRV? Would a minisplit or two do the same work of providing fresh air and some heat? Should we just open the windows from time to time (as recommended by our chimney installer)? Thanks!
GBA Detail Library
A collection of one thousand construction details organized by climate and house part
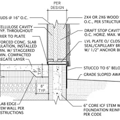
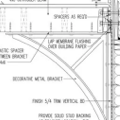
Replies
Cathy,
A tight home always needs a mechanical ventilation system. A minisplit has nothing to do with ventilation. A ductless miniplit system is a type of air-source heat pump used for cooling or space heating -- not ventilation.
You can ventilate your house without an HRV or an ERV if you want. To read about all of the ways you can ventilate your house, see Designing a Good Ventilation System.
Thanks for your reply! I read the article you linked to and it still seems that we're left with installing either an HRV or ERV for our house if we want to have ventilation. We don't have a heating system or furnace, so it doesn't seem like a central fan integrated system is an option. A bathroom ventilating fan is code, so we'll definitely have that. Is that enough?
Are there particular brands of HRV systems that you recommend? Because the HVAC installer I trust said the ones he is familiar with don't work well....
If a bathroom fan is enough, and you don't think we'll have a problem with fresh air intake or enough air for the woodstoves to work, then I'm happy with that much cheaper option! Thanks again!
Cathy,
As my article stated, there is nothing wrong with an exhaust-only ventilation system. Plenty of people are quite happy with the performance of such a system.
Exhaust-only ventilation systems use one or more high-quality bathroom exhaust fans (usually a Panasonic) controlled by a 24-hour timer. You want the fan to run enough hours each day to satisfy ASHRAE 62.2 requirements (but no more than that).
The article explains the advantages and disadvantages of each kind of ventilation system, including exhaust-only systems.
I don't know why your HVAC installer thinks that HRVs don't work very well. As long as they are installed properly, most HRVs perform very well indeed.
Thanks very much. I'll look into ASHRAE 62.2 requirements.
Thanks for all that you provide on this website, it's beyond helpful.
Cathy,
ASHRAE 62.2 requirements are explained in the same article (Designing a Good Ventilation System).
If you go the exhaust ventilation route, both Panasonic and Broan make very nice fans that can be set to a specific ventilation rate (in increments of 10cfm). This should enable the fan to run continuously and would eliminate the need for a timer.
http://www2.panasonic.com/webapp/wcs/stores/servlet/ModelDetail?displayTab=O&storeId=11201&catalogId=13051&itemId=487154&catGroupId=119505&surfModel=FV-08VKS3
http://www.broanultra.com/zb80.html
Wood stoves that rely on conditioned space air for combustion aren't a great idea in a very tight home. There are many units out there set up to duct in combustion air.
Also, in a house that small & well insulated it might be tough to find woodstoves tiny enough to not turn it into a sauna if you're burning it at a high enough rate to kick a non-catalytic EPA woodstove in to secondary-burn mode (necessary for it to come anywhere near meeting it's EPA emissions or efficiency ratings.) The true heat load of that house at outside design condition is probably under 15,000BTU/hr unless you keep the windows open on the coldest night of the year. If you go with the woodstoves, find something with max-fire of ~35KBTU/hr or less, and something with it's own thermal mass like a ceramic or soapstone model, an EPA rated steel or cast iron stove will give you hot-flashes getting it up to secondary-burn temp.
Heating/cooling with mini-splits would also be a good option, since they can be had in smaller sizes and modulate well with load when right-sized. As fully modulating systems they also "play nice" with woodstoves, automatically backing off when you crank up the fire, but maintaining room temp as the woodstove cools. But as Martin points out, they are not ventilation systems.
Along the lines of Dana's comments regarding wood stoves - I was forwarded this link recently regarding a new US-made low-capacity woodstove.
http://unforgettablefirellc.com
Thanks everybody! This is so helpful, wish I had posted months ago!
Dana, I will look into the ceramic and soapstone stoves, thank you! My husband is quite partial to Vermont Castings stoves...would one of their smaller catalytic stoves be suitable?
Minisplits are aspirational right now, they're out of our range. Good to know they play nice with wood stoves, though.
BTW: An inch of foam on the exterior isn't enough to allow you to skip the interior vapor retarder. But for less money than virgin-stock there are several vendors in MA selling reclaimed roofing foam in good condition for about 1/4 the cost. of new goods, usually in in 2" to 4" thicknesses. At 2" sheet polyiso (any facer type) would nearly double the whole-wall R of a no-foam 2x6 wall (after factoring in the thermal bridging of the framing) of your 2x6 construction, and at 3" it would more than double it. Search some of the nearby craiglist materials sections for "rigid insulation" and you'll find some of them. If you can drive as far as Framingham (it's a haul from the Cape), there's always the Insulation Depot on Waverly Street (insulationdepot.com.) There's nothing greener than re-using building materials, and you'd be money head even if you have to patch or scrap some of it.
At 2" any type of foam would get you to the magic R7.5+ needed to meet code without an interior vapor retarder, but with iso you'd be at ~R12. Three inch stock is still pretty easy to handle, and that's what I'd recommend. If that would make your wall assembly too thick, back off to 2x4 on the framing and you'd be at exactly the same wall thickness as 2x6 + 1" foam, but instead of ~ R19 whole-wall you'd be looking at ~R28 for about the same money as a 2x6 solution with virgin-stock foam. (If you stayed with 2x6 construction and 3" of roofing iso on the exterior you'd be over R30.)
The Vermont Castings Aspen is a li'l cutie that probably won't roast you to death, but and is DOES have provision for ducting in outside air. If you're going for a 2-stove solution that might be the way to go. The Intrepid II does too but being an iron stove with 36KBTU max firing rate it's going to be more prone to the hot-flash issue even at a third to half-throttle where it needs to be to hit it's efficiency numbers. The Hearthstone Tribute is nice little soapstone model, but is limited to 16" wood, which can be an issue in an 18-20" cordwood market. (It's fine if you're cutting your own.) The Euro-modern Hearthstone Bari takes longer wood, but might be a budget buster (but then almost any soapstone unit might be.)
Hi Dana,
I'm not sure that I'm following everything that you wrote and I want to make sure that I am. Maybe it would help if I clarified some things.
1. Insulation: Our roof does not have the exterior foam insulation (mostly because we didn't think about it, but also because the attic is not a part of our envelope). Roof has plywood, tar paper, asphalt shingles. The siding has plywood, tar paper, 1" of foil coated polyiso, red cedar shake. We added the 1' of foam insulation as a bonus, not to meet code. Our plan on the interior is to have code R-value blown in cellulose (we were quoted for R-21 in the walls, R-40 or R-55 for the attic floor) and then sheetrock or plaster. The basement is not part of the envelope either. It is 2x6 construction. Do we still need a vapor retarder on the interior? What sort of vapor retarder do you recommend?
2. woodstove/chimney: the chimney is already built with 2 flues, one for each floor. We asked the mason about ducting in outside air and he laughed it off. I was refering to the Intrepid II before, if we got that would we have to cut through the chimney? (Is that even possible?) or through the sidewall? Are we going to be able to have any sort of stove??
I appreciate your expert advice. We haven't had much help from the pros we've worked with/ consulted with on trying to make this building green--everyone asks us "you want to do WHAT? why??" and so we just take bits and pieces from this site and the green building books and textbooks. I hope we haven't made some terrible mistakes. Thanks again.
A couple of quick comments here.
1. I would be hesitant to invest in a HRV unless I *knew* that the house was going to be very tight, I were in a very cold climate, and/or the house layout was such that remote rooms might not get enough circulation. Our house is very tight and operates fine with exhaust-only ventilation using a WhisperGreen fan. I am more aware than most of IAQ issues and pay attention to "operating" the house correctly, but we don't need more ventilation equipment than that. My experience of blower door testing many houses is that most people are not building tight enough to benefit from a HRV--there is already more than enough infiltration.
2. A woodstove with ducted outside air is a major plus if the house is tight, in fact it's probably a must. We have a Morso 3142 with ducted outside air in the house and it burns well no matter what is going on. We have a Morso 1440 in the shop without outside air, and I usually can't light it if the bath fan is running. I would definitely spend the money and effort to go with outside air.
Just because the iso came off a commercial building roof doesn't mean you can't apply it to walls. I was talking about using it in walls, not roofs (though it works surprisingly well on roofs too. :-) ) The R40-R55 on the attic floor is pretty good, as long as it's air-tight at the attic floor.
Going with only 1" of foam on the walls puts you in an in-between state regarding interior vapor retarders. The type of foam matters, but all exterior foam reduces the ability of the sheathing to dry toward the exterior- it's only a matter of how MUCH it's limiting outward drying. But foil-faced iso is a COMPLETE vapor barrier, with not one but two class-I vapor retarders, which means all drying MUST be toward the interior.
It would be nice if the assembly could be left fairly vapor-open to the interior, which it could if you had even 1.5" of exterior iso, but with only 1" you can't. With insufficient exterior-R such that he structural sheathing will spend many winter hours below the dew point of the conditioned space air and take on substantial moisture, made somewhat worse by the fact that there is now zero drying to the exterior.
If the cavities are still open and the cellulose isn't in yet you still have a few options:
1: A flash-inch of closed cell spray foam applied to the sheathing from the interior (at about a buck or so per square foot, maybe $1.25 if it's not as competitive on the Cape) will air-seal the cavities nicely, and puts a ~ 1-perm vapor retarder between the susceptible wood and the interior, and makes the non-wicking interior side of the foam the condensing surface. This is a very good solution, but may be a budget buster.
2: Install Certainteed MemBrain film under the gypsum as a variable-permeance vapor retarder. As long as you keep the interior room humidity under 35% @ 70F in winter it will be about a 1-perm vapor retarder, but if the cellulose or structural sheathing loads up in winter it can still dry rapidly in spring when the interior RH rises, and the MemBrain hits 2+ perms. This is a pretty-good solution but not foolproof in tight house. (It's pretty foolproof if you had an ERV/HRV system though.)
3: Apply vapor-barrier latex primer on the wallboard. This reduces the permeance to about 0.5 perms, which is enough to limit wintertime moisture loads, but unlike MemBrain any drying is also dramatically slowed. This is the 3rd suggestion because it's really the third-rate solution, since it lowers the drying capacity of the assembly so severely.
With 2" of exterior foam you could have just skipped the interior vapor retarder, and the overall drying capacity would have been enhanced. With 5.5" of dense-packed cellulose the fiber can buffer some amount of wintertime moisture, but it's capacity is not infinite.
Before you put up the gypsum be sure to air seal between any doubled-up studwall plates with a bead of caulk, as well as at the bottom plate/subfloor junction, or you could end up with some damp spots on the exterior sheathing from that air leak too. Air seal any electrical outlets to the gypsum AND to the wire penetration as you go too. Air leaks can move a lot more water than vapor permeation through latex paint.
It's always possible to core through a chimneys & hearths with masonry coring bits if need be- professional woodstove installers do it every week, if not every day. It's simpler to duct in combustion air if the chimney is on an exterior wall, but it's possible to go under the floor to side-wall it between floor joists. IIRC code requires 1" clearance to combustibles for the intake air vent, and you can wrap it in rock wool where it goes through the exterior wall of the house. Just be sure it's above the snow-drift line. If your woodstove installation instructions don't spell it out for you, I believe the spec on outdoor combustion air ducting clearances to wood-burners is in the IRC 2009 (current MA code). The folks who sell you the combustion air kit should be able to quote it chapter & verse for you.
The basement is ALWAYS part of the building envelope- the cube has six sides, not five! Even if you insulate between the joists and put rigid foam on the bottom it's still part of the envelope- it's damn-near impossible to adequately air seal that plane, since it has 1001 electrical & plumbing penetrations, even if there is no direct access from the inside of the house, only a outdoor bulkhead-door.
But air-sealing the band joist & foundation sill is fairly straightforward, and reclaimed roofing insulation is dirt-cheap- cheaper than mid-density fiberglass batts per square foot per unit-R.
Cathy, we are also working on our own green building project - a green retrofit/deep energy retrofit in Chicago - and also had to resolve the ventilation question.
I found it helpful to read up on case studies or accounts from people who actually did the things we were planning on doing. If you think an actual account would be helpful to you too feel free to read about our ventilation experience on our project blog.
The first link is a summary after we had finished the installation of an ERV in the garden apartment of the building. The second link are posts under the ventilation category. If you browse through there you find more information about our research, decision making process and the installation.
http://delafleur.com/blog/?p=2353
http://delafleur.com/blog/?cat=89
Hope this will be helpful!