Interior vs. exterior air barrier

Wondering what the consensus is on the interior vs. exterior air barrier issue is? I am considering this question in light of a double-stud, dense-pack cellulose wall.
Marc Rosenbaum has indicated that he prefers exterior air barriers, because they are so much simpler to execute (no zig-zagging around floor systems, etc).
Joe Lstiburek’s “Ideal Double Stud Wall” and the Pro Clima engineers have indicated that they feel that interior air barriers create a more durable wall because they prevent humid interior air from convective looping within the wall (if not actually ever leaking to the exterior), and potentially reaching the dew point on the exterior framed wall before making their way back to the interior.
What are people’s thoughts on this, in this particular double-stud/dense-pack cellulose context?
GBA Detail Library
A collection of one thousand construction details organized by climate and house part
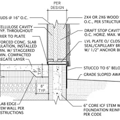
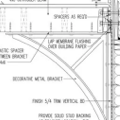
Replies
Burke,
Either approach works fine, especially if the walls are insulated with some type of insulation other than fiberglass batts.
It is certainly true that it's easier to establish an effective air barrier at the exterior sheathing than at the drywall layer; I agree with Marc Rosenbaum on that issue.
Those who insist on an interior air barrier often exaggerate the disadvantages of an exterior air barrier. If the wall is insulated with dense-packed cellulose, there aren't going to be any convective loops. And if the exterior air barrier is effective, there won't be any air movement through the wall due to exfiltration. So there is no driving force to encourage indoor air to enter the wall cavity.
I wrote an article on this topic in 2010 (“One Air Barrier or Two?”). In that article, I concluded, "To a large extent, double air barriers are an attempt to respond to the inherent performance problems of fiberglass batts." So don't use fiberglass batts.
Question for Martin: what do you think of blown-in fiberglass instead of dense-packed cellulose?
C.B.,
Blown-in fiberglass can be installed at different densities, just like cellulose. It is typically installed at about 1.8 pounds per cubic foot -- considerably less than dense-packed cellulose, which is installed at 3.5 to 4.0 pounds per cubic foot. The higher the density of the blown-in fiberglass, the lower the chance of convective loops.
If blown-in fiberglass insulation has been installed by a conscientious contractor in a wall with an exterior air barrier, I wouldn't worry about convective loops. That said, if cellulose is available, I would always choose cellulose over fiberglass.
For more information on blown-in fiberglass, see Getting to Know Spider Insulation.
Miracle of miracles- a clear, simple answer in the world of sustainable building!! Ha, ha! Thanks Martin. That's what I kind of thought as well, but wanted some confirmation.
At 1.8lbs density fiberglass is every bit as air retardent as 3.5lb cellulose. It's only at lower densities of both that cellulose dramatically outperforms fiberglass on air tightness. At 2.2lbs fiberglass is in the same tightness range as 4lb cellulose.
See the air resistance curves vs. density on p.2 of this document:
http://www.jm.com/content/dam/jm/global/en/building-insulation/Files/BI%20Toolbox/Dense_Pack_JMSpider_vs_Cellulose.pdf
Notice that the curve doesn't show just how miserable fiberglass is at 1.0lb density, but 1.0 density IS a recommended and standard density for most fiberglass blowing wools (including JM Spider). If you go that route, a minimum of 1.8 lbs will be tight enough to prevent performance loss convection.
See also:
http://www.jm.com/content/dam/jm/global/en/building-insulation/Files/BI%20Toolbox/JMSpiderDrillAndFill_3rdPartyTestResults.pdf
There are other good reasons to opt for dense packed cellulose over dense packed fiberglass (lower embodied energy, higher thermal mass, much higher hygric buffering capacity, lower cost), but mere air tightness isn't one of them.
Dana,
Thanks for your comments. I have modified my earlier response in light of the data you shared about fiberglass installed at a density of 1.8 pounds per cubic foot. I appreciate the correction.
Having used OC ProPink L77 in my house, Dana's answer got me looking for details on it. During my looking, I found that (not a surprise) Dr Joe and company had done research into all of this only a year ago.
For the record in case anyone in the future looks at this thread for information, see:
http://buildingscience.com/sites/default/files/migrate/pdf/BA-1408_Airflow_Resistance_Loose-Fill_Mineral_Fiber_Retrofit_v2.pdf
One document missing from Appendix A of BA-1408 for ProPink L77 is:
http://www2.owenscorning.com/literature/pdfs/10016096%20Unbonded%20Loosefill%20Installation%20Tech%20Bulletin.pdf