Interior rigid foam installation

I am remodeling a 1905 Folk Victorian (code for farmhouse). The majority of the house is 2×4, with the exception of an addition which is 2×6. I looked into foam exterior but it would involve removing a lot of original molding and architectural details that add to the house. With spray foam at $7000, it is a $6000 premium over fiberglass. Not worth it. This is where I decided to go with XPS on the interior (or even polyiso).
I have read that the interior foam approach is somewhat accepted. I have a different question though: inside of my walls is a layer of plaster and lath (presumably for air sealing). I want to be sure if I leave it be that it would not cause issues in regards to vapor retarder location. The old wall system would be as follows: siding>tyvek>3/4 t&g planks>plaster>fiberglass (or cellulose)>xps>fir strips>drywall.
On the first floor I had to tear out much of the insulation for structural repairs. However the rest of the existing structure has blown in cellulose in excellent shape, so I’d like to leave it in.
The addition has 2×6 with R-19 fiberglass. I would probably add foam here too. I’m not looking for superinsulation, I’m simply trying to outperform the bare minimum.
I live in South Dakota, zone 6a. Interior vapor retarder is required.
Any advice appreciated!
GBA Detail Library
A collection of one thousand construction details organized by climate and house part
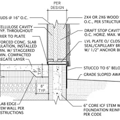
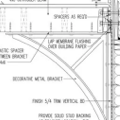
Replies
Ryan,
It's possible to install interior rigid foam on walls in your climate. The resulting wall will never perform as well as a wall with exterior rigid foam, however.
The problem areas are the rim joists and the partition intersections. If you remove interior finishes to gain access to these areas, and if you do a meticulous job of air sealing and insulating the rim joists and partition intersections, then your approach can work.
Good luck.
If going with a fiberglass solution for the cavitiy fill, dense-packed (1.8lbs/cubic foot or more) is highly recommended, and you can do it without removing any plaster/lath/molding. (Drilling from the exterior is best, if you're re-siding, but it can be done from the interior with a single ~2-2.5" hole per stud bay.) Dense packing the fiberglass will reduce infiltration nearly as well as a sprayed-foam solution- unlike foam which only expands into the adjacent space on which it lands, fiber blown under pressure will flow into all exfiltration points, clogging those leaks. At ~1.8lbs density blowing wools such as Optima or Spider are as tight at 3-3.5lb density cellulose (which is another alternative to consider.) Blowing at lower densities isn't nearly as effective at air sealing. While it's not tight enough to be considered an air barrier for all purposes, dense packed fiber is a tried & true method of tightening up antique houses.
Balloon framed Victorians can often be dense packed mostly from the attic (and sometimes basement), and the only wall drilling required on the interior is where bays are blocked by window/door framing.
Unlike fiberglass, cellulose has the benefit of being able to buffer wintertime moisture in the insulation, protecting the structural wood. But if this house has un-flashed or poorly flashed windows cellulose could create issues by soaking up too much bulk-water intrusions. To know which would be the better approach in your case would require a bit of on-site investigation.
R19 fiberglass is the real dog of the insulation biz due to it's very low density. (It's the same weight per square foot as R13s designed for 2x4 construction- just fluffed out more, with VERY low resistance to air flow.) If you're already going to be blowing insulation elsewhere, before adding the interior foam it's probably worth drilling a few holes per bay in that section and packing over the batts. You probably won't be able to snake in a dense-packing hose, but it's possible to hit ~2.5-3lbs density, and get most of the air-sealing benefit that you'd have on the true dense-packed areas.
Ryan,
Unlike Click and Clack, the Tappet Brothers, I don't do relationship counseling. So when it comes to negotiating with your wife and your father, you're on your own.
I think that your gable siding will look goofy if the siding below it ends up proud of the cedar shingles. The whole point of this type of gable design is that the gable needs to be proud of the siding below.
If you decide to install a continuous layer of exterior rigid foam, the cedar shingle pattern can be recreated by your siding contractor -- or you, or your father. Just photograph the gable before you demolish the siding, and then copy the pattern.
Thank you all for your replies. I have another thought on this if i may ask. All of the siding details of the house that we would like to keep are above the ceiling in the house. If one was to do foam insulation, could you just foam up to the existing siding (well, the cedar shingles) and then do some sort of continuous combination sill/drip edge to compensate for the difference in thickness? Even as I type that out it sounds like a trick to get perfect.
Main concerns of adding rigid foam to the interior are that space is sort of precious (narrow house) and wiring gets a couple more steps (such as box extensions on all exterior walls).
Stuck between a rock and a cold house!
Ryan