Interior poly vapor barrier?

I’m renovating a cape built in 1955 in Falmouth, Maine zone 6A. I have created two new stacked bathrooms. Both have one 8′ wall which is the exterior wall. The original house is framed with 2×4 wood studs and has 3/4″ T&G wood sheathing and wood shingle siding. I removed the old interior plaster finish and framed an additional 2×4 wood stud wall just inside the old. I have installed a layer of 3 1/2″ ROXUL with the old studs and a second 3 1/2″ layer of ROXUL within the second wall studs.
The two layers are pushed tight to each other. There is a new 3′ x 4′ PARADIGM double-hung window in the center of this wall. The interior finish will be 1/2″ HARDY tile backer board for the first 3′-6″ then 4′ high painted 1/2″ gypsum wall board up to the ceiling. The ceiling is the old 3/8″ plaster on 1/2″ gypsum backer board.
My question is: should I install a 6 mil poly vapor barrier to the inside face of new wood studs before applying the finished boards?
Thanks,
Brian
GBA Detail Library
A collection of one thousand construction details organized by climate and house part
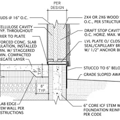
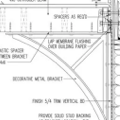
Replies
Brian,
Q. "Should I install a 6-mil poly vapor barrier to the inside face of new wood studs before applying the finished boards?"
A. No. Instead, pay careful attention to air tightness. For more information on poly vapor barriers, see these articles:
Vapor Retarders and Vapor Barriers
Forget Vapor Diffusion — Stop the Air Leaks!
I'm a big fan of avoiding polyethylene, especially in new construction. But at first glance it seems a reasonable thing to do in Brian's situation:
Roxul's website ( http://www.roxul.com/residential/vapor+barriers ) states that a vapor barrier/retarder is essential, and that polyethylene is the first choice of many professional contractors. (Interestingly enough, though, they do start their explanation addressing "vapor transmission," but as they get more detailed they actually refer to air-transport of moisture into the wall...).
The 2009 IRC (in the absence of adequate exterior foam insulation) requires a Type I or II vapor retarder; polyethylene satisfies the Type I requirement.
Presumably the T&G wood sheathing and the wood shingle siding are highly permeable, such that his wall will readily dry to the outside. I've read that 15# felt has a perm rating of about 30 (?) so that even if it's part of the construction, it wouldn't significantly decrease the wall's ability to dry.
Given the existing wall construction, and assuming that he's not removing the exterior siding to add foam insulation and/or an air barrier, how does one go about addressing air tightness? If polyethylene is not recommended, is it instead best to just gasket and seal everything such as electrical boxes, recessed mirrors, etc., and use an appropriate latex paint?... Is it worth doing only an 8' section, when adjacent exterior walls aren't necessarily being addressed?
Thanks!
Will,
I think that Brian should install his backerboard and drywall following the Airtight Drywall Approach, using gaskets, caulk, and airtight electrical boxes. If desired, a layer of MemBrain could be installed as a smart vapor retarder.