Interior plywood for earthquake areas — can it replace a vapor retarder?

We are renovating a 1925 Pacific Northwest house, Everett WA, right on the coast. It is earthquake territory here. So it would be good to keep this house up through any quakes we may get, when it can be relatively easily done. We have double studded the kitchen wall now. Making it 8″ deep. The north wall became 9″ deep. Now we are in low need of any vapor retarder for our climate I understand, zone 4C. Interior air barrier never hurts BUT, and here is my question… Would interior plywood sheathing be a good choice to replace the air barrier, caulking the seams. Plus give a major strength enhancement to the walls in case of any quakes?
Next question is for the upstairs.. Where we want to cool a bit in the summer plus dehumidify. Interior plywood also there and can plywood work like a smart vapor retarder? As when it gets moist (WET?) it increases it’s perm rating. Thickness an issue I would think. So 1/2″ for downstairs and no air barrier or vapor retarder. 1/4″ thickness upstairs WHEN it would make a poor man’s smart vapor retarder PLUS still give a strength enhancing working for the walls? Or should we forego the smart vapor retarder working on the plywood for the upstairs and just focus on either: 1/2 Plywood for stability. OR focus more on vapor control and have NO plywood but a smart vapor retarder.
Thanks!
GBA Detail Library
A collection of one thousand construction details organized by climate and house part
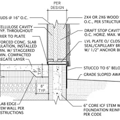
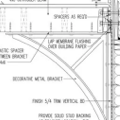
Replies
Jan,
The short answer is: Yes, plywood is a smart vapor retarder.
Remmeber, though: In your climate, there really is no need for you to worry about the vapor permeance of your interior layers. Vapor diffusion very rarely causes problems in walls, as long as you have exterior layers that inhibit inward solar vapor drive. (In other words, on the outside you need either a rainscreen gap, OSB, or plywood sheathing -- not fiberboard without an air gap -- and on the inside you don't want polyethylene.)
Pay attention to airtightness, and stop worrying so much about vapor diffusion.
Jan,
I also meant to give you one more piece of advice: if you are engaged in a seismic retrofit, you need to consult an engineer.
Vapor diffusion issues notwithstanding, stiffening framed walls in earthquake zones makes it more likely that the walls will walk off the foundation in an earthquake. That is the rationale in CA that makes it illegal to use construction adhesive to air-seal the exterior sheathing to the studs(!). It's better/safer during a quake to let the walls flex, even pop some sheathing nails and crack the drywall than to have it so stiff that it rips up the bottom plate from the foundation anchoring, shifting off the foundation.
I second martin's advice. Ad-hoc seismic ungraded usually don't yield predictable results. As Dana said, most houses have quite a bit of shear capacity in their existing sheathed walls. The weak points are usually mechanical connections, like anchoring to the foundation, floor to wall, and floor to roof.
Well I fear that even an engineer's knowledge can only do so much. The foundation anchoring will definitely be the weakest link in most cases. In our upgrade we had to put in some structural LVL joist combined with flitch beams. Those upgrades now make me look around and see that in case of a shaker the walls will be the first to give around the flitch plus LVL reinforced part of the house. In every area, foundation, walls, floors, ceilings nobody will really know what will happen when the earthquake or quakeS usually, will hit. It is not a new house but a retrofit and that makes it all the more that common sense will most likely be the best to apply. Yes... the foundation anchoring I fear will the most important and most difficult to upgrade.
When plywood though is considered a smart vapor retarder... My last thread died young and I hope we can revive it: https://www.greenbuildingadvisor.com/community/forum/gba-pro-help/39891/unvented-slanted-roof-radiant-cooling-and-no-polyurethane-4c
As I apparently do not need to worry about any smart vapor retarder for our climate, I will desperately need one in the ceiling as Dana brought up. 1/4" plywood between the WarmBoard as good as, better than MemBrain or IntelloPlus?
I copied these last sentences onto the original thread so respond here or at the original posting.
Thanks.
Jan,
Seismic retrofit work happens all the time. If you are worried about the connection between your foundation and your walls, an engineer or a seismic retrofit specialist can help. There are a variety of solutions for older houses -- special hardware has been developed for this work.
Thanks Martin. Yes, the foundation connection is definitely, in my simple thinking, the weakest link. We will have WarmBoard ceilings, so therefor MOST ceilings will become rigid boxes. So with the mentioned beams, and now the boxed floors/ceilings, the entire house will become more and more rigid. Definitely have to focus on the foundation connections. It is too complex for me to grasp the best route to go after that. So it will be good to get some expert eyes onto this.
Thanks!
Quarter inch plywood never becomes a class-II vapor retarder (at any moisture level), though half-inch goods can when bone-dry. Quarter inch plywood never becomes as vapor-open as MemBrain, but if you're using latex paint as the interior finish the latex becomes the limiting factor on drying rates, even in a MemBrain protected structure. While the MemBrain will be over 10 perms when there is a lot of moisture in the cavity, if there is 5 perm paint between the MemBrain & conditioned space it hardly matters. It takes a higher moisture content than MemBrain before the plywood goes north of 5 perms, but it will. It's "good enough", as long as it's air-tight. But it's a heluva lot easier to make wide long sheets of MemBrain truly air tight than air sealing a bunch of 1/4" plywood edge-butted to WarmBoard (or even as a tiled-in complete layer of 1/4" plywood above the WarmBoard.) MemBrain is quite a bit cheaper per square foot than 1/4" plywood too. (About $100 for an 800 square foot roll when purchase in small quantities through retailers.)
Moisture drives affecting framing cavities in zone 4C are primarily from the exterior. As long as you have a rainscreen gap between the siding & sheathing as a capillary break & drying path you don't really need (or want) an interior side vapor barrier tighter than 5 perms- but you DO want to make it air tight on both the exterior sheathing & interior side. Caulking 1/4" plywood to the framing on the interior would work, but don't glue it without factoring it into the seismic engineering plan. The stiffer the walls, the more force will be delivered to the foundation anchors.
This book really helped me understand shear wall design and importance of the connection path, roof to foundation... Not saying don't consult an engineer or specialist, but if you want to understand what a retrofit requires, very helpful.
Wood-Framed Shear Wall Construction; An Illustrated Guide Paperback – 2004
by Thor Matteson
Much appreciated! Want to be informed as much as possible as engineers are not bullet proof either in their approach, sometimes...
BUT whatever I do: I either end up with a pile of sticks and an intact foundation OR a crooked intact house on a cracked foundation. Mother nature will take over and decide at that point...
Thanks David!