Interior paint and vapor barriers

Hi all,
So we have spent the better part of a year building our home. It’s been a challenge.
Consults with building designers have led us to having a vapor permeable assembly. We used havelock wool with no internal vapor barrier, tyvek to the exterior of the home.
However, we just primed and painted the house with Ben moore Eco spec paint (had some spackle issues so needed an extra coat) and am only now realizing that the latex makes it pretty impermeable to vapor. This won’t allow the cavity to dry when vapor gets in.
Any thoughts on how to rectify this? Should I not be as concerned as I seem to be?
GBA Detail Library
A collection of one thousand construction details organized by climate and house part
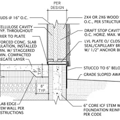
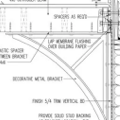
Replies
What climate zone are you in? What type of exterior cladding/sheathing are you using? Did you use exterior continuous insulation, and, if you did, what kind? Do you have the usual drywall interior?
If you're in a heating-dominated climate, an interior side vapor retarder is always a good idea, but not always necassary. The idea is if you can keep moisture out of the wall, drying becomes less of an issue. It sounds like your assembly MIGHT (depending on cladding/interior wall) have drying ability in both directions, which is helpful and limits the potential for moisture issues.
It's difficult to give much more detail without more information about your wall assemblies.
Bill
Hey thanks for your response!
We learned while building unfortunately. Next build will be better!
We are in NJ. Based on energy vanguard, risinger, and other new commentary we just have a simple wall assembly that consists of vinyl siding, Tyvek WRB, plywood sheathing, studs/havelock wool, and typical drywall etc.
We plan to have dehumidifiers pretty much all over the home as our last central one became filled with mold.
We are in a heating dominated area. However, it rarely gets too cold, and if it does, it's for short stretches. We've also had the home dried in for almost a year before starting drywall and finishes and there were no leaks. So pretty confident on that end.
We wanted to vapor barrier at all, but feel like the latex paint was a mistake.
Gavin,
Your wall is fine. There is a range of how vapour-open walls should be based on climate. For heat dominated ones you don't want them entirely open - and codes reflect that requiring different levels of vapour-retarders for each one. Your paint is not a vapour-barrier, it is a vapour-retarder, and will be beneficial in your climate to stop interior moisture from entering the walls at a greater rate than it will be removed to the outside.
Your exterior of plywood/tyvek/vinyl siding should be pretty vapor open, so good drying to the outside. Blocking vapor from getting INTO the wall is usually more important in heating-dominated climates, so I don't think the paint is going to be much of a problem here. Latex paint isn't a vapor barrier unless you specifically used vapor barrier paint. I pulled up the SDS for the paint you mentioned and the associated primer (not sure what you used exactly), and it doesn't mention anything specific about vapor permeance, which makes me think it will behave similarly to any other latex paint around 5 perm-ish or so.
Bill
Bill,
Here is what the code says:
https://www.greenbuildingadvisor.com/article/building-codes-update-vapor-retarder-requirements
We spoke with many many building scientists on this and the consensus was we don't want any vapor retardation or barrier so we can have it totally dry to the interior no matter the climate. Of course extreme areas with severe temps are often a different circumstance.
There was a great depiction on energy vanguard on how much water actually difuses through a wall assembly, which is why a plastic sheeting could potentially be more harmful by totally blocking diffusion. The problem is, will this vapor retarding from the latex now cause slowing of said diffusion and retention of moisture within the cavity.
Gavin,
Unfortunately there is no universal solution which works well in all climates, which is why the IRC requires different levels of interior permeability for each zone. The direction of the vapour-drive in heat dominated climates is overwhelming to the exterior, so yes you do want to slow that drive, which the paint does effectively. With no vapour-retarder you will get more wetting that drying in the wall for most of the year. During the summer the paint simply isn't vapour-closed enough to be a problem. What you have ended up with is the standard code compliant wall used on all the buildings around you - and it works well.
Remember that a vapor retarder like this slows diffusion in BOTH directions, so any limits it places on drying also apply to wetting. Your particular assembly can dry in both directions too, since you have a vapor open exterior portion of the wall assembly.
I agree with Malcolm here: you have pretty much the standard assembly, and I wouldn't worry about it. The paint is helping you more than it's hurting you, and you're unlikely to have any problems here.
Bill
I hear you.
My understanding is this: there will always be vapor and condensation in the walls at some point. Code requirement by me requires a full on poly sheeting which we specifically told the inspector. No. This was because the last house assembly we had trapped all that moisture in the insulation- lots of mold issues.
So I understand this as water gets in where does it go. It can dry to the exterior throigh our vapor permeable assembly or to the interior ( and with a good hvac design constantly pulling moisture out of the air). I understand that I'm a little bit hesitant and rightfully so based on our last living experience. However, I really did not know that the latex paint creates any type of barrier. So that is where the hesitation comes from.
Can you explain how the wetting and drying cycles are slowed? Maybe that can alleviate that concern again.
Gavin,
I completely understand your hesitancy having had experience with poly.
During the heating season the vapour-drive is towards the exterior. Even with good control, the indoor relative humidity is going to be higher than the outside. With a good air-barrier your walls can handle that. The interior painted drywall is about 5 perms. That's a class 3 vapour-retarder, so still quite vapour-open (for comparison poly is 0.6 perms which is a class 1). Your outside will allow more drying that can get in through the interior. Plywood opens up to 20 perms when damp, and most WRBs are around 50 perms.
In the summer when you may use air-conditioning, much of the drying will be to the inside, so you don't want an interior vapour-barrier (poly) because it would be on the wrong place, and moist air in the wall cavities would condense on it as the air hit the cold interior surfaces. So that's where you want an interior vapour-retarder that hits the sweet spot for your climate and allows that drying to the inside. What you have now is exactly that. No moisture accumulation in either season.
That was an awesome explanation!! Thank you very very much.
Do you think multiple layers of paint and primer make much of a difference? We had to do it a 2nd time because the initial spackle was so poor and we had to fix everything post painting, and then paint again?
How can I find out the perm rating of Ben moore eco spec?
Your comments saved me from a coronary. Seriously, a very thankful friend.
Gavin,
Eco-spec is 100% acrylic latex
Latex primer is 6.3 perms
2 coats of latex paint on drywall 5.0 perms
Enjoy your new house!
Thank you so much!!!!
Does adding another layer of primer tenfold that perm rating? I ask that because after the spackle and painting issue, we need to redo the entire primer and paint again. Unfortunately unless there is a better way to paint over the new 2nd spackle
This was so helpful again.
Gavin,
Here are extracts from answers Martin Holladay gave to these questions:
Q. "Would an interior latex paint with low permeance create any types of water or mold problems vs. a latex paint with a higher permeance rating?"
A. No.
Q. "Would the choice in paint permeance be different in a warm humid or cold humid climate?"
A. No. If you are adding a layer of interior latex paint to a wall that already has at least two layers of paint, the permeance of the paint is fairly irrelevant. Each additional layer of paint reduces the permeance of the paint layer somewhat, but really -- vapor permeance isn't really an issue.
>"Does adding another layer of primer tenfold that perm rating? "
Nope, not really. It's closer to how adding more R value works in terms of absolute energy flow, so a sort of diminishing returns in terms of extra peformance (more vapor blocking power, in this case) with each successive coat. In theory, you never actually get to zero, either, so you would never reach an ideal "0 perm" vapor barrier regardless of how many coats of paint you apply.
Your paint layers are vapor open enough that an extra coat or two is unlikely to make any difference in a practical sense, as long as you don't use any paints specifically intended to be used as vapor barriers, which you're not using here.
BTW, I did look at the TDS (Technical Data Sheets) for the Ben Moore Eco Spec paint AND the associated primer, and neither listed any perm rating or anything at all about vapor permeance. Normally the TDS is where stuff like that would be listed (the SDS is the Safety Data Sheet, and provides information to help you select the right respirator cartridge and things like that). I suppose you could try contacting Ben Moore, but I think going with the "about 5 perms" we've been talking about here is close enough.
You can think of vapor retarders as "slows down the flow", vapor barriers as "almost stops the flow". Smart vapor retarders, including kraft paper, are pretty open as vapor retarders go, and can vary their permeance depending on moisture levels, polyethylene sheet is a pretty good vapor barrier, even if it has a few holes in it, and a metal foil layer is about as close as you can get to a perfect vapor barrier using commonly available building materials. Your assembly is a pretty good mix of cutting down on moisture getting in when it shouldn't, while still being able to let it out when it should.
Bill
Thanks everyone. Interestingly enough I reached out to ben moore and got this reply. They never tested this like for permeability, which I thought was strange. I need to rely on all of your good advice and not overthink it.
You know, we also had a 2nd layer of Tyvek that was installed as well, by mistake from the contractor. I think that will slow drying to the exterior as well. Presumably.
Gavin,
Luckily two layers of Tyvek are still so vapour-open (38 perms) that they don't make much difference in decreasing the drying of the wall. It is the plywood sheathing that determines how vapour-open the exterior is.
Two blogs which offer a comprehensive explanation of vapour-diffusion:
https://www.greenbuildingadvisor.com/article/all-about-vapor-diffusion
https://www.greenbuildingadvisor.com/article/outward-vapor-diffusion
You know, I reached out to Ben moore again and they have absolutely no perm ratings on any interior paints. They only have ratings on paint specifically designed to be a vapor barrier and those are set at .5 approximately.
This is all so fascinating and the puzzle of trying to make things work is fun and exhausting. Like for example, we have 3 full bathrooms and they are covered wall to ceiling with go board as it's completely waterproof. That actually acts as a vapor barrier because it's closed well foam on the interior. Then you ask the question, will that cause issues in the assembly in those places? Or do the benefits of this outweighs the risks of having an assembly that dries?
All the lack of ratings means here is that Ben Moore hasn't done testing on those products for vapor permeance. That doesn't mean their products don't have some amount of resistance to vapor migration. I'd assume they are similar to most other latex paints in regards to vapor permeance here.
Bill
Gavin,
Again, if you have good drying capacity to the outside - because that is the direction of vapour-drive in heating dominated climates - an interior vapour-barrier doesn't cause problems. 99% of all houses build in Canada still use interior poly. While not ideal, as long as the outside is vapour-open, and there is good air-sealing, these houses do fine. The rule of thumb is that if drying exceeds wetting then the assemblies work.