Interior foam, veneer stone, etc.

Wow, my second (plus) question! I have lurked for a long time, finding most of my questions answered by searching, but I have been having a hard time finding solid answers as my project plans get more specific.
Current home: zone 5 (Southern NH). House built circa 1970, with the associated quirks and so-so insulation level. Slab foundation with poured walls. Walkout basement with three walls about two thirds below grade. The fourth wall (I will call it the “front”) is a “half wall” with the remaining upper half being stud construction. The whole front is exposed, being where the entry door and garage door is.
The upper half of the front is covered with cedar shingles with the concrete portion exposed. By the way, there isn’t even any felt under the shingles right now, but the sheathing is doing fine (had to replace some broken shingles so I could see what’s going on). The rest of the house is aluminum siding which covers down to and including the rim joist area.
Current plan: 3 inches of rigid against the interior of the concrete wall (all sides). 2 inch eps or xps with a “cover” of 1 inch Thermax (for fire rating) on the rim joist (cut and cobble).
Near future plans: Currently, in the stud portion of the front wall (2×4), it’s FG with poly barrier. I want to replace the FG with Roxul (R15) and 1″ rigid (most likely xps), for additional R and to provide a thermal break. No other VB/VR other than the rigid.
Further future plans: Replace aluminum siding with vinyl siding (finish is so old, it’s “powdering”), with veneer stone. The veneer stone will only be on the front of the house (most likely), covering what is now exposed concrete going up the upper half wall and stopping where the current aluminum siding (to be replaced by vinyl) is.
Question 1: Just want to make sure that the near future plan of roxul between studs and xps over that (with furring and drywall) will be OK (exterior will remain shingles).
Question 2: With Further future plans of veneer stone to cover that area, will the required two layers of felt, lathing, scratch coat, then veneer stone present a problem with the Roxul/xps on the interior. I am thinking it will still allow drying to the outside?
Question 3: Since the siding will be pulled off to replace, is it plausible to then put rigid foam against the sheathing (plywood) before the siding? My concern is that there is likely poly vb in the main floor walls (as was the practice), so putting foam on the exterior of the sheathing may result in a moisture “trap” between the vb and the foam?
Question 4: If Q3 is plausible, would I have to somehow “butt” the foam/siding out somewhat or leave some kind of gap at the rim joist area to take into consideration that there’s the rigid on the inside (to allow for exterior drying)?
Thanks to all the geniuses on this site!
Wayne
GBA Detail Library
A collection of one thousand construction details organized by climate and house part
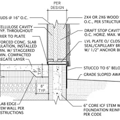
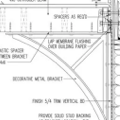
Replies
Wayne,
Question 1: "Just want to make sure that the near future plan of Roxul between studs and XPS over that (with furring and drywall) will be OK (exterior will remain shingles)."
A. Yes, that will work. For more information on this topic, see Walls With Interior Rigid Foam.
Question 2: "With further future plans of veneer stone to cover that area, will the required two layers of felt, lathing, scratch coat, then veneer stone present a problem with the Roxul/XPS on the interior. I am thinking it will still allow drying to the outside?"
A. When you install stone veneer (or manufactured stone veneer) on the exterior side of a concrete wall, I don't think you need any asphalt felt or lathing. The stone veneer can be adhered directly to the concrete with mortar or an adhesive approved by the manufacturer of the stone product.
Wayne,
Question 3: "Since the siding will be pulled off to replace, is it plausible to then put rigid foam against the sheathing (plywood) before the siding? My concern is that there is likely poly vapor barrier in the main floor walls (as was the practice), so putting foam on the exterior of the sheathing may result in a moisture trap between the vapor barrier and the foam?"
A. This question comes up frequently on GBA, and I have a standard answer. It's cut-and-paste time:
Many energy experts worry that it may not be a good idea to install exterior foam on a house with interior polyethylene. Although it would be better if the poly weren't there, the fact is that tens of thousands of Canadian homes with interior poly have been retrofitted with exterior rigid foam, and there haven't been any reports of widespread problems. According to building scientist John Straube, all indications show that these retrofits are "not so risky as most people think. These homes will probably be fine."
That said, the installation of exterior foam is not advised on any home that has suffered wet-wall problems like leaking windows, condensation in stud cavities, or mold. If you plan to install exterior foam during a siding replacement job, keep an eye out for any signs of moisture problems when stripping the old siding from the walls. Investigate any water stains on housewrap or sheathing to determine whether the existing flashing was adequate.
If there is any sheathing rot, determine the cause -- the most common cause is a flashing problem, but condensation of interior moisture is not impossible -- and correct the problem if possible. If you are unsure of the source of the moisture, hire a home performance contractor to help you solve the mystery.
If your sheathing is dry and sound, I don't think you need to worry about adding exterior foam. Adding a rainscreen gap will certainly go a long way toward avoiding future moisture problems. Of course, it's important to be meticulous with your details when you are installing your new WRB and window flashing. It's also important to keep your interior relative humidity within reasonable levels during the winter. Never use a humidifier.
To summarize, here are four caveats:
1. Be sure that your foam is thick enough to keep the wall sheathing above the dew point in winter. Read more on this topic here: Calculating the Minimum Thickness of Rigid Foam Sheathing.
2. When the siding is being removed, inspect the existing sheathing carefully for any signs of water intrusion, and correct any flashing or housewrap problems.
3. Install rainscreen strapping so that there is a ventilated gap between the new exterior foam and the siding. (This step isn't necessary when installing vinyl siding, since vinyl siding is inherently well ventilated.)
4. Keep your interior humidity under control during the winter; if the interior humidity gets too high, operate your ventilation fan more frequently.
Wayne,
Question 4: "If Q3 is plausible, would I have to somehow butt the foam/siding out somewhat or leave some kind of gap at the rim joist area to take into consideration that there's the rigid on the inside (to allow for exterior drying)?"
A. At the rim joist, you can have exterior as well as interior rigid foam without worrying about problems. Just make sure that the weather is dry and sunny on the day that you cover the exterior of the rim joist area with rigid foam.
Thank you, Martin, for the VERY thoughtful and detailed response - you are definitely a great benefit to the green building movement!
Regarding Q2, though. Yes, the veneer stone would be directly adhered to the concrete portion of the front wall (likely with a scratch coat). My potential issue is with the upper half of the wall, as for the front, the poured wall is only half-height, with the remaining wall being stud construction.
For aesthetic and logistical reasons, I want to run the veneer all the way up the entire height of the font of the basement section of the wall (at which point it will be vinyl siding for the upper level of the house.
With (from the inside - out) drywall, rigid foam, Roxul between studs, two layers of felt, lathing with scratch coat, then stone veneer, will that present any kind of drying problem. I assume not, as felt, although there are two layers, and the veneer are permeable enough, but just want to make sure.
Thanks for your valuable input!
Wayne,
Q. "With (from the inside - out) drywall, rigid foam, Roxul between studs, two layers of felt, lathing with scratch coat, then stone veneer, will that present any kind of drying problem?"
A. Your described stack-up doesn't include any exterior sheathing. Is that actually how you plan to build your wall? (Some California builders install stucco on the exterior side of the studs, without any plywood or OSB sheathing, but I don't recommend that approach.)
I'm going to assume that you plan to install OSB or plywood sheathing on the exterior side of your studs, even though you didn't mention any sheathing.
Stone veneer (or manufactured stone veneer) over OSB or plywood is one of the riskiest types of wall assemblies. In fact, thousands of homes -- perhaps tens of thousands -- with adhered manufactured stone veneer over OSB have suffered sheathing rot.
If you want to build your wall this way, it's essential to include a ventilated air gap between the stone veneer and the OSB. There are several ways to do this; most involve either a three-dimensional plastic mesh layer to provide the air gap, or vertical 1x4 strapping to create a rainscreen.
These details will be similar to the details I recommend for stucco. For more information on this topic, see To Install Stucco Right, Include an Air Gap.
Oops, yes, it would be plywood sheathing on the studs (before the felt), as that is the current sheathing on the wall. Thanks for the heads up on the risks of veneer stone. The two layers of felt (on the sheathing) then lathing and scratch coat was per manufacturers directions.