Interior Foam Insulation vs exterior

I thought I had things all figured out. I’m in central Wisconsin, Zone 6, I was planning on 2×6 construction with (2) 1″ Layers of exterior polyiso held by 3/4″ furring strips via fastenmaster’s specs. Hardieboard only requires 3/4″ screw penetration, good to go…but all the 5/4 and 4/4 trim (frieze, band corners) made by Smartwood, Miratec, Azek, Certainteed requires 1 1/4 penetration. Using vinyl siding with basic corners are about the only option which would be fine, but I would still have to foam between the furring stips and it still doesn’t provide a solution for bump-out windows with decorative trim that more or less has to be made with 4/4 boards. Exterior foam also makes cultured stone nearly impossible, and I have yet to find a manufacturer that supports exterior foam (2″ anyway.) Short of using 2×4 furring strips (still not supported by Certainteed), there are no manufacturer approved solutions.
The only solution I can come up with is to ditch exterior rigid insulation and put interior rigid insulation between the studs and drywall. But I need a little guidance.
1) Do I still need an interior vapor barrier? I was planning on dense pack cellulose between studs, what is the best way to hold the insulation in?
2) Do I still need 2″ foam or can I get away with less? I was thinking if I used 1/2″ to 1″ I could save having to us furring strips.
3) Should I still try to keep the exterior structural sheathing airtight ( ie tape seams) ? Or do I need to make it easier to dry to exterior?
Thank you,
GBA Detail Library
A collection of one thousand construction details organized by climate and house part
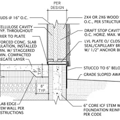
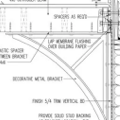
Replies
Just did some interior foam tuffr polyiso across the studs in zone 6.
1)No VB. You can use insul mesh to hold the cellulose in. Or drill holes in the foam and blow it in. I went with roxul batts.
2)I used 1". foamed the seams. I used no strapping. Major pain to find the stud when hanging the blueboard. Also lost out on the radiant R3 by omitting the airspace strapping would provide. So I'd strap it in retrospect. And run the foam behind the partitions.
3) Yes you should still try to make the plywood air tight so that it dries evenly. I used caulk from the inside.
In retrospect, I wish I'd gone with 2 layers of 2in foam on the exterior walls. Would have elliminated lots more thermal bridging. What will I lose per year in heating cost dollars due to this? Who knows..
I am in Southern Maine and have found a way to meet Certainteed's warranty as well as prevent thermal bridging. Hunter panels make a product called Nail Board or Nail Base. It is a 4x8 sheet of polyiso of your desired thickness (I have been using 2") adhered to a 7/16" OSB. , It get fastened with a factory recommended Headlok screw. From an installation stand point, you are adding foam to the exterior and re-sheathing that entire building. Certainteed has an amendment for SIP's paneling that allows you to have 1/2" of purchase, fastened minimum of every 12" that this falls under. I went to a cement fiber certification held by Certainteed just to have this method approved and they said it would be covered under warranty. From a cost standpoint a 4x8 sheet of 2" nail base costs me $46 dollars. A 2" sheet of polyiso cost me about $42 not including the OSB or Strapping. From an installation standpoint it goes up faster than strapping and you don't have to worry about nailers around doors and windows other than the jams, which you would have to deal with anyway.
The problem is not the siding, but the thicker trim. I have yet to find an approved method for 5/4 trim short of using 2x material as furring. If I do that, I either need to use 2x furring for everything or use 3/4" less foam on the corners, etc to compensate for 2x furring vs 3/4" on the corners, frieze, band etc. If I use 3/4" less foam, I run into not having enough foam to meet code. Also, it will be hard to match all the different thicknesses.
Brian,
Q. "The only solution I can come up with is to ditch exterior rigid insulation and put interior rigid insulation between the studs and drywall. Do I still need an interior vapor barrier?"
A. No.
Q. "I was planning on dense pack cellulose between studs. What is the best way to hold the insulation in?"
A. You can either install an air-permeable netting, or you can blow the insulation through holes in the drywall after the drywall has been installed. For more information, see How to Install Cellulose Insulation.
Q. "Do I still need 2 inches of foam or can I get away with less?"
A. I don't recommend your method of cutting rigid foam and inserting it between your studs. That's a fussy and time-consuming method. You would be better off using closed-cell spray polyurethane foam for a flash-and-fill installation. And yes, you still need at least 2 inches of foam.
Q. "Should I still try to keep the exterior structural sheathing airtight ( i.e., tape seams)?"
A. In my opinion, yes. It always makes sense to limit air leakage.
Q. "Or do I need to make it easier to dry to exterior?"
A. Building a wall to be deliberately leaky is a very bad approach, since leaky walls can be riskier than tight walls. If your wall leaks air, you can end up with more rather than fewer condensation problems.
Martin, I admit my wording was not the best. I plan on installing the foam ---over--- the studs, on the interior side, under the drywall. I still want to limit thermal bridging as much as possible. I believe a roof insulated in this way is still required by code to be vented, that's why I ask on the walls. I was under the impression that the foam would not need to be as thick if installed this way.
Brian,
You can install interior rigid foam if you want. If you go that route, be sure to include a ventilated air gap between your siding and your sheathing, to help your sheathing dry out in the spring after it gains moisture during the winter.
As I'm sure you know, it's harder to detail the insulation details at rim joists and partition intersections when using interior foam compared to exterior foam. But the details can be worked out if you think every step through carefully.
Brian - i think you should stick with the exterior foam. Get some 1" plywood and rip to appropriate strips to be used over the first layer of foam where you need the additional nailer....and seal with tape as if it were foam board. I would not worry about the loss of r-value in those small areas. You are 'nibbling around the edges" .... if you were able to model this loss of foam you would find it does not make much difference. You need to be practical first. And you will still have a better envelope by doing the exterior foam and not fusing with the many air sealing/insulation details required by using foam board on the interior...in my opinion.
Thanks for the advise Bruce. I spent some time considering your proposal. 1" plywood is difficult to get in my area. 2 layers of 1/2 plywood don't add up to 1". Deck boards are 1" thick, so that might work, but its pressure treated, although fastenmaster screws are rated to come in contact. I could also plane down 2x material or special order 5/4 pine boards. This is all a lot of work though. Keep in mind that this is a cottage style home. There are boxed windows, all the trim around normal windows, band boards, frieze boards. This all needs thicker material. Originally, I thought about using 1 " foam, 1/2" foam, then 1/2 plywood. The 3/4" furring strips plus the 1/2" plywood would meet the 1 1/4 requirement. With so many layers, its going to be hard to keep it all together, before getting the furring stips on.
Apologies for reviving this thread. However, I too am in zone 6 and in a 1931-era stucco home. We are renovating and adding a portion to the house over an existing attached garage. We are grandfathered in on interior side-yard setbacks but we cannot go any further into the side yard.
I assume that it would still be prudent to follow the suggestions in the "Musings of a energy nerd" post regarding foamboard. However, I am a little concerned about using stucco to wrap the new addition. I am not confident that the stucco would allow the sheathing to dry sufficiently.
Is two layers of #15 felt under stucco going to create enough of an airspace/drainage plane for a wall with interior iso and cellulose in a zone 6 (Minneapolis) Or would it be better to simply use an alternative cladding with rainscreen to ensure sheathing dryness.
Garrett,
My rule is: if you are installing stucco on a wood-framed building, you always need a ventilated air gap between the stucco and the wall sheathing.
More information here: To Install Stucco Right, Include an Air Gap.