Interior Basement Wall Advice

Hello all! Long time reader, first time poster.
I need some advice for insulating a full basement. Here’s my situation and conditions as they currently exist. Hopefully I’m not forgetting anything.
-Location is right on the border of climate zones 4&5.
-Bare concrete block walls.
-The entire basement is below grade
-R-19 fiberglass insulation between the basement and first floor with kraft faced vapor barrier on the basement side.
-On some sections of the exterior wall, the sill plate is flush with the inside top of the wall.
-On the back wall, which is about 65′ long, they must have used a thicker block around 10″. They used a 2×6 sill plate, so there’s a gap of 4″ or so from the edge of the sill plate to the inside of the wall. So…you can look down into the block wall cavities from above.
There used to be some drainage problems where water would enter the basement, but those have been fixed. The current temperature and humidity readings are 54 degrees and 67%, respectively.
There is condensation against the rim joist where there are pieces of fiberglass insulation shoved directly against them.
Here is my tentative plan:
1. Remove fiberglass from rim joists and allow to dry.
2. Install rigid foam on perimeter walls
3. Cut small strips of 1/2 rigid foam to lay flat on top of wall section to cover it up.
4. Spray 3″ of closed cell spray foam against rim joist, and spray continuously on sill plate and the top of the wall to the top of the wall boards to create a continous layer of insulation.
5. Tape the seams of the rigid foam wall areas.
How does this plan sound? Id like to use 2″ of rigid foam on the walls. I was initially going to use Dow Thermax so that I could do the installation for now without a thermal barrier, but I can’t see to source it anywhere.
Ive called a lot of suppliers, but it seems like the best prices are still Home Depot or Lowes.
Here are my options:
Dow Super Tuff R (R13)
Pactiv GreenGuard (R10)
RMax Thermasheath (R13)
I know two are Polyiso with facers, whereas the GreenGuard is XPS.
I guess ultimately my two questions are: Is my plan sound? And which foam should I be using?
Thank in advance for any advice!
GBA Detail Library
A collection of one thousand construction details organized by climate and house part
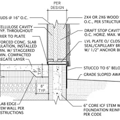
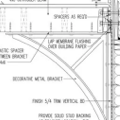
Replies
In zone 4/5 the wintertime performance of the polyiso on the above-grade section will not be a the rated-R. Going with EPS (faced or unfaced, any density) would deliver higher performance than it's rated R, and is about the same cost as polyiso per unit-R (though it's 50% thicker to acheive that R.) The performance of XPS increases at colder temps too, but unlike EPS, it loses performance over time, eventually hitting the same performance as EPS of equal density after several decades. (The labeled R for XPS is a weighted average using a 25 year anticipated lifecycle.)
In zone 5 or marine zone 4 you need about R15 to hit IRC code-min, and even at the cold edge of zone 4A/4B it's not insane to go that high:
http://publicecodes.cyberregs.com/icod/irc/2012/icod_irc_2012_11_sec002.htm
Do do the full R15 all with virgin-stock foam is rather expensive, though reclaimed goods are about 1/4-1/3 the cost. In my area (central MA) there are multiple vendors of reclaimed & factory-blemished foam board. YMMV.
But with 1.5" of EPS (R6-ish) trapped to the CMU with a 2x4 24" o.c. studwall with R13-R15 batts (unfaced or kraft, but not foil faced) you'd be there, and it's easier than mounting 3" or more of foam to the wall with 1x furring and extra-long masonry screws.
The 3" of cc polyurethane foam is a bit overkill, but works. Since 1.5" foam is the same thickness as a 2x6 foundation sill, building the ledge with 1.5" EPS and foaming over it with an inch of cc foam, and filling the rest with R13 batt would do it, and give you something useful to do with the scrap EPS of doing the foam + studwall. It would be fine to cut'n'cobble 1.5" EPS to the face of the band joist too, as long as you seal over it with a flash-inch of cc foam. The exact thickness of the spray foam not critical- it's primarily for air-tightness, but also to reduce the vapor retardency to under 3 perms, which it does even at 1/2".
With R13 on the interior of R6 EPS you have no condensation issues that would require an interior side vapor retarder in your climate- latex paint on wallboard would be plenty, and keeping the interior finish somewhat vapor open also prevents ground moisture from accumulating in the studwall. It's wise to put an inch or so of foam under the bottom plate of the studs as a capillary & thermal break to keep the bottom plate above the summertime dew point as well. It's fine to TapCon the stud plate through the foam to the slab. Since the studwall isn't structural, it doesn't need doubled up top plates or 16" o.c. spacing, and the lower the framing fraction, the higher the net performance.
When you have a choice, EPS, open cell polyurethane, and polyiso are far greener than XPS or closed cell polyurethane due to the extremely high global warming potential of the blowing agents used with closed cell polyurethane & XPS. While those products are sometimes useful for their lower vapor retardency, low vapor retardency can also be a problem, depending on the wall stackup & climate. In your case 1" of cc foam is sufficiently low-perm to limit the accumulation of moisture in the band joist over the winter, and vapor open enough that there is at least some drying toward the interior. At 3" you'd be at about 0.4 perms, which is pretty tight, the middle of the class-II vapor retardency range, but wouldn't be a problem in your proposed stackup.
Dana,
First off, thank you so much for the time that took. That's a ton of good information.
In light of your answer, I have a few more questions.
I am going to be doing steel framing. I don't think it'll be a problem going 24" OC. I was avoiding using batt insulation just to limit anything that could be a potential food source at any point down the line. But if you think it'll be fine, I'm good with that. Would Roxul be a better choice? I have yet to use it, but I like what I've read about it. It seems to have quite a few advantages over fiberglass.
As to the rigid foam component, the prices I'm finding for EPS vs Poly are closer than I was expecting. And I can't seem to find EPS in 1/2". It looks like 1" or 3/4". Here's the pricing:
1" Polyiso (R6) - $19.47
2" Polyiso (R13.1) - $30.47
1" EPS (R3.85) - $13.78
3/4" EPS (R2.89) -$11.18
Based on my calculations, I'll need 54 sheets to cover the wall area. Add another 5 sheet if I did the rim joist cavities.
So for just the walls...
Polyiso 1" @ R6 = $1,051.
Polyiso 2" @ R13.1 = $1,645.
EPS 1" @ R3.89 = $744.
EPS 1 3/4" @ R6.74 = $1347. (Install 1 sheet of 1" and 1 3/4", more work)
EPS 2" @ 7.78 = $1488. (Install 2 sheets of 1", more work)
Based on the above, what do you recommend? Based also on taking installation difficulty into account. You mentioned polyiso losing some value on the above grade portion. I should mention that there isn't much above grade. Maybe about 6". Of course, that's also what caused some of the water problems to begin with. Though in this particular case, I suppose it's a benefit.
One other question if I go with batt insulation in addition to foam. As I'm sure you know, the insulation for steel studs is designed to fit in the channel of the stud. So any offset from the foam insulation in the framing would leave an air gap between the foam and batts. In a wood installation, you could just put the batts between the studs back until it contacted the wall. Of course, I suppose you could buy the size meant for wood studs and push it back as well. That would just leave the inside channel section of the stud uninsulated.
I'm not sure what the best practice would be in the above scenario. The sheets of EPS mention leaving at least a 3/4" air gap to increase the total value, but I'm not sure how that applies in varying installation scenarios. It seems like a gap would allow that air to go up and into the joist bays above in this case. But I guess you could spray foam between the top plate and sill area, which would be required anyway for fire blocking.
Sorry for so many questions. When it comes to basements and moisture, I know I need to get it exactly right.
Thank you!
Ryan,
Not sure on your exact location or what vendors you are checking for the EPS prices - but those prices seem a bit high.
In Minneapolis (fairly moderate cost of living I believe) - EPS goes for $5-7 for 1inch and $10-14$ for 2inch at places like Menards and HomeDepot. With polyiso at $13-15 for 1inch.
Using two layers of 1" with the seams lapped by a foot from one layer to the other (both layers taped) makes for a better air seal. But that's not super critical.
I don't quite agree with Nick that the pricing is universally on the high side, assuming it's at box-store retail. Have you sought out any recliamed/used foam options? I can get pretty clean 2" fiber faced 2lb density polyiso for about $8-12/sheet (sometimes less) from multiple vendors in my area. Derated for climate that would be about R11. So, on an R/ft^2 basis it's R11 x 32'= 352 R-feet, for ~$10.00, or about 2.8 cents/R-ft^2, give or take.
The 1lbs density R13.1 foil-faced stuff would derate to about R12, for 384 R-ft^2. At $30.47 that works out to about 7.9 cents/R-ft. which is pretty typical, and about 3x the cost of reclaimed goods.
The R6/1" goods derates to about R5.7, for R5.7 x 32'= 182 R-ft^ 2, for $19.47, or 10.7 cents/ R-ft^2. A bit pricey, 8-10 cents would be more typical.
The 1lb density EPS is R3.85 x 32' = 123 R-ft^2 for $13.78. That's 11 cents/R-ft, which is VERY pricey for Type-I EPS. (7-8 cents is more typical), but maybe this stuff has foil or vinyl facers(?).
Anything over 10 cents/R-ft^2 is a bit of a gouge, particularly for 1lb EPS. (Virgin stock Type-II EPS is usually ~9-10 cents / R-ft^2, and it has 50% more polystyrene than Type-I EPS, and runs ~R4.2/inch.)
If you're going with virgin stuff from the box store and are going with 1x strapping without any fiber insulation layers, go with the 2" polyiso, which is closer to code, and cheaper R, and would meet IRC 2012 code min for zone 4 (but not zone 5).
If you're going to trap the foam to the wall with a fiber-insulated studwall, go with the 1" polyiso, and R13-R15 rock wool/fiberglass batts. The studwall + fiber layer would come in at about R9.5-10 after thermal bridging, and with R5.7 foam on the exterior it would meet IRC 2012 code-min level performance for zone 5.
Price out the lumber & fasteners & insulation for both approaches. If you buy R13 "contractor roll" kraft faced R13s the studwall approach may come in cheaper on material cost and will have the performance edge over 2" polyiso.
But if you can find reclaimed foam, the reclaimed foam + furring solution is usually cheaper than a studwall + fluff approach.
When using polyiso on a wall with a flooding history, stop the foam an inch or 3 off the slab (where ever the high-tide mark was), as a capillary break to keep it from wicking up moisture from the slab. EPS/XPS doesn't have this issue, and can come all the way down to the slab. If using a studwall approach, putting an inch of EPS under the bottom plate of the studwall mitigates against high moisture levels in the bottom plate board too.