Insulative system cost/benefit question

I’ll start by saying, this is my first ever post to GBA and want to express my gratitude to the building science enthusiasts and experts that maintain this site and answer questions.
I am a licensed builder in the Panhandle of Florida and have a tiny home cottage build that I’m to be starting in January. My first new build since getting my license in June. The client is budget conscious and doesn’t really see the benefit in putting extra money into a perfectly built passive structure so I’m attempting to put together the best cost/benefit plan for the envelope possible.
My question is basically; would it be better to spend extra money on a higher grade insulation (open cell foam) for the envelope and have a standard sheathing detail (OSB and Homewrap). OR, a cheaper wall insulation such as kraft faced fiberglass and install ZIP-R 15/16 so there’s at least a minimal attempt to thermally break the system? Any advice is appreciated
GBA Detail Library
A collection of one thousand construction details organized by climate and house part
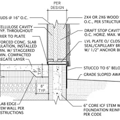
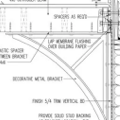
Replies
Hello SandRock,
GBA has an article about a question very similar to yours. Their angle is whether you should focus on insulation or on air sealing. Air sealing, as you likely know, is critical so we can control the air flow in and out of the strucuture with an HRV or ERV.
You can read the article but this one line sums it up: "If you have to choose one, go with air-sealing"
https://www.greenbuildingadvisor.com/article/whats-more-important-air-sealing-or-insulation
If fiberglass and ZIP are less costly, then I would choose that option and use the ZIP tapes (designed to stick to ZIP sheeting) to air seal the very best that you can. From what I know of open cell spray foam, it can trap a lot of water vapor and it is slow to release that water.
If you are in florida then you would want a good vapour retarder on the exterior. I am not sure that the craft paper (facing the interior?) on the insulation would be a good idea in a hot humid climate given that you would want the walls to dry towards the interior. Again, most of the condensation issues result from air leakage into the assembly. This is again another reason to seal that ZIP sheeting real tight.
https://www.greenbuildingadvisor.com/article/understanding-a-wall-assemblys-drying-potential
Hope this helps.
SandRock,
Besides Zip R probably being unavailable in your area, it's certain to cost probably 5X what a standard typar/osb/fiberglass wall assembly would cost. If it were up to me, I'd spend whatever money that could be considered extra on adding a rain screen to the siding, if not brick veneer. With even a small gap of 3/8", which you can get from plywood rips, you'll really enhance that wall assembly. Add in a little extra for taping the seams of the OSB for your air barrier, and you'll be doing them a much greater service than any production builder would even dream of.
It's easy to get caught up in the high performance wall assemblies, but if you've got to start somewhere to get enough houses under your belt to build confidence with other consumers, I'd start small.
Good luck!
Edit:
Though not directly related to your question, I'd grab a copy of the 2021 IRC and start with the prescriptive requirements in there, as opposed to whatever code version your locality enforces, if at all. That way you've got something to provide credence to whatever your proposals are.
Kyle, would SandRock not be better off using Plywood if ZIP is not available? This GBA article from 2021 speaks about recent building science studies examining the reliability of OSB as an air barrier. In know that there has been different points of view on OSB in the past but the actual recent studies are providing some evidence to consider. What are your thoughts?
https://www.greenbuildingadvisor.com/article/study-finds-osb-sheathing-not-a-reliable-air-barrier
Hugh,
If you scroll down through the comment section, you'll see some of my thoughts on that article, which I'll summarize with a few statements.
On this level of build, the amount of air leakage through the OSB panels, if any, is likely to be exceeded by air leakage due to other penetrations. I don't accept that the air leakage in that artcle/experiment was as high as Huber suggested. This is minimized further by the secondary WRB tight up to the sheathing.
In other words, air would need to face a pressure differential that is high enough to (2). force its way through the osb, and (2) travel at most h/2 to the edge of the house wrap and escape. I don't know what that pressure value is, but I have cut enough OSB to know that it's essentially a solid matrix of wood and adhesive. There have been a sufficient amount of < ACH 1.0 houses built with OSB for me to conclude that the air leakage through the medium itself isn't large enough to be concerned with.
Pragmatically, any holes that small will probably plug themselves up over time too.
If you tell us your county we can give more detailed advice, but looking at the Energy Star reference (https://www.energystar.gov/ia/partners/bldrs_lenders_raters/downloads/County%20Level%20Design%20Temperature%20Reference%20Guide%20-%202015-06-24.pdf ) it seems that most of Florida has a summer design temperature in the mid-90's and a winter design temperature in the mid-30's. It's a cooling-dominant climate but not as much as I would have thought.
In terms of cost-effectiveness, it's really educational to use an energy modeling program like BEopt where you can put in different assemblies and see how they perform. A big part of your business is going to be knowing what things cost, so it's a good thought experiment to change up materials and see how it affects the construction cost and the energy usage. Another consideration is the size of the HVAC system, with more insulation you can downsize and save some money there. An intangible benefit is that tight houses are more comfortable, quieter and cleaner. However at a certain tightness level your local code may require supplemental ventilation, which would be an expense that might not be worth it.
In cooling-dominant climates you have to be extra careful about moisture management. This is an area where you can distinguish yourself as a builder because a lot of people in the business don't understand it. Much more important than the insulation material is the set of construction techniques you choose. Moisture management means keeping warm humid air out of your walls, which means really good exterior air barriers and vapor barriers. It also means really good detailing to keep rainwater out. Your walls will dry to the interior, with the moisture removed by the HVAC equipment, which means that your interiors have to be vapor open -- no vapor barrier on the insulation, just drywall and latex paint. Joe Lstiburek has a few articles where he talks about how impermeable finishes like vinyl tile, wallpaper and even large cabinets or mirrors can prevent walls from breathing to the interior and lead to mold damage.
Note that this is the opposite of how walls are built in most of the USA. In most places the vapor barrier is on the inside and the wall is allowed to dry to the exterior.
Thank you everyone for your insight. I failed to mention my emphasis for air sealing which is of vital importance. Speaking with my rep at builders first source he tells me that the cost difference between OSB and zip isn’t that great with the current prices of OSB in my area (seems strange since zip is an OSB product) but I’m considering Zip-R (15/16) with blown in fiberglass now. Paying close attention to air sealing the commonly overlooked areas such as at the sill plate and top plates with a tight zip system seems to be the best approach. I wouldn’t call myself an expert in building science and hadn’t considered the effect of the Kraft paper on the systems ability to dry to the inside and I hope the blown fiberglass can help in that regard.
Building material prices vary a lot by region, now so more than ever, so it's hard to make generalizations. But I associate exterior continuous insulation with cold climates where you need to keep the wall interior warm enough to prevent insulation, and you need lots of insulation and continuous exterior allows you to achieve that without making the wall so thick. I don't think of it as cost-effective in warm climates.
I think of Zip-R as a specialty product for when you need continuous exterior insulation, and you also need a continuous nailing surface for the siding. The material is more expensive than other approaches but it saves labor.