Insulation/Ventilation plan of attack – 4a zone – expert opinion coveted!

Hi All,
I’m hoping I can attract Martin and other experts to this thread, really respect and value his and everyone’s opinions in this community. My GC and Architect are really leaving this up to me, neither are really willing to engage, and I’m trying to make the best of a pretty difficult/tough situation (another story). We are a few weeks away from when insulation decisions need to be made, so here goes, does this sound like total chaos, or should I be ok with this plan of attack.
Caveats: I’m scared $#itless of spray foam, I do have it in my crawlspace/basement, and it worked out just fine after a lot of anxiety, but I have trust issues I think with some of the “pros” i’ve worked with, and have nightmares of a bad installation, being left with a situation where my new areas stink of off gassing foam forever, and my family and wallet hates me 🙂 .
3 car garage being converted to family room, Mansard style roof that is “raised” so a roughly 10+ foot flat ceiling and sides that mirror the steep mansard shape. HVAC ducts need to unfortunately go above ceiling joists, they will be R8 insulated, air handler in conditioned mudroom next door so no issues there, and roof rafters are only 2-3″ deep. Soffits run continuously around the entire structure, no ridge vents or vents in the attic! Veneer brick exterior, 1″ gap/cavity between interior framing, flashing and weep holes, 2×6 frames on inside.
Plan: Air seal ALL walls/ceiling etc.
Walls: R21 faced HD fiberglass walls (paper faces in).
Attic/Ceiling: Install 3 box vents near ridge (ridge isn’t long enough). I don’t have deep enough rafters for insulation there, so plan is to lay 2″ rigid foam on top of ceiling joists, have HVAC ducts and trunks sit on that. Then sprayfoam 2-3″ of closed-cell spray foam just directly and around trunks and ducts to encapsulate it fully. That gives me roughly R20-25 depending on how thick I go including the R8 duct wrap – I know I said I dont like spray foam but I can live with just encapsulating the ducts and keeping a vented attic for potential smells. If I don’t spray foam I was going to have them build a box around ducts and trunk in rigid foam but I don’t know how efficient that is? For ceiling I was going to use R49 fiberglass between ceiling joists (faced paper down?) And then finally to help with some of the thermal bridging, continue that 2″ rigid foam being laid on top of ceiling joists that HVAC sit on and air seal it all, basically giving a gross R49 + R10 if I did XPS. Is 2-3″ of rigid foam enough for ducts or should I lay loose fiberglass over all of the ducts on top? Mansard style roof, so wanted to have the guys continue 2″ rigid foam down the sides/angle to outline the ceiling framing which also gives me additional R10, plus creates an air sealed type cavity to allow soffits to push air above this whole thing, allowing roof deck and all to ventilate.
New garage being built next to existing garage, 2nd floor will have cathedral like framing, but essentially no attic except for a shallow gap towards the center of the room as the ceilings flatten out about 9 feet high (29×20 interior space, so flat roof area is maybe 20×15 w/ 7′ side walls and pitched towards center. Rafters are 2×12, soffits, and again 3 roof vents will be installed towards ridge/top spaced out.
Plan: Air seal ALL walls/ceiling etc.
First floor –
Walls: R21 faced HD fiberglass walls (paper faces in).
Ceiling:R49 faced fiberglass, unless should I just use roxul/sound insulation? rim joists, cut/cobble 2″ xps rigid foam.
2nd floor –
Walls: R21 faced HD fiberglass walls (paper faces in).
Attic/Ceiling: I’d like to have my guys again use 1.5″ or 2″ rigid foam to create baffles all the way from soffits to ridge area directly against the roof rafters. Here I think Martin has recommended EPS, but it looks like I can source just faced EPS, so is it better to just use XPS here as a backup plan? R49 fiberglass in rafters below these rigid foam baffles/cavity, drywall. the center of the attic/ceiling flattens out, so there is a gap between ceiling joists and roof/rafters, so if I’m doing rigid foam to create baffles/vent channel up towards the ridge i’d like to continue that around the top of the ceiling joists. within the center of that space will be a framed out box for a 4way min split, and I’d have this 2″ rigid cavity above and surrounding it.
Apologies for the long post, I find that no one actually wants to plan this out with me or give me honestly any sound advice, my architect is probably closer to 100 and not interested in building science or best practices, he just says fiberglass insulation in ceiling joists and bare minimum details on the plan. My GC says architect needs to give details on this, or “i’ll do whatever you tell me to do” instead of actually giving a sound plan. If the overall feedback is you need to hire a specialist to come in and provide a plan, please let me know what type of specialist that is.
thanks guys!
first pic existing 3 car garage being converted to living
2nd is new 2nd floor of new garage- circled red polls are just temp
GBA Detail Library
A collection of one thousand construction details organized by climate and house part
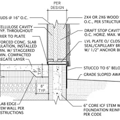
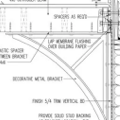
Replies
I see no problem with R21 faced fiberglass batts in the walls everywhere, except that in CZ4 and higher, you need R5 continuous on the exterior too. Facing goes to the "warm in winter" side in heating dominated climates, so you're correct facing the paper facer towards the interior. I would be sure to air seal the walls prior to insulating (caulk and canned foam), and I'd detail all the interior drywall airtight too for some added insurance. It doesn't hurt to double up on air barriers.
Assuming this is a normal "stacked" two story home, why are you insulating the first floor ceiling? Is this just to help dampen sound between floors? You should use NON faced insulation here, and mineral wool will perform SLIGHTLY better than fiberglass for sound, but probably not enough to justify the much higher cost. I'd probably use unfaced R19 batts here, maybe R30. If this is just for sound, there is no need to full fill the cavities between the joists. You also don't need to worry about any codes for R values, since you're not insulating between conditioned inside spaces and the outdoors.
For the cathedral ceiling areas, you need to be very careful about venting, otherwise you need to go unvented with spray foam. If you have sufficient rafter depth to allow for at least code minimum levels of insulation, you can avoid the need for spray foam here. You don't need rigid foam for the baffles -- that only adds cost. I would use 1/4" waferboard for the baffles, tacked onto furring strips that will "frame out" the vent channels. That's quick, easy, and relatively cheap. You actually WANT some vapor migration upwards through the baffles into the vent channels here, you do NOT want a vapor barrier material. I see no issue using fiberglass batts under the vent channels. Depending on overall depth and target R values, I would consider putting a layer of foil faced polyiso UNDER the rafters, with the seams taped to form and air and vapor barrier. Build this way, you can use unfaced batts between the polyiso and the baffles below the vent channels. That might save you a bit of money.
I do not like the idea of using rigid foam above the floor joists in the attic. I think this opens you up to lots of air leaks, and adds a lot of cost for no real benefit. I would not use batts here, either, since you appear to have a good size space above the floor joists, even if it's not really a full attic. I would use blown cellulose in all of the "attic" spaces, and you can bury the ducts in that. I would insulate the ductwork though, and I'd air seal the ductwork (ideally using mastic) prior to insulating. Commercial standard practice is to insulate the ducts with rigid fiberglass panels, with seams taped. The insulation is normally secured to the ductwork by tack welded nail-like fasteners. Blown cellulose is the cheapest way to insulate these attic floors, and it's one of the best options too from both a performance and "greeness" perspective.
I would NOT use XPS against the rim joists. I would use either fiber faced polyiso or EPS. EPS will be cheaper. You can use some mineral wool to get the fire protection needed plus add a little R value. A combination of 2" EPS and Safe'n'Sound mineral wool works pretty well. Seal the EPS in place using canned foam around the perimeter of each piese. I prefer Loctite's TiteFoam for this over Greatstuff.
I think you can avoid using sprayfoam anywhere if you're careful with your details here. I would airseal everything with canned foam and caulk, and I'd detail all drywall airtight too.
Bill
Bill - thanks so much for replying, going in order of your comments:
- Double checked with my building department, they didn't adopt the more stringent r5 continuous requirement on exterior so i'm good with the R21 HD batts ( going to have them airseal everything completely top down the entire envelope beforehand .
- Re: ceiling above garage and 2nd floor room, Insulating in ceiling was just for sound as you said, so want to air seal that space and provide some type of insulation (though the garage will be heated/cooled w/ its own mini split, but likely just heated to 50-60 max). Noted on your recommendations, i'll use unfaced and maybe an R30 high density but will compare that to something like Roxul Safe n Sound for there.
- Regarding cathedral type ceiling (i'm calling it this because no added depth between roof deck /rafters/drywall). I have 2x12" rafters, and if I need R49, how do I accomplish that if I need at least 1" space for baffles to go from soffit to ridge vent? I really didn't want to encapsulate the space which would be obviously much easier at this point by sprayfoaming closed cell directly against the roof deck/rafters and jsut not having them install sofits or ridge vents, but is that really my only option here? I figured using rigid foam as baffles would give me a little more added R, and then i'd have to make do with stuffing as much fiberglass in there to fit (9 or 10 inches cavity). This i'm still confused here..
- Existing garage to family room - Yes there is some room but not a tremendous amount. The thing is I have 2x12 ceiling joists there, so if I did cellulose don't I need to first have them do drywall, then create a hatch to get up there and fill those joists with 12" just to get even with the top of the joists where my ducts are going to be sitting, then i'd have to go another at least 8+" above that just to get level with where the ducts will be sitting on top of the joists (probably 14" then). Or are you proposing I have them add some type of subfloor/osb on top of the floor joists where HVAC ducts are, and just blow 14-16" of cellulose (baffles on side to allow air from soffits to get over)? I'd then have nothing in between my floor joists, so do I fill those with insulation. Other question is if he creates a hatch for cellulose, how do we install that gap where hatch is once they close it up? The issue with all of this is these damn HVAC ducts, but doesn't aesthetically make sense to run them anywhere else, so I need at least those up there.
thanks again!
re: "using rigid foam as baffles would give me a little more added R value"
A little tip - you can buy 1" foil-faced, poly-iso board & make a cut/score the board in such a way that the foil face can stay attached on one side. Then flip that over & it becomes the 1" "standoff" you need to become the baffle space for soffit to ridge vent.
I would then buy the 1 component closed cell foam w/the fan tip & either just seal all of the edges of the baffle or possibly buy the 2 component foam & do a "flash & batt" type of application ...
https://sprayman.co/products/sprayman-insulation-spray-foam
former spray/inject foam contractor VT
Thanks for this! I saw a YouTube vid on this idea and it’s a really cool innovative way to create baffles.
I'm a big fan of exterior rigid foam, so I'd consider the R5 (or more!) on the exterior even if it's not requried. It will greatly help with thermal bridging of the studs, and give you a better performing wall. Up to 1" (R6 if using polyiso) doesn't really complicate trim any. Up to 2" (R13 if using polyiso) is usually not too difficult to work with. Over 2" and you get into the "thick" territory, which does complicate some exterior details. It's up to you though if your muncipality doesn't required anything at all.
For that cathedral type ceiling, yes, using rigid foam for the baffles helps, but not much since you have so far you need to go in terms of getting to R49. You have 11.25" of space to work with with a 2x12. I like to use furring strips to frame out the baffle, which makes a 1.5" vent channel. 1" is code minimum, but it's really better to have more than that, especially for a very long vent channel or a low pitch roof. Using 1.5" furring strips is easy, but you could rip 1" strips of plywood too. Using 1/4" waferboard to form the baffle then leaves 9.5". You could stuff a 10" thick R30 fiberglass batt in there and still be pretty close to R30. You have to get another R19 worth of insulation, which complicates things. The rigid foam will do more for you on the interior, but you'd need 3" thick polyiso to hit R19, and that won't be the easiest to work with due to the need for long fasteners. Another option is to furr things out with perpindicular strapping so that you have enough room for a layer of batts going at 90 degrees to the rafters, then put in R13 batts (if using 2x4s to furr things out), and 1" polyiso on the interior behind the drywall. That gives you R30 in the main cavity + R13 in the furred out area + R6 for the polyiso = R49 total, and it should perform pretty well.
You could also put all your insulation in as batts, in which case you'd furr things out to fit R19 batts (6.25" thick), but you now have an oddball thickness of batt to work with. In that case, I'd probaly use 2x6s as furring, compress the R19 batt a bit, which will slightly reduce the R value, then use 1/2" polyiso on the interior, which will get you up to a tiny bit over R49 when you're done. Either way works.
If you don't want to vent the roof, closed cell spray foam is your safest option. IMHO, it's really your only option for an unvented assembly.
For the garage, you'd need a way to get up there to install the insulation. A hatch somewhere would be the usual option, and remember that that hatch could be on the exterior somewhere too -- it doesn't have to go inside. It's possible to do this with batts too, but it'll be more labor intensive. It's also possible to put in an insulation support "floor" that is non-structural. I've used that same 1/4" waferboard (I like it because it's cheap) and furring strips to build insulation support "flooring" between attic floor joists. I usually do this when I am concerned that adding insulation might cause the ceiling drywall to bow, but you could also do it to provide a way to insulate prior to drywall going up.
Bill
I’m unfortunately too late for the exterior insulation. Poor planning on my part, though wish the GC or architect would have cared to raise or flag it.
Ugh I’m thinking spray foam may really be the only “right” option for this cathedral space. I need to start seeing if I can find something that has the least chance of a potential bad install job. It’s pretty sad that I don’t trust my GC and whoever his subs are to do this, but maybe I’ll find out first what they use and go from there. I think the newer closed cell water blown stuff seems more safe, but the thought of a failed job and whole situation with this guy on that spells DISASTER :).
Good call on the hatch being exterior, they had to cut into the existing ceiling /roof to connect the mud room so maybe I have them leave that open as an exit point. - thanks again for your help.
You want to ask about "HFO" blown spray foams, which are a bit safer than the old fashioned stuff, but perform a bit better than the water blown stuff. Honeywell has a good document on this here:
https://prod-edam.honeywell.com/content/dam/honeywell-edam/pmt/oneam/en-us/blowing-agents/documents/pmt-am-solstice-lba-enovate245fa-cost-effective-solutions-brochure.pdf?download=false
Your main issue with a bad install would be the A and B components not getting mixed right. Too much of one and you get crumbly foam. Too much of the other and you get gooey foam (the really nasty way an installation can "fail" is the "gooey" way). The best way to avoid this is to get an EXPERIENCED spray foam crew. The guys I use locally where I am are very OCD about their mix, and constantly adjust things throughout the job based on what they see coming out of the gun, and what the ambient temperature is. I've never had even close to a bad install with these guys. You do NOT want to be someone's very first spray foam job...
I usually recommend you find one good contractor that you like, then get referrals from that contractor. Contractors tend to like to work with other contractors that are like minded, so someone who likes to do quality work, for example, tends to like to work with other crews who also like to do quality work. The first good crew gets you "in the door", then they can recommend other good crews. I never open bid any work for this reason -- I always use people I know, so I can trust their work. Unfortunately this isn't usually an option for people outside of the industry, because they don't have enough contact with the trades to know where to start, so you're in a fairly common situation among people attempting to build high performance structures.
Bill
The other issue, besides proper component mixture, is making sure the passes the sprayer makes is properly calibrated to make sure it is not too thick!
Putting too much foam on (too thick) per pass can create internal voids via shrinkage as the curing process is an exothermic reaction
You can have a “burn out” situation that can create voids
Thanks guys! 1 last one, I have areas of flat roof over new mudroom that have EDFM, again not attic just 2x12 joists. Right now they have joists and plywood on top, haven’t done anything yet, but if they kept going they said they would seal plywood? Then 1/2” fiberboard, seal it(?) then epdm membrane. I’m seeing I should definitely add a layer of polyiso, and fully seal that before the membrane, so proposing layers are:
EPDM
fiberboard
1/2” Polly’s
Plywood
Joists
R49 fiberglass by furring down or 3” closed cell/flash and bat
Drywall
The 1/2” polyiso gives me enough for moisture proof? I know I need to get to r49 but I’m told I don’t have the 2-3” I need to get r15-20 up top so need to do majority of insulation below - working with what I have!!
Standard commerical construction puts polyiso over the roof deck, and under the membrane, with a protective layer as you mentioned. I would use a lot thicker than 1/2" polyiso though. Ideally try for one of the stackups mentioned on here for roofs in your climate zone, which will put a big chunk of the total R value in the polyiso. I'm more familiar with the Northern climate zones, where we usually shoot for around 60/40 exterior to interior, but in your climate zone les is probably safe, 50/50, maybe even less. That would mean, for R49, you'd want around 4" of polyiso above the plywood, and then a little less than R30 inside. You might be able to go a little less on polyiso. I know one of the other members on here has more experience than I do with this sort of thing in the more Southern CZs, so he'll hopefully comment here on what is a good and safe ratio for you.
If you go with less, you are at more risk of condensation on the cold underside of the plywood. Remember that this is an UNVENTED assembly from your description, so you have to be much more careful with moisture control and insulating methods.
Bill
Just confirmed with contractor I can fit 2” of foam, that gets me 13.1, i can then use r38 fiberglass which gets me over r50, is that ok?
Better yet can I just order 1” and 2” and stagger it? I can’t find 3” but I can order 1” and 2” poly from Home Depot - it’s faced on both sides I hope that’s acceptable? Tape first layer and then stagger the next, then I’ve got 19.1 R , plus r30 batts
Yes, you can stack different sheets to get to the target thickness you want, just be sure to stagger the seams. Any commerical roofing supplier should be able to get the thicker stuff for you, but either way works.
BTW, you should't abbreviate "polyiso" (which is already a shortened name for polyisocyanurate) as "poly", because "poly" usually refers to polyethylene sheet like you'd use for a vapor barrier. Best to avoid confusion here.
Bill