Insulation under floor

I was hoping to get some input on detailing for insulation under a slab. I am constructing a ranch house near Austin, Texas.
The house foundation has been designed to be a monolithic slab. Large parts of the slab will be used as a polished concrete floor. There are parts of the house, where the outside ground is sloping away, where 3-5′ of concrete foundation will be showing. I am concerned this will be an area of loss of a lot of heat in the summertime and would like to insulate the floor in these areas.
I do not want to place any outside rigid foam insulation due to termite concern. It was suggested to me to place rigid foam directly under another layer of concrete. Can someone please advise me about this idea and what the details would be: depth of recess within original slab, thickness and type of optimal insulation, optimal thickness of the top concrete floor and reinforcement needed for it?
Thank you.
GBA Detail Library
A collection of one thousand construction details organized by climate and house part
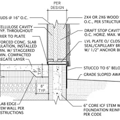
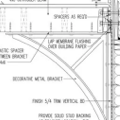
Replies
Hi Deerefan (be great to have a name for the GBA Q&A community to use for you) -
GBA has drawings for slab construction for different climates (https://www.greenbuildingadvisor.com/detail-library/detail-drawings-foundation-floor-connections).
As always, the key is to completely pull the foundation assembly into the building (with exterior rigid insulation on the vertical surfaces of the foundation perimeter) or to completely push the foundation assembly out.
With monolithic slabs, it's very hard to push the slab out of the building but also challenging to protect the rigid insulation on the exterior of the slab.
I suggest you move to a high density rigid mineral or rockwool board with a cementitious coverboard. This leads to challenging planar issues affecting just how you locate your exterior walls. This is a good job for a high performance, building-science-minded local architect. Check the GBA bulletin board.
Peter
Peter,
Thank you for your reply. I prefer to use my nickname online, I hope that is understandable.
I reviewed the details of the drawings. My preference is not to put any insulation on the outside because of: termite and other insect issues, long-term durability, appearance not matching the remainder of the house and deteriorating over time.
So, if my direction would be to place insulation on the inside, could it be done similarly to an insulated slab on grade in a stem wall foundation? That is, creating a recess in the monolithic slab with insulation at the base and around the perimeter. If so, how deep would the recess need to be, how thick would the insulation need to be, how thick would the concrete need to be?
As a second part to the question, why do you recommend rock wool board? I thought XPS rigid foam was the best way to go here? Thank you again.
>"As a second part to the question, why do you recommend rock wool board? I thought XPS rigid foam was the best way to go here?"
Termites and ants seem to love tunneling in polystyrene insulation. Dense rock wool, not so much.
Also, XPS is one of the least green insulating materials in common use in the US, due to it's high polymer weight per R, but more significantly the HFC blowing agents used (banned under the Kigali Amendment to the Montreal Protocol.) As the HFCs diffuse out over decades XPS eventually hits the same performance level of EPS of similar density. In the fine print the major manufacturers only warranty it to 90% of labeled R-value- R10 is really R9-ish, but over the very long haul it's really R8.5-ish. Rock wool doesn't have that issue.
Think you should look into doing a stem wall, and insulating on the inside of that, for the walls and slab.
The foundation has been designed to be a monolithic slab, so changing would be a major and expensive undertaking at this point.
Let me take a step back and ask a question. If the foundation wall is taller and more exposed, does that make the concrete floor colder in winter, given that the thickness of the bridging area to the 4" concrete slab floor is the same? If is, is this a practical or theoretical only difference? Thank you.
Some sort of slab-edge insulation is going to be necessary for coldest-day comfort whether it's a grade beam or stem wall. A course of 6" or wider low-density aerated autoclaved concrete block extending down to even a foot below grade would be enough to make a difference in Austin.
Dana,
How can that be applied to the outside of the foundation wall and still be inline with wall sheathing above?
I recommend you pour an initial footing where your elevated grade beam will land. Form your foundation Typ. but for your elevated grade beam you can course ICF blocks around the rear perimeter, embed steel as TYP, and monolithically pour with finished floor and perimeter and interior beams. Waterproof your ICF blocks with a poly wall or other sprayed membrane and then lathe and stucco as a typ. underpinning of that span.
For your question to Mr. Dorsett's response, it all depends on your cladding plans. The only way for this to have a seamless finish is to either have an overhang in the concrete floor (per engineering) or use it as a brick/ stone lug.
LBR_Homes,
Thank you for the response. Would the ICF blocks be on the outside of the foundation? If so, is the termite issue no different then putting rigid foam with cladding to insulate the foundation wall there?
Second question: Would the wall and thus roof load then rest on the ICF part of the foundation rather then the perimeter grade beam? Does this not change loads, etc.?
Thank you.
Deerefan,
The ICF blocks act as the forms for the structural concrete, and turn into the insulator upon curing. You've got a lot of different options for termite prevention/ mitigation. 6" to 12" bed 16 grit basalt, crushed granite, etc. Figuring this out will be determined by how the engineer designs the slab. Whether the ICF forms are above grade on a keyed lug or below with a mono pour.
Best,
After much reading on the website and thought, here is my proposed solution (please see diagram): 6" recess in the slab, 2" XPS horizontal and vertical foam insulation, 4" concrete floor on top.
My questions:
1. What is a better way of addressing the vertical part of foam insulation: covering it with base plate (left) or beveling the foam and covering with concrete(right)? 2 concerns regarding beveling (as suggested by Martin Halladay in an article): how effective of an insulator is the beveled edge and what are the chances of the thinner concrete cracking over time?
2. I plan on using this insulation only 4' around perimeter to maintain the advantages of good soil temperature year round. Thoughts?
3. Polyethylene film will be used under the slab, any need to use it above this foam as well?
4. Is metal mesh needed in the top 4" concrete floor? Joe Lstiburek does not seem to think so in his article on slab insulation, I haven't seen a concrete slab without reinforcement before...?
5. For wood floors in the house, would you recommend doing this insulation as well or not. It seems more tricky as it is harder to keep it around the perimeter only and used everywhere we may use the advantage of cooling effect of the central slab in the summertime. If you do recommend it, would it be acceptable to facilitate the design by not using the vertical insulation part?
Please let me know your thoughts on this approach. Thank you.
Somehow, the image did not get attached. Will try again.
Can someone please tell me why the image will not attach? Its a jpg and 2.5mb. Thanks.
Deere Fan,
E-mail me the image and I'll post it for you. My e-mail address is martin [at] greenbuildingadvisor [dot] com.
>"A course of 6" or wider low-density aerated autoclaved concrete block extending down to even a foot below grade would be enough to make a difference in Austin."
---------
>"How can that be applied to the outside of the foundation wall and still be inline with wall sheathing above?"
Aerated autoclaved concrete (AAC) is structural, just like concrete masonry units "cinder block". As long as it's supported by proper footing it can be directy under the wall.
>2" XPS horizontal and vertical foam insulation, 4" concrete floor on top.
If going that route use EPS instead (most ICFs are made of Type-II EPS) which has a stable R value over time (unlike XPS), and much lower environmental damage. Termites will tunnel in either of those insulation types, but not AAC.
Another type of termite-proof structural/semistructural insulation is Foamglas:
https://www.generalinsulation.com/products/insulation-products/insulation-types/foamglas-insulation/block-2/
https://www.greenbuildingadvisor.com/article/foamglas-my-new-favorite-insulation-material
At 2.5" Foamglas has about the same R-value as 2" of EPS or fully depleted XPS. At 3" it has a slightly higher R-value than the labeled R value of 2" XPS. It's not as structural as AAC, but it's many times more structural than polystryene. You could build the entire wall out of AAC if you wanted to (I've seen 3 story buildings in Europe built with AAC), but you'd have to have an engineer do the math when installing Foamglas under load bearing wall.
Martin, I have emailed you the diagram, I appreciate you posting it.
Dana, As you will see in the diagram all of the slab insulation (horizontal and vertical) is within the slab itself. I do not want to take any risk of having a termite problem given our location. I appreciate you mentioning other options for the foundation but I am afraid we are beyond that point. Our structural engineered designed a monolithic slab and I have to problem solve within these confines.
As I had posted previously, we have had a less than ideal experience with the architect, engineer team which is why I am having to do all of the work which I feel was someone else's responsibility. The engineer was never interested in answering any of the questions that I asked. This is going to be our forever home, however, and I am determined to make it as correct as possible. I really appreciate all of the help from this forum.
Simply replacing the XPS with Foamglas or EPS works in that diagram.
A 4" slab on top of a monolithic slab seems like a lot of extra concrete. The subsoil temperatures in Austin are nearly ideal ~70F, and insulating between the floor slab and that ideal subsoil thermal mass probably increases both heating and cooling energy use.
Moving the cantilevered sill plates 2" to cantilever the exterior rather than the interior and applying 2" of exterior Foamglas down to a foot or so below grade would likely be a lower energy use/higher comfort solution, and you could skip the horizontal insulation and second slab, use the monolithic slab as the finish floor slab.
In the current design there is a ~R 3 thermal bridge to the outdoors from the interior edge of the sill plate through the concrete. Putting 2" of Foamglas on the exterior would raise that to the R-7, about the same R value of the sill plate itself.
Dana,
Thank you for the suggestion. From my reading, foam glass is not available on a residential level in the US.
I understand that a second slab means extra cost, but this would only be in areas of the house with tall exposed foundation and my estimated costs are really quite reasonable, everything considered. My plan was not to insulate the entire slab in these areas but only 4' around the perimeter, where the cold or heat from the outside would be felt the most. The remainder would be in contact with the building pad. I didn't show this in my diagram, but the sill plate will be covered with rigid foam insulation.
As you can see, I am really not keen on perimeter slab insulation due to the potential for termite entry. Given this, do you feel the my proposed plan is worth it, or should I abandon it altogether and insulate the interior of the slab at all?
Just wondering if anyone could help with the last post. Is it worth insulating the perimeter 4' of the slab underneath as I described in the diagram or is it too much effort for the benefit? We are currently working on the trench work for the foundation so I really need to make a decision soon. Thanks.