Insulation under basement concrete slab.

I am building an energy efficient home in Southern Maine. I am planning on using ICF’s and a spray foam insulation in the wooden frame stick built structure. Would it be cost effective to install styrofoam insulation under the basement slab, and if so how thick?
GBA Detail Library
A collection of one thousand construction details organized by climate and house part
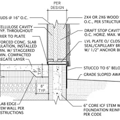
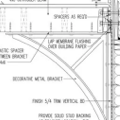
Replies
Dana,
In your climate zone, I would strongly recommend that you install at least 2 inches of rigid foam (XPS or high-density EPS) under your basement slab.
There are two reasons for this:
1. The insulation will lower your energy bills.
2. The insulation will keep your slab warmer, making it less likely that condensation will form on the slab during the summer. A warmer slab means a more comfortable (and dryer) basement, making it easier for you to install carpeting if you ever want to.
"Cost-effectiveness" is hard to determine, since there are so many variables (including what fuel you are using to heat your house, and whether energy prices rise in the future.) In this case, don't worry about cost effectiveness -- just install the foam. After all, it will be hard to retrofit it later if you ever change your mind.
Martin is correct under slab insulation is crucial. How thick really depends on what your goal is, which some energy modeling will give you the answer.
A couple of comments/questions though. XPS is said to have more green house potential so, if that is one of your concerns, you may want to go with EPS. EPS also has high embody energy but I haven't found an alternative that is cost effective yet. Foam glass is something but it is about 2x as expensive.
Martin, I've read contradicting opinions about rigid foam losing R-value as it absorbs water? I've read arguments on behalf of XPS and EPS on this matter. I am leaning more toward EPS absorbing less water and loose less r-value. Interested in your take on this.
Martin also mention moisture. Your vapor barrier under the slab is very important too. I think conventional homes use a 6 mil. We used a 20 mil Stago wrap. May be overkill but it sure is tough stuff.
I think these things that go into the ground that cannot really be changed once it is done is important to think hard on. Good luck!
Also, I think you will find foam surprisingly inexpensive.
Roger,
Neither XPS nor high-density Type IX EPS absorb much water, nor is either type of insulation negatively affected by damp conditions. That's why they are used below grade.
In any case, you want to install your rigid foam over a layer of crushed stone, which acts as a capillary break, and the crushed stone should be drained by perforated pipes leading to daylight, a distant drywell, or a sump. If you do that, the foam will stay dry.
Hi Martin,
You are right, installing crush stone and proper drainage should provide the capillary break and drainage to take care of this issue. Here's where I read about the battle of the foams.
http://www.plastifab.com/technicallibrary/docs/pibs/PIB_268_-_EPS_Insulation_R-Value_Retention_After_15-Year_Below-Grade_Service.pdf
I know this is issued by an EPS company and I actually left a message with the testing company to track down the actual report. I am just curious.
Would you recommend using foam board under basement floor in Alabama?
William,
In Alabama, I would say you probably don't need rigid foam under a basement slab.
Do any Southern builders care to comment?
I live in NJ. We're adding a 520 sq ft addition with a full basement. I've told my contractor that I want 2" XPS foam under the slab, but he's trying to discourage me. He's telling me that they've seen a lot more cracks develop in slabs that have XPS underneath. They just want to put a 6 mil poly vapor barrier underneath over 4" of crushed stone.
Does he have a legitimate concern, or should I insist on the XPS? If we go with the XPS, should we still have the vapor barrier and are there specific techniques that need to be followed to minimize cracking?
Eric,
In New Jersey, I would definitely recommend rigid foam under your basement slab. If your contractor doesn't know how to place concrete over rigid foam, it's probably time to find a new contractor. Your contractor is ignorant and possibly unskilled if he says that he can't install a quality slab over rigid foam.
Be sure to place your polyethylene on top of the rigid foam (directly under the concrete). It will take your contractor a little longer to finish the slab than he is used to, because the foam and poly will prevent moisture from wicking downwards. That delays curing, but the concrete will be strong as long as the contractor doesn't water down his concrete and stays on site long enough to finish it. He shouldn't be in a hurry.
Thanks for the response Martin. Two more questions:
Will I still see a benefit even though the slab is being tied into a non-insulated slab? (this is an addition).
Should we be specifying anything special about the concrete mix for the pour?
Sorry to revive an old post, but there are some important tidbits of information here. I've read the articles by Joseph Lstiburek at BuildingScience.com where he intones us never, ever to put the polyethylene layer under the foam or we'll simply have moisture laden foam for eternity. (see paragraph 5 in http://www.buildingscience.com/docum...059-slab-happy).
However, if we put the polyethylene layer OVER the foam, then how do we address the issue of securing hydronic heat lines? Most installers tack the radiant heat tubing to the foam, but we've now just put thousand of holes in the poly, making it kinda useless, wouldn't you think?
I've read where if polyethylene is being used to control vapor, these penetrations may pose no real issue as most vapor moves with air, and the concrete is an air barrier. Yet, if we are employing the polyethylene for control of radon gases, I've also read that any penetrations negate the poly's utility.
So, tell me, where do you put you polyethylene layer? What is the solution to this dilemma? Secure the PEX to the rebar, then pour over the poly (which lies over the foam)? Or is wet XPS not really that bad?