Insulation retrofit for radiant floor heat

I’ve searched this site and found a lot of useful information but no clear consensus on what is the “best” method for retrofitting insulation in radiant floors. The situation is exposed hydronic tubing stapled up to the subfloor with no heat transfer plate. The joist bays are relatively accessible from the insulated basement and crawl spaces. Climate Zone 6.
The information I’ve gathered points me to spending money on insulation products rather than radiant barriers. It seems like the best approach would be to install foil faced polyiso fastened and sealed up to 4″ down from the tubing. The air space created will boost the R-value a bit beyond the polyiso. This will be labor intensive in several areas due to odd framing spacing and other things in the joist bays.
A lower cost option would be to install faced fiberglass stapled to the bottom of the floor joists. It doesn’t seem like it would matter much if there was an air space between the fiberglass and tubing since it will not be a sealed installation.
It seems that any type of insulation would be much better than having it uninsulated as it is now. That would at least reduce the heat loss to the basement and crawl spaces below and improve distribution, although it’s tough to say how much. We plan to compare the cost of the distribution improvement with the cost of adding cold-climate heat pumps.
Thanks for the help.
GBA Detail Library
A collection of one thousand construction details organized by climate and house part
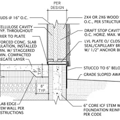
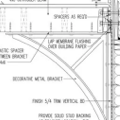
Replies
Foil face polyiso would be a very expensive way to deal with it. In an insulated basement (even if only semi-heated) R13-R19 kraft faced batts stapled to the sides of the joists (not at the bottom, stapled to the joist edges) with top of the fluff ~2" below the subfloor works.
You would get a very modest boost out of laying aluminum foil (the kitchen goods are fine) on top of the batts, but most of the heat transfer from the tubing to the subfloor is via conduction & convection, much less by radiation.
If you can install heat transfer plates (even the cheap sheet metal type, as long as they grip the tubing well) performance would go up quite a bit, and you can snug the R13s up tight to the tubing/plates, with no air-gap.
You could abandon the system and add baseboard heat. I have used to radiant bubble foil years ago and there was no downward heat so it seemed to do the job. i am not happy with under floor radiant at this time. Mini splits and electric matt heat under bath tile is what I like now.
Would you be able to retrofit heat emission plates of some sort ?
As Dana stated above , don't be concerned with shiny stuff .
If the tubing is stapled to the floor you may experience striping , adding the plates would be best , lowering the tubing 1" would be better than what you have . Put the insulation right up to the bottom of the tubing regardless of what you do .
Can you post pix of the install and include the end of the joist bays ?
Thanks for the feedback. It is possible to retrofit heat transfer plates, it will require pulling many of the staples holding the hoses up. A heating contractor said it's newer Entran tubing that appears to be in good shape. I only have one pic on file and it's not very good, but I've attached it for what it's worth. Retrofitting the plates and installing fiberglass will probably cost less than cutting and fitting polyiso, so we'll explore that option.
EPDM tubing isn't designed for heat transfer plates, so it is what it is...
If you suspend the tubes below the sub-floor the striping effects will go away, but the water temperature requirements would soar. Insulating from below won't make the striping any worse than it is now, so it's up to you to decide whether it's objectionable or not. The Entran product line is on it's third generation (after v.1 and v.2 had a gazillion leak problems and class-action lawsuits.) Given the less than stellar history on EPDM tubing in this application the last thing I'd want to do is run it at a temperature any higher than is necessary, since higher temperatures accelerate the aging of polymeric materials. It may be rated for 200F in the spec, but I personally wouldn't run it higher than 140F unless I were freezing. YMMV.
It looks like you have TJIs rather than dimensional lumber joists. This means you can't use batts normally designed for wood framing, since they are only 15" wide. There are16" wide batts designed for steel framing that would work- you may or may not be able to find them at box-store type outlets, but steel framing is common in the commercial construction world- they're out there. R13s are fine for zone isolation like this.
Thanks Dana, I appreciate the info. I was coming to that conclusion about the EPDM tubing as I was looking around for the proper sized heat transfer plates. Fiberglass in the joist bays seems like the most reasonable option to improve the distribution. The framing is mixed; rough sawn for the main area with spacing varying from 12" to 16", dimensional lumber in one crawl space, and TJI in another crawl space. So different widths will have to be sourced and cut.
If it's a bunch of random width it might be less work to just staple up some blowing mesh (using landcaping fabric is fine) an inch or two below the tubing and another mesh 4" below that and squirt in low-density cellulose. The mesh next to the tubing will keep the cellulose from getting between the tubing & subfloor, and even if it bellys up to touch the subfloor it won't change the striping much. You don't want to dense-pack it, just fill to where it starts to firm up a bit- a soft mattress fill, not a firm one . With a 1-stage rental blower you'd just slit the lower mesh 4-5" every 6' or so where/when you want to insert the hose, blow one direction until it starts to firm up, then the other, then move down feeling the firmness with your fingers until you it a soft-ish spot again.
Not so fast guys . EPDM tubing wreaks havoc on many things . Most of all zone valves , mixing devices and most important heat exchangers . How long are these loops and what circulator is being used . We worry about erosion quite a bit in hydronic systems and the EPDM type tubing adds a whole other dimension , that being the material itself . Those leaks , many of them at least were caused by a breaking loose or de lamination as it were of the pipe . I cannot tell you how many systems , boilers , valves , circulators ,etc I have removed , abandoned and replaced due to this type of tubing .
As Dana mentioned high temp is the enemy here but even worse is head . If the mechanical energy needed to overcome the head loss is such that you need to move fluid at a higher velocity you will break these pieces of rubber away from the tube wall and deposit them in the moving parts of your system rather quickly .
I've read accounts of mysterious black goo destroying heat exchangers in mod-cons on systems with EPDM tubing too. If there's a budget for it getting rid of the EPDM might be the right thing to do, but that isn't what was being asked.
I'd personally never install it (in my house or any other), but it's up to the owner whether its worth getting rid of it. Replacing it with PEX & heat spreader plates is not a cheap solution.
Thanks all for the input, very helpful. I will remind the client of the concerns over EPDM tubing and we'll weigh that with the cost of insulating between the floor joists.
May not be what was being asked but probably more relevant to the final choice then anything else we told him . Doesn't make alot of sense to encapsulate something that very well may become a huge problem at a later date .