Insulation for Pretty Good House Goals

New construction, zone 2, about 50 miles south of Houston, 10 miles from the gulf coast. 98% of the homes in this area are built and insulated the same way they were 30 years ago (or longer) when my previous home was built. Blown rockwool or fiberglass batts in the walls and above ceilings. Vented attic (typically ridge vents). Little if any consideration is given to a tight building envelope. HVAC ducts in the attics, which can reach 140+* in the summer. Slab on grade foundation. OSB wall sheathing with Tyvek. No additional sealing. One ton of AC for every 600 square feet.
My goal is to build a “pretty good” house (not shooting for any awards or certifications). Attached is a cross-section of the house. Front of the house is on right side where exterior stairs are shown. House will have a full concrete foundation (top of foundation about 18″ above natural ground) with a crawl space built on the foundation. Top of foundation to finished floor is 48″. Crawl space under conditioned living area will be closed/unvented. Crawl space under front veranda and rear screened porch will be vented. Crawl space has a continuous CMU perimeter stem wall, including between the porches and conditioned living area.
As the cross-section shows, the current plan is to spray 2″ of closed cell foam on the inside of the conditioned crawl space CMU stem walls. Exterior house walls will have open cell spray foam. Underside of roof will also get open cell spray foam. All exterior walls are 2×6’s, and wall sheathing will be 7/16″ zip (not zip-R). Roof will be fiberglass shingles over OSB.
Because a lot of the HVAC ductwork will be in the attic areas above the porches, the plan is to encapsulate the entire attic, so there will be some type of insulation (currently OC spray foam) above the porch and veranda ceilings. You can’t tell from the cross-section, but the porches are each about 50′ long, so it’s a large area.
Spray foam hasn’t “caught on” here yet. Maybe a few percent of the new homes use it, and those probably don’t use it correctly. It’s also pretty expensive here. I’m pretty sold on the closed cell foam in the crawl space. I’m looking for alternative ideas for the insulation, including for example, using a combination of materials (e.g., spray foam in crawl space and under roof and blown rock wool in walls and over porch ceilings), or maybe a solution that doesn’t use any spray foam except in crawl space. However, I need to keep it pretty basic, i.e., no leading/bleeding edge solutions. One thing I don’t want to do is use Zip-R or insulation outside of the wall or roof sheathing.
Thanks,
Ira
GBA Detail Library
A collection of one thousand construction details organized by climate and house part
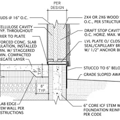
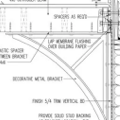
Replies
I would try to keep mechanicals out of the attic, even if you seal the attic and bring it into the building envelope. It’s a pain to maintain stuff in attics even if they are conditioned attics.
I’d use closed cell spray foam under the sheathing, open cell can sometimes have moisture issues.
Why are you opposed to exterior continuous insulation? You’d likely see better overall thermal performance from a wall with regular fiberglass batts and exterior rigid foam than you will from open cell spray foam in the stud bays. Spray foam, either open or closed cell, does nothing to deal with the thermal bridging of the studs. Only continuous insulation, usually rigid foam on the exterior, can help with thermal bridging. I’d consider using batts in the stud bays and exterior rigid foam instead of spray foam in the walls. M
Spray foam is not a magic insulation that blows everything else away even though the marketing materials often imply that. Spray foam has some advantages (notably air sealing and its ability to provide a fully adhered layer of insulation), but those benefits can only be fully realized in certain niche applications. In many “regular” applications you can do almost as well performance wise with more conventional insulating materials at lower cost.
Bill
One of the goals is to not stray too far from what is normally done in this area. What I've discovered is that anything that is not typical in this area will cost a lot more than it should because the trades don't know how to bid it, so they will all bid really high.
All homes in this area built in the last 50 years have ductwork and the furnace/blower in the attic, so HVAC companies are used to working on that stuff in the attic. I would probably be charged a premium on both installation and maintenance if I put it all in the crawl space. Plus it will all be readily accessible with a full size stairway (not a pull-down attic stairs) and lots of decking and headroom.
Exterior continuous insulation (especially Dow "blue board" up to 3/4" thick) is fairly common around here, although it is probably never detailed correctly to provide air sealing. Zip wall sheathing is seldom used around here, and when it is, it is not Zip-R. In general, does a correctly installed Zip wall sheathing system (either Zip-R or Zip over 3/4" Dow blue board) provide adequate air sealing such that blown in insulation doesn't need additional sealing?
I'm especially interested in spray foam alternatives for under-roof applications (that don't require exterior insulation), and what is required for air sealing the roof in those applications.
Thanks,
Ira
Coastal regions and hot - humid climates will benefit from unvented, conditioned attics due to hurricane risks. In your case, it is what people do anyway.
Rather than spray foam of any type, consider blown fiber in the walls and roof. Cellulose is the most environmentally friendly and has more fringe benefits than blown fiberglass, but blown fiberglass may be more common. In your climate zone, fiber products can be used in the roof, provided there is a vapor diffusion port: https://www.greenbuildingadvisor.com/article/vapor-diffusion-ports
Your question about Zip sheathing's installation sounds a bit like faith based air sealing. Rely on blower door testing rather than a product's reputation to verify airtightness, then fix any air leaks. It is not difficult to bring the air barrier from the walls over the roof and apply overhangs afterwards. There are details in the link below from a BSC case study house in Houston you might find useful: https://www.buildingscience.com/documents/profiles/etw-houston-profile
If using continuous exterior insulation, consider 3/4" polyiso; this has greater r value than XPS, and has substantially less environmental impact.
Most people here, myself included, probably have more heating degree days in October than you do in January. You might also try searching Building Science Corporation 's website, filtering by hot-humid climate. This might give you a better idea of where to spend money and/or how to best prioritize options.
Ira,
I would read this article if you haven't done so. I think it is one of the most important articles on GBA and should be posted to the home page at all times:
https://www.greenbuildingadvisor.com/article/how-to-build-an-insulated-cathedral-ceiling
I would read this as well:
https://www.greenbuildingadvisor.com/article/creating-a-conditioned-attic
Personally, I would avoid spray foam when possible. If the spray foam- especially closed cell foam- isn't applied correctly or the mix is off, then removing the product is akin to chipping away semi-cured glue from your structural framing. Also, I just don't trust the stuff (especially open cell foam) in a fire. https://youtu.be/snlhECzj1E8?t=540. If you do use spray foam, then make sure you find the best contractor possible and be willing to pay a little more for them.
Okay with that out of the way, here is the BIG QUESTION regarding your roof: Do you want a Vented Roof or an Unvented Roof?
The answer may change your architectural details. Currently, your architect/designer has already spec'd the use of spray foam for an Unvented Roof assembly. You can't just change this to a Vented Roof without altering the plans. Your roof framing and trim details will need to be modified to accommodate baffles, increased rafter depth, soffit vents, and ridge vents to achieve a proper Vented Roof.
Without altering your existing plans, you are left with only three options, in order of best to worst:
1. Exterior rigid foam above the roof deck
2.close cell spray foam under the roof deck
3. open cell spray foam under the roof deck*
*There is some debate here as to whether or not open cell foam should ever be applied under a roof deck. This is why Bill recommended closed cell foam instead. OC foam is an air barrier at around 5"+ depth but it is never a vapor retarder. Read this article for more:
https://www.greenbuildingadvisor.com/article/open-cell-spray-foam-and-damp-roof-sheathing
Ira, you wrote:
"I'm especially interested in spray foam alternatives for under-roof applications (that don't require exterior insulation), and what is required for air sealing the roof in those applications."
IF you are willing to work with your designer to alter your existing plans, you can then explore spray foam alternatives. This may include adding baffles and then fluffy insulation like batts, or netted fiberglass or cellulose.
You are right to then think about air sealing as fluffy insulation is air permeable. You can use an air-tight drywall approach, or a tack up/tape a smart-vapor retarder like Membrain or Intello Plus. This will be a bit of challenge by looking at your current design and may be unusual for your contractors.
If you use Huber's highly-rated Zip system tape on your Zip sheathing, your walls will be airtight. Zip sheathing is an air barrier, assuming you use their tape and avoid overdriving nails. And do a good job air-sealing around windows and doors. You probably know that tight air sealing is needed, but if you aren't doing the work yourself, this needs to be communicated to the builder, and monitored or verified by you to fix before siding and insulating.
It would be helpful to know what R-values you are targeting for your walls and roof. You don't specify how much spray foam you intend to install. Spray foam is expensive when you decide to use it as your primary insulation material. Its WAY cheaper to use fiberglass in stud bays, or mineral wool batts, or blown-in cellulose. You can install any of these products yourself if you want, further keeping your costs down. If you weren't going to use much spray foam to keep costs down, you don't have to worry about the lower R-value of fiberglass batts, or thermal bridging through studs. Either way you may end up with comparable overall R-values, we don't know enough about your plan for making quantitative comparisons.
Its much cheaper to have a ventilated attic with insulation on the ceiling, than try to insulate the significantly larger area of the roof, with all the additional detailing it involves to do it right. You can pile on plenty of insulation very cheaply and easily on an attic floor. (And you can do it yourself easily enough.) At least consider this alternative, and compute the cost savings involved, including the labor costs. Can you use those savings for air-sealing or additional insulation, which can reduce the costs of mechanicals and utility bills? And improve comfort? Or to allocate some space below your attic for mechanicals?
Calculate the heat losses and gains of each of your rooms or areas of the home to size your mechanicals and see how much additional insulation will impact those numbers. Insulation is cheap to add during new construction. The R-value and air-sealing of your building envelope matters a lot. Your home will be more comfortable, less expensive to operate, and your air conditioning system will be sized smaller and cheaper. You probably know this already, but doing some quantitative modeling and pricing will be useful for making the decisions you face.
Are you installing an ERV to bring in fresh air that's cooled and dehumidified by the exhaust air stream? In your very humid and hot summers, that would be helpful. A source of fresh air is needed in an airtight building for healthy indoor air quality.
The people at BSC have written a number of articles wrt building and re-building in flood and hurricane prone areas like Houston and Florida. In particular, they have some suggestions for designing houses such that when they do get wet and/or flooded, they can (relatively) easily be dried out before mold ruins everything prior to rebuild. This is pertinent to your insulation selection, and where you put your insulation.
Eg,
BSD-111 Flood and Hurricane Resistant Buildings
BSI-101 Rebuilding Houston
BA-0704 Durable and Energy Efficient Home in Post-Katrina NO.
Also, there's the FEMA Building Guide to Coastal Construction.
There is a lot of information there, including a lot of specific details for insulating walls and attics. Raising the building is the first priority, glad you're starting 48" up.
I encourage you to model your house in BEopt before you decide where to put your HVAC. The roof pitch looks steep I am betting the conditioned attic will have 80% more surface area than the attic floor maybe closer to 120% when you add the porch ceiling, dormers, gable walls and roofs to your thermal envelope.
The way I see it the use of spray foam is a direct result of poor planning and or laziness. There is almost always a better less expensive way to get the job done.
If you must have a conditioned attic because you are planning on finishing it someday I say put rigid foam on the outside with a nail bed on top. Used foam is often available and could be very inexpensive.
My guess is you could get a R60 attic floor for 1/3 of the cost of R25 spray foam attic.
Also consider spray foam is complex chemistry often done by Gomer Pyle under veering conditions. Things can and do go wrong from time to time and the smell has driven more than a few from their homes.
Any up charge for working in a crawlspace will be way less that the spray foam upcharge.
Do not be a lemming and accept that is how we do it around here. Be strong and say no stupid. This is your one chance to get what you want how you want it.
https://beopt.nrel.gov/home
Walta
The walls are R13 OC spray foam. Under roof sheathing is R19 OC spray foam. Crawl space perimeter stem walls will get 2" of CC spray foam. Not sure what the attic floor above the porches will get, but they will be in the building envelope. I will be using the Huber Zip tape and/or the Huber Zip liquid flashing, and the wall penetrations will be correctly detailed. Although the Zip system is seldom used here, I'm confident that it will be done correctly, and it's fairly easy to determine whether it was done correctly.
The HVAC system was designed by a professional that contributes/posts on GBA often, and is familiar with the local climate and construction techniques/methods. His plan calls for two 2-ton conventional HVAC systems and a dehumidifier.
I understand there are methods/techniques that are better than what I hope to do. However, cost is an issue. Also, with regard to being a lemming, I've read many posts on this website and others that a homeowner is better off not using the advanced techniques if he doesn't have builders/contractors that know how to implement them. I talked to several custom home builders in my area about this house. Many were unwilling to build it due to the "pretty tight home" and closed crawl space design. Spray foam is somewhat common in the Houston area, so I'm confident that I can find someone there that can do a good job without running the costs way up.
I've never seen insulation on top of the roof sheathing around here. My guess is that it is seldom done in Houston (fifty miles away). I'm not even sure it can be done around here since I'm in the "Inland Zone 1" hurricane zone, which is the 2nd strictest area in Texas, and therefore we have to deal with significant windstorm requirements (to survive 120 mph gusts). To be in the strictest area, you have to be in a beach front community, pretty much within a half mile of the beach. Even if it is allowed, it would be extremely difficult to find someone that knows how to do rooftop insulation, and just as difficult to ensure that it is done correctly.
A specific question... if I use OC spray foam under the roof sheathing, would it be better to use Zip sheathing for the roof sheathing or regular OSB with a particular type of roof underlayment (between fiberglass/asphalt shingles and sheathing)?
Thanks,
Ira
Ira,
You wrote:
"The walls are R13 OC spray foam. Under roof sheathing is R19 OC spray foam. Crawl space perimeter stem walls will get 2" of CC spray foam."
What energy code (year) is used in TX? I thought you needed at least R-38 in Zone 2?
Also, if you do opt for OC foam under your roof sheathing, then be sure to run your HVAC to the attic. *It is critical that your attic space be conditioned with that set up.*
Help me understand what makes your house better than the code minimum stuff the production builders slap together every day of the week? Some promised air sealing.
I do not live in your climate but to my ear R13 walls and R 19 roof sound like code minimum numbers.
I still say you will cut your electric bill in half if you put the equipment and duct in the crawl space and put R6 on the attic floor. Anyone disagree given the large porch ceiling and roof areas a conditioned attic would into the thermal envelope.
Have you seen a manual J calculation with and without the conditioned attic?
Do you have a plan to finish the attic at some later time?
Walta
Rick,
I don't know what the energy code is for new homes in my area. However, over the last couple of years, I've seen dozens of new spec homes built in the neighborhood where I currently live that are 2x4 construction with fiberglass batts in the walls, 1/8" Thermo-Ply sheathing (except on shear walls, corners, etc.), and very poorly installed Tyvek. I never measured it, but my guess is at most R-22 loose fill fiberglass on top of the ceiling. I haven't seen any consideration for air sealing other than Tyvek and improper taping at perforations that usually comes "unstuck" before the brick veneer or siding goes up.
My home will be custom built, so we will make sure better methods and material are used, e.g., Zip sheathing completely taped/sealed, 2x6 walls, etc. The typical custom home in this area is somewhere between the spec homes and my home with regard to materials and methods, but probably a little closer to the spec home side.
At some point, I have to trust the architect and the HVAC designer (both of whom are well known in their professions and are very familiar with the local climate) to have designed a home that fits our needs. The HVAC system is pretty much top-of-the-line for a conventional system, and it was designed based on the info I've posted. All HVAC components except the outdoor units and one dehumidifier in the crawl space will be in the attic. We are using tankless water heaters. On the other end of the spectrum, we will have at least one prefabricated wood burning fireplace in the house, maybe two. The range will be natural gas, as will the furnaces and tankless water heaters. We aren't expecting a net-zero house, $20/month cooling/heating bills, etc. It's unlikely we will have solar anytime soon. In other words, there will be quite a few compromises to accommodate what we think is important to us. From a green building perspective, I think the home will be significantly better than most in our area, but quite a bit less than most of the homes discussed on this web site.
Ira
Walter,
R-13/R-19 may be code minimum here. Air sealing is probably the biggest improvement over what is normally built here, both spec and custom. HVAC design is better. Most houses around here still have 1-Ton per 500-600 square feet. Mine will be closer to 1-Ton per 850 square feet, which I understand is still a lot of AC, but a lot better than most around here.
I haven't seen a manual J without the conditioned attic because I have not considered a vented attic. The house (including all of the major systems) is being built with the expectation that the attic will be converted to living space in the future (probably by the next owner, as I we have no need for the additional space). There is about 1400 sqft of attic space that can easily be converted into two additional bedrooms, one or two bathrooms, and a large bonus room.
Ira
What’s the consensus around here with open cell foam? My area seems to use closed cell almost exclusively. I didn’t have e a single contractor recommend open cell and we used closed in the wall cavities, roof deck, and crawl space.
Where's "around here"? I'm 50 miles south of Houston.
Foundation and stem walls are done, framing to start in a week or so. Still trying to decide on insulation, but leaning heavily towards OC foam under roof deck, blown rock wool in walls, and CC foam on inside of crawl space perimeter stem walls (continuous CMU blocks).
Still unsure about what to do above porch ceilings. Currently leaning towards blown in loose fill rock wool, but not sure how thick it needs to be or how to air seal the porch ceilings. Maybe some type of roll-on air barrier like one of the Proseco products? Anyone know if that can be applied directly to the 1x6 T&G porch ceilings (attic side), or should I hang sheathing to the joists first, then roll on the barrier to the underside of the porch ceiling before putting up the 1x6 finished porch ceiling.
I know a lot of people say rock wool will settle over time, especially in walls. However, my previous home was flooded about five years ago, and when we removed the drywall, I didn't see any signs that the rock wool had settled in the wall cavities.
Ira