Insulation Re-do

I am an architect working on a 2 BR/2BA high end addition above an existing garage in the mountains of Colorado. The exterior walls are 2×6 walls, roof has 2×12 rafters, floor is 11-7/8″ TJI’s with 1 1/2″ of gypcrete for radiant heating and tile floor. Garage below is heated and insulated. The contractor just insulated the new space and did it differently than spec’d. We caught it before drywall and he is going to go back and make changes to bring things to what was spec’d. We are having extremely cold temperatures right now (-15) and I’m concerned about installing foam on very cold sheathing. Here is what was spec’d and what was installed:
2×6 Wall spec: 2″ min. spray foam with blown-in cellulose insulation to fill the cavity, no vapor barrier. Installed: 5 1/2″ of blown fiberglass with vapor barrier.
2×12 Roof spec: 4″ min. spray foam with blown-in cellulose insulation, no vapor barrier.
Installed: roughly 2 1/2″ to 9″ spray foam and R-30C kraft faced batts. Doing a partial inspection I found one area about 12″x24″ where there was no foam against the roof sheathing.
2x Interior Wall spec: blown-in cellulose.
Installed: kraft faced batts and open faced batts.
11-7/8 TJI Garage Ceiling spec: blown-in cellulose for sound and insulation.
Installed: kraft faced batts. There are plumbing lines in the garage ceiling and contractor felt that batts would be better if there were ever a water leak.
We also called out to spray foam all penetrations and rim joists. All penetrations in studs, plates, rafters, and sheathing were also to be filled. Wood to wood connections and gaps were to be caulked and sealed. The rim was not foamed and some penetrations were filled but many were not. I don’t know if penetrations at the exterior fiberglass filled wall were foamed.
I had a very helpful conversation with an insulation expert from Wisconsin yesterday who has cold climate concerns about the “flash and batt” system and also expressed concerns about trying to apply foam to extremely cold sheathing, should we stay with the spec.
I’m curious to get forum input about our best options at this stage. Does the extreme cold we are having make our spec’d wall system much more difficult to install properly right now? Would heating the interior make it less likely to have foam adhesion issues?
I’d also be curious to get thoughts about the existing blown in fiberglass insulation vs. our spec’d system. The owner wants a very good thermal envelope. And finally, thoughts about the garage ceiling as installed vs. spec’d would be great.
In addition: blower door test? foam manufacturer inspection?
Thank you for your time and consideration of our situation.
GBA Detail Library
A collection of one thousand construction details organized by climate and house part
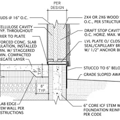
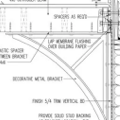
Replies
Rick,
First of all, you didn't mention whether the specifications call for open-cell spray foam or closed-cell spray foam. The specified insulation for the roof assembly -- 4" min. spray foam with blown-in cellulose insulation -- will only work if (a) you use closed-cell foam, and (b) the house is located in Climate Zone 6 or somewhere warmer. If you are in Climate Zone 7, the minimum R-value for the spray foam layer is R-30. More information here: How to Build an Insulated Cathedral Ceiling.
There is lots to say on the issues you raise. In general, it's kind of a waste to use spray foam between studs or rafters, because the spray foam doesn't address thermal bridging. It's much better to install rigid foam on the outside of your wall sheathing and roof sheathing -- but I imagine that, at least at this project, it's too late to switch gears.
Thanks. Closed cell spray foam. Zone 6. Yes, I'm now in the camp of adding foam at the exterior. This project did not get spec'd that way, unfortunately.
Martin, I had planned to use the third unvented system as described in your article (which I read many times in working out the roof assembly):
"Install a layer of closed-cell spray foam against the underside of the roof sheathing, and fill the rest of the rafter cavity with an air-permeable insulation". We have the spray foam in the rafters and we need to verify thicknesses. For the air-permeable insulation, I assume unfaced batts or blown in fiberglass would be best. Does blown cellulose limit air movement too much? Thanks again for your input. It's a big help. Rick
Rick,
I think you should stick with your specs. It is the contractor's responsibility to build according to the specs.
The G.C. will to need to coordinate the spray foam work closely with the spray foam contractor. My guess is that the contractor will need to wait for a good weather window (a warm day) and will also need a heating system to warm the sheathing to the correct temperature. Needless to say, the spray foam contractor will be providing a warranty for his or her work, and therefore has a strong incentive to do a good job.
That said, this job has had an unusually high number of screw-ups, so someone needs to provide supervision and verification to be sure that the specs are met.
Martin, Yes, there has been a serious breach of contract here and a substitution of a lesser value insulation package than what was spec'd. This one of the challenging and frustrating parts of being an architect. Thanks for your input. In your opinion, will blown in fiberglass or cellulose be better under the spray foam at the rafters? Thanks, Rick
Rick,
I prefer cellulose to fiberglass, because cellulose does a better job of reducing air movement and does a better job of redistributing moisture if any areas of the assembly get damp.
To be specific, we are classified as Zone 6 with around 5500 degree days.
Martin, Last question (I think); At the garage ceiling, installed, we currently have R-30C kraft faced insulation in the ceiling. There are plumbing lines in the ceiling and in a dropped soffit. The ceiling is 11 7/8" TJI's with 3/4" floor sheathing with 1 1/2" of gypcrete. The floor above will be travertine tile. The 3-car garage has a heated slab and the walls are insulated with blown cellulose (garage doors are thermal weak spot). In the winter cars will drive in with snow and it will melt on the floor of the garage. I'm struggling with getting insulation and vapor issues right here. Any opinions? Thanks, Rick
Thanks again for all the good information. Rick
Rick,
The most important issue with the garage ceiling is to make sure that it is airtight.
Whether or not you need to focus on the insulation details of the garage ceiling depends on whether the owners will heat the garage to 72 degrees or will sometimes leave the garage unheated. You might consider the possibility that a future owner would decide not to heat the garage. At that point, the need for good ceiling insulation would increase. For more information on insulating the ceiling of a garage with a bonus room above, see How to Insulate a Cold Floor.
"This one of the challenging and frustrating parts of being an architect."
It needn't be. I suspect this is the result of a competitive bid where the contractor has been cutting corners to meet his low bid and hoping the homeowner, the architect and maybe even the building inspector don't notice. Almost all our projects are open-book negotiated bid with a single contractor we know to be cost-appropriate for the project. In return for a clean shot at the project the contractor opens his subcontractor proposals with their detailed specifications and costs to inspection prior to construction. The contractor then has little incentive to sneak in lower-spec work and every incentive to ensure the named sub performs per contract. There are many additional advantages for both homeowner and architect to this approach:
http://hartwrightarchitects.com/an-argument-for-negotiated-bidding/
Thanks James, I agree with you. 99% of our work is an open book negotiated bid with a preferred contractor. We strongly encourage the owner/architect/contractor relationship you describe. I don't feel that competitive bid contracts work best for my clients. The low price driven contract ignores the importance of communication, quality, and relationships in getting the owner the best product. In this case however, the owner is from a competitive bid market and insisted on the competitive bid process. I stressed to all bidders (contractors I already had a good relationship with) the importance of making sure they were very confident with their bid numbers. It's been a challenging process because of the antagonistic relationship set up by this type of contract. Personally, it's been especially difficult because the problems are with a contractor with whom I've had a good working relationship in the past.
Too bad, Rick, that even 'high-end' clients often think they can get better value by shopping the heck out of a project. Good luck.
Thank you James. That's exactly what happened.
Just curious, but what's the ZIP code? 5500 HDD is more typical of the WARM edge of climate zone 5, and nowhere near a zone-6 type climate. (Zone 5 is between 5400-9000 HDD, zone 6 is more than 9000 HDD.)
Find the county in this document:
http://apps1.eere.energy.gov/buildings/publications/pdfs/building_america/ba_climateguide_7_1.pdf
Most of Colorado is in climate zone 5, only the higher altitudes hit 6 & 7, and the southeast corner is climate zone 4. If you're on the warm edge of zone 5 rather than zone 6, that makes a difference on what works or doesn't on insulation stackups from a dew-point control aspect.