Insulation payback

A co-worker of mine is planning his new house. I have been offering suggestions on insulation. His architect has commented that the payback is too long for any insulation other than fiberglass. How do you respond to that?
GBA Detail Library
A collection of one thousand construction details organized by climate and house part
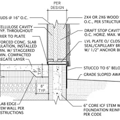
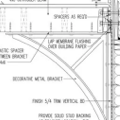
Replies
That it's like saying, "the return is too low to invest in anything other than 3 year bank CDs." Such a statement betrays a shocking amount of ignorance, especially for new construction where you have a variety of great opportunities to add various forms of insulation in a cost-effective manner that you rarely do with renovations.
Remember we are talking payback here not overall performance. I have to laugh because I just got done reading the Building Science Corp study then clicked on this Q&A. I guess their argument would be, assuming airtight outside walls, most insulation products perform similarly if installed correctly. The problem is fiberglass has a higher margin of error in getting that installation right.
It would be helpful for others to comment if you provided the climate zone and other factors (style of house, size, etc.)
If the guy is like, seventy eight years old then I give the architect the nod on the payback time. Now ask the guy if he wants to drive a Yugo, because anything else doesnt give a payback. My 1996 GMC will disagree at 199,000 miles but for most people...
I would quiz the architect about how much building science he knows. To many, R value is R value no matter the material used to get it, differences in real-world performance are not understood, and the maximum acceptable payback period is a few years. The architect would have to be able to expound at length about the different materials and their particular benefits and drawbacks to have any credibility.
Scott,
In Vermont, bids for attic insulation jobs often show a lower price for cellulose than fiberglass. It's not only better, it's cheaper. So how can the payback be better for fiberglass in that case?
What have you been suggesting in place of fiberglass? What is the baseline in terms of wall thickness and air tightness? Whether or not the architect is correct depends on these facts and others, such as climate and fuel costs. For example, if other air sealing measures are already in place and you are suggesting closed cell spray foam in the stud cavities, the payback would be bad, especially if the climate is moderate and fuel is cheap. On the other hand, if this is a cold climate, the baseline is a leaky structure, and you are proposing some air sealing measures and cellulose, then the payback would be favorable.
There is payback in terms of NPV on future energy savings, but there's also payback in reduced up-front mechanical costs, payback in resilience, hedge value against future price inflation, payback in comfort.
If the only metric being used is the net present value of future energy savings at flat energy pricing the boat has been missed.
Fiberglass can be good, 1.8lb dense packed fiberglass in stud bays is AWESOME, but not necessarily worth the premium over damp-sprayed cellulose or R23 rock wool batts, spending the difference on exterior insulating sheathing. Code min walls for US climate zone 6 (includes all of VT) are R20 + R5 c.i. or R13 + R10. R5 is insufficient exterior R for dew point control on R20 in a zone 6 climate, so R13 + R10 is a better (read "more resilient") choice. R13 damp sprayed cellulose is more air-retardent than R13 fiberglass, has measurably higher thermal mass, and has many times the moisture buffering capacity, which enhances the resilience further.
From a long term energy cost point of view it can be rational to take it up to whole-assembly R-values sufficient to go Net Zero Energy. (The approximate whole assembly R value it takes to get there can be found in Table 2, p 10 of BA-1005: http://buildingscience.com/documents/bareports/ba-1005-building-america-high-r-value-high-performance-residential-buildings-all-climate-zones/view )
Unlike utility & fuel bills, the additional cost of a high-R house is subsidized in the tax code- it's often cheaper to go high-R rather than code min, if you can get it to the point where you can heat/cool the place with a couple of mini-splits for under $10K upfront cost rather than spending $25-50K on mechanical systems, since the operational cost at the very-low loads is but a fraction of what it costs to run the more expensive systems supporting code-min loads. If you build to where you're spending $500-800/year on heat & power instead of $2500-3000, those savings are in after-tax dollars, and you are hedged against future energy price volatility.
I'm suggesting the use of mineral wool instead of fiberglass. Its going to be an uphill battle to increase energy efficiency of buildings as many people don't really care about it. Granite counter tops and hardwood floors is where its at.
The additional whole-wall R of R23 rock wool vs. R20 fiberglass is much smaller than the center-cavity R implies. The whole-wall R of a 2x6/R23 rock wool wall with no insulating sheathing comes in at about R15.6-R16 (counting air-films wallboard,wood sheathing, & siding discounted for the thermal bridging of the framing at a 25% framing fraction.)
The R20-fiberglass equivalent wall comes in at R15.2-R15.5 whole wall That's less than an R1 difference in whole-wall performance, all else being equal. The fire-resistance of rock wool is much higher, which is worth something.
If there is a signficant cost difference, spending the cost difference on insulating sheathing is worth it, especially if it's sufficient for dew point control at the sheathing.
The code-min R20 + 5 reduces drying capacity since it requires a class-II vapor retarder on the interior, and the foam is a vapor retarder on the exterior. That comes in at about R20.2- R20.5 whole-wall, but it's not very moisture resilient with half-perm paint on the interior, and would need a smart vapor retarder to give it a resilence boost. R20 cellulose and a smart vapor retarder would offer a significant resilience boost over R20 fiberglass and half-perm paint.
The other code-min prescriptive is R13 + 10 (2" of XPS or polyiso or 2.5" of EPS), and is more expensive than R20 + 5, but it's also far more moisture resilient since the interior side can be left vapor open. (R13 cellulose would be even more resilient.) At a 25% framing fraction it comes in at about R20.4 - R20.7
It has very limited drying capacity to the exterior through 2" XPS (about 0.6-0.7 perms) and zero drying capacity through 2" foil faced polyiso, but about 1 perm through 2.5" EPS.
R15 (rock wool or fiberglass) + R8.4 (2" of 1.5lbs density EPS) has nearly comparable performance at a whole-wall performance of R19.4- R19.7, but is cheaper than R13 + R10 XPS/iso, and would allow the sheathing to dry toward the exterior (1.2-1.5 perms, still a class-III vapor retarder) as well as ample drying toward the interior, and plenty of dew point control. But it doesn't quite hit code-min, coming in about R1 shy on a whole wall basis, despite being slightly higher R at center-cavity.