Insulation options and costs for (vented) crawl space floor and (unvented) roof

Hi all. Long time reader/lurker here and finally have a reason to post something. I built a freestanding addition to my house that sits ~2′ above grade. The crawl space sides are completely open, the front crawl space wall is just the existing house foundation, and the rear crawl space wall is 12″ CMU. Floor joists span from the CMU wall, over a beam ~3′ from the existing house foundation (herego the addition is “freestanding” even though it butts up against the existing foundation). The roof is flat (1/4:12) and unvented (it’s basically a floor joist system). Roof has 2″ of GAF glass-faced polyiso on the exterior (covered by DensDeck and TPO). It’s time to insulate under the floor and ceiling – both are ~400 sqft. (note: Walls are done with R23 RockWool (inside) and 1″ polyiso RMAX (outside).
R-value reqs are R19 (floor) and R38 (ceiling)
Floor: I was thinking 3″ closed cell for vapor/moisture protection given the proximity to grade. A contractor just quoted me $1200 for 5.5″ of open cell which I think is the wrong choice for the crawl space, but could be wrong. Joists are 9.5″
Ceiling: I was thinking of just using batts because I have the polyiso on the exterior, and the thought of foam scares me in case there’s a roof membrane leak. The problem is I need 24″ “steel stud” batts for the TJI’s and am having an impossible time sourcing Rockwool in that size. I could probably find properly sized fiberglass/ECOBATT batts if need be. The same contractor quoted me $1300 for 8.5″ of open cell as an alternative. Joist are also 9.5″
Thoughts on these options and contractor quotes would be super appreciated.
I know everyone prefers closed crawls (me too – my main house is closed up) but due to some design limitations and budget, the open crawl was my only realistic option. For what it’s worth, there are zero utilities running under the addition. I also know that rooftop decks are generally frowned upon but I couldn’t resist the temptation to make use of that giant outdoor space (and it made framing super easy).
Thanks!
Anthony
GBA Detail Library
A collection of one thousand construction details organized by climate and house part
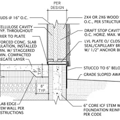
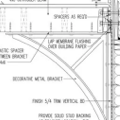
Replies
Anthony,
Your addition has attributes that are much closer to a structure built on piers, than an open crawlspace. There has been a lot of different discussions here on GBA about the best way to insulate floors open to below. Here is one to start: https://www.greenbuildingadvisor.com/article/the-best-way-to-insulate-a-floor
@Malcolm
Thanks for the link. You are spot on that the build is much like a pier structure, or at least some weird hybrid. That said, the article doesn't really address the foam question so much as it focuses on "the proposed foam solution doesn't meet code" so instead use a complex batt+OSB+foam system. If I had 40" to work with in the space, I'd be more inclined to consider that. But with <24" ... that sounds painful. It also doesn't really address air sealing unless I missed something?
Conversely, the LSU article (linked in that other article) basically says that in "open crawl spaces" (my build) I should use either closed cell or foil faced rigid foam for moisture reasons. Given that I do have a beam to contend with, limited headroom to work, and a strong desire to keep the insulation "pressed" against the subfloor, I'm leaning towards closed cell. So back to the closed cell topic - to get R19... that's 3", correct? Any guidance on cost for 3" x 400 sqft?
EDIT: Also wanted to add that while rigid foam /or/ OSB under the joists is attractive to keep moisture off the joists (and for that reason I may do one or both, headroom be darned), because these are TJI I'm not worried about thermal bridging. Also - while not currently an issue in my house - in the past, both this house and my neighbors have had rodent issues. So cellulose seems risky for that reason.
We need a location (or IECC climate zone) to get very deep into the recommendations. Is this climate zone 3A or 3B, or somewhere else?
>"Floor: I was thinking 3″ closed cell for vapor/moisture protection given the proximity to grade. "
2' above grade above a well vented crawlspace isn't a moisture problem. The average summertime dew point humidity of the local outdoor air would be more relevant. Closed cell foam is the opposite of "green", when it can be designed out of the assembly (and it most cases it can at least to some degree.)
At 3" closed cell foam is well below the IRC's code minimum R30 for zones marine-4, or zones 5 & higher, whereas the 2x6/R23 + R6c.i. walls are above the code min 2x6/R20 in zone 3, where R38 attic/R19 floor is IRC code min.
For the roof, R30 denim batts designed for 24" o.c. steel framing can be ordered through the big orange box stores. ($725 for a pallet sufficient to cover 323 square feet.) They're 8" deep x 24.25" wide. Unlike fiberglass or rock wool, denim has a fairly substantial thermal mass, enough to insert a delay of hours in peak ceiling temps during the cooling season. Denim batts also have a negative carbon footprint (as sequestered carbon), since it's a re-use of scrap cotton. They're a bit of PITA to trim compared to rock wool or fiberglass, but still a fairly straightforward DIY. With 2" of polyiso above the roof that would be fine for zone 3 or lower.
Better still would be a full fill of 9.5" of 2.8-3lbs cellulose (~R35), which is achieveable with a single-stage rental blower. Like cotton the thermal mass effects insert a delay in peak ceiling temp in the summer, as well as lowering the peak ceiling temp.
@Dana
I'm in climate zone 4 (northern VA). Sorry, I'm not sure about the dew point question!
EDIT: it occurs to me that my county may have slightly lower R-value reqs than what typical Zone 4 states. Here is a link to my county's literature:
https://www.fairfaxcounty.gov/landdevelopment/energy-conservation
For the ceiling, it sounds like batts of (anything) are fine, with a preference to denim as it's very green. I'm with you there - R30 + exterior 2" is fine. Question - faced or unfaced?
The only downside to batts is that I will have to seal the TJI joist/blocking intersection. I forgot to mention that the joists are cantilevered past the wall. So where the TJI's lap over the wall, I have flange-to-flange perpendicular TJI blocking with gaps in the left by the webbing. I'll probably just cut rectangles out of 1" foamboard and then spray foam the gaps from the outside.
As for cellulose... I have nothing against that. I just think I'd do a bad job of it especially since I have no idea how I'd suspend it in the ceiling w/o drywall and/or make the inspector happy.
Hi Dana,
Sorry to pester - I just wanted to make sure I got your thoughts on kraft faced vs. unfaced R30 batts. I'm guessing unfaced since the denim batts only seem to be unfaced? Or maybe it doesn't matter much. The ceiling will eventually be finished with sheetrock and latex paint.
Thank you!
If the ceiling is also the floor of a vented attic, you don’t really need to worry about using faced batts.
Just because the batts don’t have a facer doesn’t mean one isn’t needed in some applications. If you do need a “facer”, but are using unfaced batts, a smart vapor retarder like certainteed MemBrain is usually a good choice.
Bill
Bill, the ceiling is an unvented flat roof that has 2" polyiso rigid on the exterior. I guess at the end of the day, I'm really just asking if faced will hurt anything or if it could only be just as good or better than unfaced. Because if there's no harm in it, then I'll likely use faced "just in case" there's some unexpected vapor condition coming from the interior.