Insulation opportunity: re-roofing a 1922 house

Hello,
I’ve scoured the archives as best I can and despite lots of great information I’ve had trouble applying what I’ve learned to my specific project. Our house is a 1922 craftsman style home with a finished attic. There is currently no access to the unfinished edges or peak of the attic so we’re hoping to upgrade our insulation situation while the roof is off.
The house has gable vents that access the unfinished corner edges and peak (4 per side of house).
We think that we’ll have skip sheathing under original cedar shingles and 2-3 layers of asphalt shingles. Under the skip sheathing are 2×4 rafters and they are sometimes over vaulted wood lath and plaster ceilings and, at the peak and in corners, over unconditioned spaces. Currently there is some amount of vermiculite insulation in the ceiling space that will be removed safely. We think there is no insulation in the walls.
We were hoping to streamline the process and save money by leaving the skip sheathing in place, but that is negotiable. We are not likely to meet code (R-38 – Cashmere, WA) for insulation, but we want a more comfortable attic in summer and to save a bit of money in winter (although electric rates are very low here). The overall project also includes updating knob and tube wiring in the attic space and hopefully being able to blow insulation into walls once knob and tube is decommissioned.
So, what would you do?
We are looking at rewiring and then dense packing with cellulose (R-14 in 2×4 rafters) and then potentially adding one layer of rigid foam to reduce thermal bridging. This would likely be a big improvement over our current condition. Can rigid foam be installed directly over skip sheathing?
The roof will be finished with Pabco Premier shingles in a light color. We also plan on adding ridge venting and eave vents if we can build in enough airflow.
Currently we have one contractor proposing to do the dense packing and foam. He intends to install 2″ rigid panels over the sheathing and then strapping and OSB, but then I found several different versions of nailboard made by Atlas, Hunter, etc. How do you all rank these products relative to simply building the layers on site? It seems like a labor vs. materials cost evaluation, but is there more to it than that? For example, I talked with reps from 2 of the companies and one said it would be fine to install directly over skip sheathing with some vapor barrier below and the other said not to because all of these panels are “non structural”.
Thoughts? I think my preference is to pack the rafters as best we can, then add one layer of rigid foam, but we’re close to throwing in the towel on the over-rafters foam. This is also complicated because there don’t seem to be any really knowledgeable insulators in North Central WA.
Thanks!
GBA Detail Library
A collection of one thousand construction details organized by climate and house part
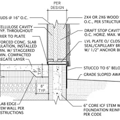
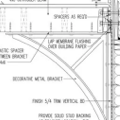
Replies
I am sure Martin will be able to advise you. In the meantime, check out this article. https://www.greenbuildingadvisor.com/articles/dept/musings/how-install-rigid-foam-top-roof-sheathing
Cashmere WA is zone 5B, which would need to hit R38 as a whole-assembly R (with all thermal bridging factored in ) to meet IRC code min. Under IRC 2009 R38 between joists or rafters would have met code.
(I'm not sure about the current WA code requirements, but I believe there are performance basis work-arounds).
In a 5B climate you can go with an unvented insulated roof if at least 40% of the total R is above the roof deck. A lot of Craftsman style 1920s homes had 2 x 6" rafters (full dimension, or full dimension), but apparently yours are 2x4 everywhere(?). Is that full dimension, or milled (3.5" nominal)?
Dense packed cellulose at 4" deep runs about R15, and from a moisture point of view would be fine with a minimum of R10 or greater on the exterior. So for a polyiso you'd need 2", a polyiso nailbase panel that would need to be a 2.5". If EPS it would need to be 2.5", if nailbase, a 3" panel. If you used dense packed fiberglass you'd be in R17 territory in the cavities, and would need better than R11 above the deck to be fully safe, which means bumping it a half inch on those minimums to have any margin. With less than that you would need a smart vapor retarder or half-perm vapor retardent paint on the interior side.
It's usually cheaper to go with foam + sheathing than with nailbase panels- a lot depends on the cost of labor. To be sure it's easier to just follow the fastener specifications & spacing instructions for nailbase panels than having an inexperienced crew try to figure out how to make separate foam + OSB work. It's not rocket science though, and you can use nailbase panel instructions to figure out what will most likely work with a foam + OSB solution.
If you have foam or nailbase panels over the top, you don't need or want eave to ridge venting- it's blocked by the foam. If you want to vent the nailer deck you need to strap the foam down with 2x furring through-screwed to the rafters, then mount the nailer OSB to the sheathing, at which point venting the nailer deck has some benefit.
Thanks. There are several nailbase products that incorporate venting by wood spacers between the foam and OSB... we were intending to use that space to incorporate ridge venting.
Our 2x4s are actually 3.5" and I think the rafters are 2x4's, although that is only based on what I see under the eaves.
What do you think about installing foam directly over skip sheathing? I don't know the details, but I'm expecting it to be 1x6" boards spaced every 6".
Jeremy,
Dana gave you good advice. The key is making sure that you have enough rigid foam above your roof sheathing to avoid moisture problems in your roof assembly. Dana recommends that 40% of the roof assembly's R-value be provided by the rigid foam layer in your climate zone (Zone 5); my article recommends 41%, but our calculations are close. Here is a link to an article that describes the principles involved: Combining Exterior Rigid Foam With Fluffy Insulation.
If you create this kind of roof assembly -- one with rigid foam above the roof sheathing -- you don't need to include a ventilation channel. If you choose to vent this type of roof, the ventilation channel belongs above the rigid foam.
The nailbase manufacturers are correct when they say that their panels aren't structural. So the question is, "Is skip sheathing structural?" My answer is, "Yes, of course skip sheathing is structural. It may not meet modern engineering standards, but you don't expect that roof sheathing on old houses was ever analyzed by an engineer. The skip sheathing has lasted more than 90 years, though, so it is 'good enough for an old house.'"
It's up to you whether or not you want to get an engineer involved. In light of the fact that you house has 2x4 rafters, it wouldn't hurt. You may not like what the engineer tells you, however -- you're probably going to be told that your house needs new 2x10 rafters and new plywood sheathing, and those costs are going to be high.
Thanks to you both!
Sorry I'm slow to get this... so you're saying that if I have 40% (or more) of my R value above the rafters then I don't need vapor barrier below the OSB? I like the idea of dense packing my rafters and simply adding 2" of polyiso.
Then, my impression is that the ventilation is mostly about meeting roofing shingle specs. If I go with your suggestion of 40% R value above the roof, then I have R-14 (or so) from dense pack and a 2" layer of polyiso (R- 13.1)... I've easily reached the goal of 40%. So, at this point I need no vapor barrier and no ventilation? I read the Pabco warranty and it seems like they want a vented structure. It would be great to avoid that for the sake of space and cost, but if ventilation will extend the life of the roof or help slightly with cooling in the summer then I'm all for it.
Jeremy,
No, you don't need an interior vapor barrier. If you want to delve deeper into the issue, you can read this article: Do I Need a Vapor Retarder?
Briefly, this is the story:
(1) Even in cold climates, the building code does not require an interior vapor barrier. Code often require an interior vapor retarder -- a less stringent layer than a vapor barrier -- for some types of assemblies in cold climates.
(2) Wall assemblies and roof assemblies that include exterior rigid foam are designed to dry to the interior, not the exterior, so it is vitally important that this type of assembly not have an interior vapor barrier. For more information on this topic, see How to Build an Insulated Cathedral Ceiling.
(3) Some asphalt shingle manufacturers insist that there needs to be a ventilation channel directly under the roof sheathing. You have two choices: you can provide the ventilation channel or ignore the manufacturer's recommendation. True, you won't get a shingle warranty without the ventilation channel, but roofing shingle warranties are basically worthless anyway. For more about the connection between a ventilation channel and shingle life, see All About Attic Venting.
Thanks again.
Our insulation contractor quoted an extra $1000 to replace the dense pack cellulose with spray foam in our 230 sf of cathedral attic ceiling. Assuming it is closed cell foam, would it be better to do the foam with no rigid outside or dense pack cellulose with rigid outside?
Most of the attic square footage is in the corners or peaks where regular blown-in insulation should be fine. If we run rigid foam over dense pack cellulose we'll likely have to cover the entire surface. Can we simply spray foam the 230 sf of cathedral ceiling and blow in the 900+sf of the rest of it?
Thanks again!
Jeremy,
Q. "Would it be better to do the [closed-cell spray] foam with no rigid [foam] outside or dense pack cellulose with rigid [foam] outside?"
A. The approach with rigid foam on the exterior side of the sheathing is always preferable, because it addresses thermal bridging through the rafters. If you install spray foam on the underside of your roof sheathing, you haven't addressed thermal bridging.
Q. "Most of the attic square footage is in the corners or peaks where regular blown-in insulation should be fine. If we run rigid foam over dense pack cellulose we'll likely have to cover the entire surface. Can we simply spray foam the 230 sf of cathedral ceiling and blow in the 900+sf of the rest of it?"
A. Yes, you can do that, saving money in the process. The performance won't be as good as it would be if you installed rigid foam on the exterior side of your roof sheathing, but I can understand your desire to go that route to save money.