Insulation on basement slab question: Polyethylene vs. Delta FL under rigid XPS?

We have a 6 year old cottage in Ontario with walkout basement with bedroom and rec room on the window end and utility area at other “subterranean” end. It is not heated in the winter except weekends when we light up the wood stove. Walls are insulated to R22. Floor is not. Basement floor temperature has been observed to drop to near 0 degrees C at exposed daylight wall in middle of winter.I don’t know if there is poly or clear stone under slab but am certain there is no insulation. I use dehumidifier to keep moisture down to 50% in summer. The goal is to get a thermal break so that the floor is not so cold in winter.
The concrete floor has no leaks and is white/ dry everywhere where exposed. In bedroom where I had laid a 12×12 carpet over 6 mil plastic for past few years. Last weekend I found the concrete is very dark and the underside of plastic was wet to touch. I am taking this to be vapour coming up through the floor and being stopped by the plastic. When the plastic was removed and floor left to air dry a few hours it started to lighten up. So after an initial moisture panic I think it is evidence that the plastic was doing its job and the white floor elsewhere is evidence of the slab drying into the basement.
My goal is to insulate the floor in bedroom and rec room. Reading through numerous web sites and information here there is a lot of information-some conflicting- as to best way to proceed. Under slab options are not possible. From information on this site I have settled in on 3/4” T&G OSB laid over 1.5″ rigid EXP insulation on vapour retarder on slab. What is challenging me is the vapour retarder. Poly sheeting is referenced numerous times on this site, as is the dimpled sheeting such as Delta FL. My questions are:
For this situation is there benefit of using the dimple sheet instead of the poly?
Does the air gap from the dimple make a difference?
Should I be sealing the perimeter of whichever one I use?
I ask the latter questions because some dimple sheet web sites suggest leaving a 1/4” gap to let vapour escape to dry the slab; whereas others suggest sealing it tight.
I see one Building Science web page promoted the air gap as good thing stating it enables a vapour stasis to be achieved; however, the page didn’t show details at perimeter. I’m assuming it must have been a sealed air space.
Any insights/advice would be appreciated.
GBA Detail Library
A collection of one thousand construction details organized by climate and house part
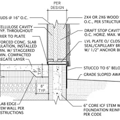
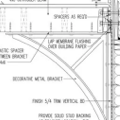
Replies
The benefit of dimple mat over 6 or 10 mil polyethylene is pretty academic. Concreted slabs don't need to dry- they are just fine even when fully saturated. The 1.5" of polystyrene to keep the subfloor warm enough in almost any Ontario climate for mitigating summertime moisture accumulation, but for the record, where is this house? (The Hudson Bay Riviera might want a bit more than that if you need to heat it in winter.)
This discussion comes up from time to time:
https://www.greenbuildingadvisor.com/blogs/dept/qa-spotlight/what-s-best-basement-flooring-system
BTW: The R-value of XPS falls over time to match that of EPS of equal density & thickness, as it's HFC blowing agents leak out over time. It's greener to go with 1.5" EPS rather than XPS, since it's blown with relatively benign pentane rather than HFCs, and has a stable R value over time. It's usually 25-35% cheaper at any labeled R-value too.
Thanks for fast reply! We're in the Parry Sound riviera (approx 45 degree lat). I had assumed EXP on presumption of higher compressive strength and more R per inch. But will re-evaluate per your tip.
So about that perimeter sealing of the vapor retarder: I believe it should be sealed so let me know if I've misunderstood along the way (ie, those sites that suggest leaving it open 1/4 inch around perimeter aren't right). Also, at the utility end of the room I will leave the concrete exposed. I plan to seal that edge of the vapour retarder to the concrete floor with an acoustic sealant. Sound good?
Again, open to better ideas/suggestions and thanks for your insights.
Grant,
If you've got a walkout basement with a slab that is very cold during the winter at the walkout side of the building, the first thing you need is vertical insulation, not horizontal insulation.
Dig a trench along your foundation wall on the walkout side, and install rigid foam insulation (at least 2 inches of dense EPS or XPS), from the top of the concrete to at least 2 feet below grade -- 3 feet is even better. Then backfill. Protect the above-grade insulation with pressure-treated plywood or metal flashing, and install horizontal Z-flashing at the seam between the top of the rigid foam and the lowest course of siding.
That's the most vulnerable part of your foundation -- where your heat is leaking.
Parry Sound! You must know Bobby Orr!
For underslab insulation, check out reclaimed xps or eps. You'll save a bundle and help the planet as well.