Insulation of deep ceiling cavities in an unvented roof assembly

All,
I am in the process of designing a house which will have long span low sloped (1 or 2 in 12) shed style roofs. I want to integrate a non-vented / exterior insulated roof assembly
While I’m waiting for my designer to provide the correct framing members, my research shows that I probably will need at least something like 9.5″ i-joists.
Per Martin’s article (https://www.greenbuildingadvisor.com/article/combining-exterior-rigid-foam-with-fluffy-insulation) I plan to use 4″ of R-Tech (2 x 2″) EPS rigid foam insulation above the roof deck (covered by ZIP System® Roof Sheathing) — I am in central Kentucky (Zone 4a). This will give me an exterior R value of 15.4
Within the cavities, I want to use a Rockwool product (no foam…) From what I can find, there are 3.5″, 5.5″ and 7 1/4″ thicknesses available. What does one do in these circumstances? My current thought is to layer a 3.5″ and a 5.5″ thickness – that’s 9″ but I would insure this was all flush to the underside of the roof deck sheathing (although admittedly this could sag). This would give me an “interior” R value of 38. I would then have a 41% exterior to interior ratio (Martin’s table point references a minimum of 31%)
Am I approaching this wrong? Is it wrong to do multiple layers of batt insulation? Should I exceed this 9″ and compress the batts? Should I be looking at blown-in mineral wool (although I was considering this job to be something I do myself)?
Any advise would be helpful.
Bonus question – when one does an “outsulation” assembly – (roof deck- rigid insulation – exterior sheathing) – what underlayment (if anything) should be between the roof deck and the rigid insulation?
thanks much!
Carl
GBA Detail Library
A collection of one thousand construction details organized by climate and house part
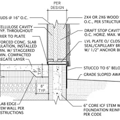
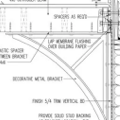
Replies
Carl, using the values you list, R-15.4 exterior and R-38 interior leaves 29% of the R-value on the exterior. The danger of skimping on the ratio of interior to exterior insulation is that the condensing surface, in your case the inside of the roof sheathing, will be cold enough to accumulate moisture for part of the year. Personally I am not comfortable using less than the code-prescribed ratio unless someone who knows what they are doing has done a hygrothermal analysis. Although I try to maximize insulation and minimize foam in the homes and renovations I design, when faced with this problem I either bump up the amount of foam or cut back on the total R-value to keep to safe ratios.
You're probably looking at Type 1 R-Control EPS, at 10 psi compressive strength and R-3.9/in. The R-value is measured at a mean temperature of 75°F, but there are no condensation risks at that temperature. At mean 25°F, when condensation is a concern, the same product tests at R-4.4/in. At 4", that would give you R-17.6 on the exterior. Mineral wool also performs better in colder temperatures, but Rockwool does not provide R-values other than the official test at mean 75°F, and in any case, with exterior insulation the mineral wool will stay much warmer than the foam. But even using these values, you only have 32% of your R-value on the exterior. I might be willing to push the limits a bit in some cases, but not by 24%.
To meet prescriptive ratios using 4" EPS on the exterior, your total R-value can't exceed R-38. If your insulation continues over the entire top plate, the IRC allows R-38. A single layer of 6" mineral wool on the interior, in contact with the roof sheathing, would work.
But obviously it would be better if you can reach at least R-49 total. That requires R-20 on the exterior and R-29 on the interior. If you're limited to 4" foam on the exterior, you can use Neopor, a graphite-impregnated EPS available up to R-5/in. Or use polyiso; even with derating for low temperatures, it will exceed your needs at 4".
There is nothing wrong with stacking multiple layers of batt insulation. In fact, because it's hard to install batts well, two layers is probably preferable.
As for your bonus question, I just did a similar assembly on a renovation, using polyiso, and used full ice and water shield over the entire roof. In my case it was important to create a waterproof and airtight layer at this location. If you are doing new construction, there is really no need for a membrane at this location, but it depends on your overall approach to airtightness. The roof deck is an easy place to create an airtight layer.
Thanks - let me digest your answer more, but am embarrassingly acknowledging my basic math mistake..
Note that sandwiching wood products between impermeable (< .1 perm) layers is less than ideal. Even < 1 perm in one direction will help.
So external polyiso seems to be the way to go - I'm not (at this point) limited to the depth of my exterior insulation, but even 4" seemed like a lot. I like that I can get around a R-20 with 3 inches (even if I do have to up my budget by quite a lot!) 2 questions:
Is there an advantage of doing 2 layers of 1.5" with staggered seams or am I being silly and using 1 - 3" layer would be easier.
Is there an issue of just doing a single batt of the 7 1/4" rockwool in the ceiling cavity - it has a R of 30 - that keeps my ratios good and would be easier and offset some of the cost of using polyiso on the exterior. I seem to remember reading somewhere that you don't want a semi-filled cavity when insulating, but of course I can't find that now...
thanks!
Carl, you might want to look around for used polyiso. The older stuff actually has better R-value and you can get good deals on it. Two layers with staggered and offset seams is definitely preferable to a single layer. Ideally you should also tape all seams, but at minimum at least tape the outer layer. New foam will shrink and it's hard to get seams perfectly tight so overlapping avoids thermal bypasses.
If you choose to not fill the cavity, you need to make sure the insulation is in contact with the sheathing, to avoid excessive moisture accumulation. Gravity is working against you so might want to just fill the whole cavity. But if you can get Rockwool made for metal framing, which is wider than that used for wood framing, it will have a good friction fit. I just don't know if I'd trust it to stay that way for decades without physical support.
>"...look around for used polyiso. The older stuff actually has better R-value and you can get good deals on it."
The higher performance is not universally true, and it's risky to presume an R-value higher than R5/inch for any used polyiso for dew-point control purposes, even if it's labeled at some much higher number.
While it's true that some of the pre-Montreal protocol goods (30+ years old) blown with (climate and ozone layer damaging) CFCs are still performing at R6/inch or better, there were also cases where the labeling overstated the actual aged performance, and some of the (climate but NOT ozone damaging) HFC. & HC blown stuff labeled R5.7/inch doesn't do better than R5/inch at temperatures that matter for dew point control.
R5/inch would be a reasonable seasonal-performance presumption for used polyiso, which is still higher performance than EPS, despite the crazy performance derating curve. See:
http://i.imgur.com/xyzIfRC.png
The performance of R4.2/inch labeled Type-II EPS would be comparable to the "Mineral Wool Batt" curve (maybe a hair below) , and the Type-I R-Tech would be comparable to (maybe a hair above) the "SPF" curve in that graph. The polyiso curve plotted is 2lb roofing polyiso that was only labeled R5.3/inch @ 75F mean-temp through the foam- most polyiso (new or old) outperforms that mark. But notice that even the worlds-crummiest straw-man polyiso curve that was plotted still performs at R5/inch when the mean temp through the foam layer is ~42F. If the binned
hourly average wintertime temperature in your area in winter is above 35F (which it is, even in cooler than average Covington, KY) and the average indoor temp is 70F, with 4" of polyiso up top and R40 rock wool in the rafters the average temp through the polyiso will be above 42F.
thanks!
What I did on my recent project, and would recommend, is to use three layers of 1 1/2" polyiso, with 2x4 sleepers embedded in the outermost layer. That allows you to use fewer fasteners through the sleepers into the roof framing, and the sheathing can be nailed to the sleepers conventionally.
Michael, so that build up is sheathing on roof structure, two layers (taped? Cap nails?) then sleepers through the 3” of foam (into the roof structure?) then more foam on the sleepers plane and then sheathing + shingles?
Sean, yes, existing (mostly) roof, wrapped with peel and stick, two layers of polyiso staggered and offset (not taped, because it's a vacation house that won't get used much in winter and the budget was tight, but normally I would tape at least the second layer). Then 2x4s aligned with each rafter, Simpson Trusslok screws 24" o.c., with a layer of polyiso between sleepers. The infill foam is not taped or super tight, but slightly thicker than 1 1/2" so once the top layer of sheathing went on it was held in place. It's the average R-value of the assembly that matters, so small gaps next to the sleepers don't make a big difference as long as air can't get under the foam. The foam was minimally tacked in place with common nails. The sheathing is taped Zip, then the roofers used a conventional underlayment as well.
Originally I was going to do nailbase insulation instead but we switched to this system for lead time reasons, and it's a stronger assembly. It's time consuming, though. On a current project we were going to do something similar, but switched to over-framing the roof with 2x6 rafters on horizontal sleepers, and used 6" mineral wool with a gap above for venting.
Thanks Michael.
thanks - this helps immensely!
Carl
Carl, I just re-read your original question... I hate to throw a wrench in the works but I had missed that you are dealing with a low-slope roof. There are special considerations for low-slope roofs because the stack effect does not work without an elevation difference between the intake and exhaust. Martin covers it thoroughly here: https://www.greenbuildingadvisor.com/article/insulating-low-slope-residential-roofs.
Michael - my plan is for an un-vented roof assembly - in the article you reference:
"In many ways, it’s easier to build an unvented low-slope roof than a vented low-slope roof. If you go this route, there are several possible ways to proceed:
...
You can install a more moderate layer of rigid foam insulation (2 to 4 inches) above the roof sheathing, supplemented by a layer of air-permeable insulation below (and in direct contact with) the roof sheathing."
I believe this was actually one of the references I used when designing my system - and the above quote seems to confirm it - correct?
Oh, sorry, yeah I was confusing this thread with another. You're good. In case you missed it, check out Dana's response #12.
Well I am (finally) just a little way from implementing my unvented roof assembly. This has evolved to the following: Rockwool R-30 batts between the rafters - OSB roof deck - 3" (2 x 1.5" ridgid Polyiso foam - seams offset) - Zip Roof Sheathing - Ice and Water shield over entire surface (see following) and metal standing seam roofing.
This is a 2:12 low slope deck hence the full coverage of Ice and Water shield.
This gives R 17.4 (Atlas ACFoam®-II) above and with the R-30 below that's a 37% to 63% ratio.
My question is regarding the Ice and Water shield over the whole surface. Huber recommends against this as "The reason we don’t recommend using ice and water over the entire roof is that the material is typically vapor impermeable, as is the foam. This basically creates a “moisture sandwich” with the exterior layer of sheathing in the middle, so any moisture that does make its way to the panel will not dry to either side. We assume that any sheathing will be exposed to some level of water vapor, so the best practice is to allow it to dry to one side or the other."
However from what I understand on a low sloped roof like mine you would want the whole surface covered. (My design consultant actually wanted 2 layers...) My thought is that with using the Zip Roof with seams sealed and full coverage of the Ice and Water shield, I should be good.
What's the thoughts on how I should integrate the Ice and Water shield?
BYW, Huber also says I could use felt paper in this assembly - "The felt paper isn’t required between the two layers of foam, but further prevents air (which carries water vapor) from traveling upward to the exterior layer of sheathing. It could also be installed before the foam on the primary roof deck, and is typically permeable so it will not impede drying to the inside." Any thoughts on this as well?
thanks all!
Carl
what kind of standing seam metal roof are you using on a 2/12 deck, Carl?
Thanks
I would put the I&W onto the OSB deck. This way it acts both as the main air barrier and warm side vapour barrier. The foam and Zip above the I&W can tolerate the occasional water leak without issues.
All metal roofing companies require a synthetic underlayment, to allow for a bit more drying, I would go with one of the permeable products here.
Felt generally won't work as it tends to melt and stick to the roof.